POLL ADDED !!! - Holton BB-345 twin-spin (first actual picture on p.2)
- bloke
- Mid South Music
- Posts: 19293
- Joined: Thu Aug 13, 2020 8:55 am
- Location: western Tennessee - near Memphis
- Has thanked: 3843 times
- Been thanked: 4088 times
Re: Holton BB-345 twin-spin (first actual picture on p.2)
I absolutely must stop posting on SM and discussion lists from my phone, as this little GDSOB changes words into other words during the very instant that I am posting, and I don’t notice what the phone did until - sometimes - weeks later. 
- These users thanked the author bloke for the post:
- the elephant (Fri Jul 09, 2021 9:58 am)
- the elephant
- Posts: 3378
- Joined: Thu Aug 13, 2020 8:39 am
- Location: 404 - Not Found
- Has thanked: 1896 times
- Been thanked: 1336 times
Re: Holton BB-345 twin-spin (first actual picture on p.2)
Yep, same for me. Add to this effect the fact that my MacBook has the dreaded "butterfly" keyboard that was such a disaster for them that after a few years of paying to replace many thousands of them for free Apple wisely decided to step backward to the more traditional scissor-type keys. I am on my third one and no more will be forthcoming from them for free, but now for $700. The first one lasted about two years, the second one lasted a week (A FREAKING WEEK!) and the last one has limped along for two years because I cannot get it fixed under warranty.
I currently have nine keys that have to be hit very hard about five or six times to get the letter to show up on the monitor, and I have two modifier keys that do not always work, and a space bar that cannot be clicked on the right side (only left, now, or you get no spaces) and — the best of all — any time I type "y" or "l" the cursor jumps up to a random line and continues to enter from that point. I have to stop, locate the mess, delete it, move the cursor back to where it is supposed to be, and type the word with the offending character very slowly and deliberately or the cursor will jump again. Using this computer has been a real drag for the last 18 or so months as this has become worse.
I spend an awful lot of my time retyping unposted text, editing posted text, or getting called out by my grammarian friends for all my typos. They love to rag on me for this. I have such nice friends back home in SA. HAHAHA!!!
I *finally* dumped my ten-year-old phone two days ago and that part of my life is dramatically better. If this next symphony and freelance season work out (no further moratoriums on public gatherings) then I will try to get a new computer (or a used one that predates this damned keyboard design). Until then I will have to post less, edit more, and try to waste time doing other things.
I currently have nine keys that have to be hit very hard about five or six times to get the letter to show up on the monitor, and I have two modifier keys that do not always work, and a space bar that cannot be clicked on the right side (only left, now, or you get no spaces) and — the best of all — any time I type "y" or "l" the cursor jumps up to a random line and continues to enter from that point. I have to stop, locate the mess, delete it, move the cursor back to where it is supposed to be, and type the word with the offending character very slowly and deliberately or the cursor will jump again. Using this computer has been a real drag for the last 18 or so months as this has become worse.
I spend an awful lot of my time retyping unposted text, editing posted text, or getting called out by my grammarian friends for all my typos. They love to rag on me for this. I have such nice friends back home in SA. HAHAHA!!!
I *finally* dumped my ten-year-old phone two days ago and that part of my life is dramatically better. If this next symphony and freelance season work out (no further moratoriums on public gatherings) then I will try to get a new computer (or a used one that predates this damned keyboard design). Until then I will have to post less, edit more, and try to waste time doing other things.

- bloke
- Mid South Music
- Posts: 19293
- Joined: Thu Aug 13, 2020 8:55 am
- Location: western Tennessee - near Memphis
- Has thanked: 3843 times
- Been thanked: 4088 times
Re: Holton BB-345 twin-spin (first actual picture on p.2)
Here's the large upper bow - guard wire installed - to the BB-345 that we're going to be offering for sale (as the customer-owned upper bow - for the customer-owned BB-345 that we are ALSO repairing - is already repaired). This one (and I keep forgetting to check the serial number on the valveset) might be a 1960's-vintage instrument, because the bell features the older LARGE script engraving.
again:
Earlier, I turned you frankentubists on to some brass molding that is a virtual perfect match for o.e.m. Holton guard wire (smaller than King sousaphone guard wire), but - just as I did before - I'm now "warning" (probably...??) most frankentubists OFF of it.
> Being SOLID (and NOT concave on the underside) this stuff is QUITE stiff, and must be bent (nearly, as if a mouthpipe) OFF the instrument, whereas regular hollow-back guard wire can easily be bent AS it is installed. Bending it to fit OFF the instrument requires (ok...not bragging - just sayin') a damn-good eye, and considerably more time.
> Being SOLID (a skinny solid "D" shape, and not concave at all on the underside), there is CONSIDERABLY more mass than with guard wire, and thus the amount of time for the energy transfer (heating) varies wildly from the bow (or cap) to the guard wire, and (again...not bragging - just sayin') soldering this stuff on to a bow requires considerably more expertise and much more sensitive touch, that is required to install regular guard wire. It also requires several applications of flux, as well as more of a "stabbing" (rather than a "pulling") soldering technique.
> If imitating an o.e.m. Holton guard wire end point, more grinding/shaping is required - than with regular "hollow" guard wire, because it can't be flattened down with a hammer or mallet. Again, it must be ground down to the desired shape.
> The material stiffness becomes even more of an issue at the ends, as the two sharp points MUST lay down ON THEIR OWN against the bow, and really cannot effectively be "teased" down with a screwdriver (etc.)...
...so I would recommend that most people stick to King sousaphone guard wire, unless they possess a particularly fine "touch", regarding soldering. I suppose there are three levels of lead soldering:
[1] plumbing
[2] band instruments
[3] Tiffany
This is probably something like (again: just sayin'...) a 2.6 - 2.8
-------------
I'd hoped to get the inner bows double-loop mounted to this, today, but that's a much easier operation (actually) than installing this guard wire, and I'll try to knock out that work tomorrow.
Again, I'm trying to get BOTH of those 345 restorations' bodies soldered together, so I can stand BOTH of them on their bells on corrugated cardboard - over in a corner - for two or three weeks, and (thus) out of harm's way, while I necessarily blow through some school repairs.


again:
Earlier, I turned you frankentubists on to some brass molding that is a virtual perfect match for o.e.m. Holton guard wire (smaller than King sousaphone guard wire), but - just as I did before - I'm now "warning" (probably...??) most frankentubists OFF of it.
> Being SOLID (and NOT concave on the underside) this stuff is QUITE stiff, and must be bent (nearly, as if a mouthpipe) OFF the instrument, whereas regular hollow-back guard wire can easily be bent AS it is installed. Bending it to fit OFF the instrument requires (ok...not bragging - just sayin') a damn-good eye, and considerably more time.
> Being SOLID (a skinny solid "D" shape, and not concave at all on the underside), there is CONSIDERABLY more mass than with guard wire, and thus the amount of time for the energy transfer (heating) varies wildly from the bow (or cap) to the guard wire, and (again...not bragging - just sayin') soldering this stuff on to a bow requires considerably more expertise and much more sensitive touch, that is required to install regular guard wire. It also requires several applications of flux, as well as more of a "stabbing" (rather than a "pulling") soldering technique.
> If imitating an o.e.m. Holton guard wire end point, more grinding/shaping is required - than with regular "hollow" guard wire, because it can't be flattened down with a hammer or mallet. Again, it must be ground down to the desired shape.
> The material stiffness becomes even more of an issue at the ends, as the two sharp points MUST lay down ON THEIR OWN against the bow, and really cannot effectively be "teased" down with a screwdriver (etc.)...
...so I would recommend that most people stick to King sousaphone guard wire, unless they possess a particularly fine "touch", regarding soldering. I suppose there are three levels of lead soldering:
[1] plumbing
[2] band instruments
[3] Tiffany
This is probably something like (again: just sayin'...) a 2.6 - 2.8
-------------
I'd hoped to get the inner bows double-loop mounted to this, today, but that's a much easier operation (actually) than installing this guard wire, and I'll try to knock out that work tomorrow.
Again, I'm trying to get BOTH of those 345 restorations' bodies soldered together, so I can stand BOTH of them on their bells on corrugated cardboard - over in a corner - for two or three weeks, and (thus) out of harm's way, while I necessarily blow through some school repairs.




-
- Posts: 1432
- Joined: Thu Aug 13, 2020 10:39 pm
- Location: SoCal
- Has thanked: 1554 times
- Been thanked: 467 times
Re: Holton BB-345 twin-spin (first actual picture on p.2)
It would be highly “exciting” but you could run it over a carbide coving router bit on a router table if you had feather boards to hold it down and against the fence. That would hollow out the back.
You’d have to be darn careful and have the feather boards set just right but it could be done.
You’d have to be darn careful and have the feather boards set just right but it could be done.
- These users thanked the author York-aholic for the post:
- bloke (Fri Jul 09, 2021 9:29 pm)
Some old Yorks, Martins, and perhaps a King rotary valved CC
- bloke
- Mid South Music
- Posts: 19293
- Joined: Thu Aug 13, 2020 8:55 am
- Location: western Tennessee - near Memphis
- Has thanked: 3843 times
- Been thanked: 4088 times
Re: Holton BB-345 twin-spin (first actual picture on p.2)
There’s a very friendly-to-me machine shop only a mile from the post office…about ten minutes away. They could do that more easily than could I, but it probably only takes an extra 45 minutes or an hour to install this stuff - compared to King sousaphone guard wire, and I’m not manufacturing Holton’s… I’m repairing/restoring one on average every six years or so. If I do decide to use some more of this material, though, I guess I could buy twenty (??) pieces of it and have them run all of them through one of their milling machines. They would charge me a very fair price…more than fair.
...probably less than a California tank of gas.
The owner is SUPER-nice. He even lets me use his banding machine, when I ship tubas out - strapped to pallets.
The owner is SUPER-nice. He even lets me use his banding machine, when I ship tubas out - strapped to pallets.
York-aholic wrote: ↑Fri Jul 09, 2021 9:11 pm It would be highly “exciting” but you could run it over a carbide coving router bit on a router table if you had feather boards to hold it down and against the fence. That would hollow out the back.
You’d have to be darn careful and have the feather boards set just right but it could be done.
- These users thanked the author bloke for the post:
- York-aholic (Sat Jul 10, 2021 8:26 am)
- bloke
- Mid South Music
- Posts: 19293
- Joined: Thu Aug 13, 2020 8:55 am
- Location: western Tennessee - near Memphis
- Has thanked: 3843 times
- Been thanked: 4088 times
Re: Holton BB-345 twin-spin (first actual picture on p.2)
This is the Holton BB-345 that WE own, which will be sold (unless I personally "freak out" over it...)
I didn't get these loops mounted to the bottom bow and bell, but I'd best wait for Mrs. bloke to be available to help with that.
This was a TON of work, because - as I stripped the lacquer off the inner bows - I found all the remaining tiny dents, remnants of dents, and flat spots - and took care of ALL of those issues. Also: ALIGNMENT - ALIGNMENT - ALIGNMENT !!!

I didn't get these loops mounted to the bottom bow and bell, but I'd best wait for Mrs. bloke to be available to help with that.

This was a TON of work, because - as I stripped the lacquer off the inner bows - I found all the remaining tiny dents, remnants of dents, and flat spots - and took care of ALL of those issues. Also: ALIGNMENT - ALIGNMENT - ALIGNMENT !!!





- These users thanked the author bloke for the post:
- York-aholic (Sat Jul 10, 2021 5:54 pm)
-
- Posts: 123
- Joined: Mon Aug 24, 2020 5:05 pm
- Location: Nashville
- Has thanked: 45 times
- Been thanked: 30 times
Re: Holton BB-345 twin-spin (first actual picture on p.2)
Don't play it out...
Music Director and colleagues will ask "where's the BIG one?"
To be followed by the "one that got away" stories

Do you have a Cronkite Bag that fits ? :smilie2:e
AW OH

I need to digitize some pics of the factory 345 CC
[flatG, etc. fun
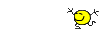
[family horn] for about 10 years.
The horn personified could play Serious or Bouncy & Playful...lots of headroom.
Joe H
- bloke
- Mid South Music
- Posts: 19293
- Joined: Thu Aug 13, 2020 8:55 am
- Location: western Tennessee - near Memphis
- Has thanked: 3843 times
- Been thanked: 4088 times
Re: Holton BB-345 twin-spin (first actual picture on p.2)
I am "playing with" the for-sale one - just a bit (as with the compact-yet-19-inch-bell-only-32-inches-tall-B-flat-that-I-built-for-myself), also seeing about getting it to "fit more inside itself" and to improve (that thing that y'all call) "ergonomics". It's requiring a bit of extra effort (beyond just sticking it back together the same way that some hapless assigned-to-stucking-it-together guy in Elkhorn originally stuck it together), but - well... - It's making the restoration project slightly more interesting...and I suspect (??) it might actually "look" (ie. curb appeal) slightly better than it did, off the dock.
- bloke
- Mid South Music
- Posts: 19293
- Joined: Thu Aug 13, 2020 8:55 am
- Location: western Tennessee - near Memphis
- Has thanked: 3843 times
- Been thanked: 4088 times
Re: Holton BB-345 twin-spin (first actual picture on p.2)
They're going to have to be like this for a bit, as there are other things to which I'm obligated to attend.
(I did go back and clean up all of the solder joints on the will-be-for-sale instrument.)

(I did go back and clean up all of the solder joints on the will-be-for-sale instrument.)

- Doc
- Posts: 2472
- Joined: Thu Aug 13, 2020 9:48 am
- Location: Downtown Browntown
- Has thanked: 846 times
- Been thanked: 767 times
- Contact:
Re: Holton BB-345 twin-spin (first actual picture on p.2)
Wouldn't it be something if I scheduled a trip to Blokeplace that serendipitously coincided with the time that thing becomes ready for testing/sale?
- These users thanked the author Doc for the post (total 2):
- York-aholic (Mon Jul 12, 2021 11:13 am) • prairieboy1 (Mon Jul 12, 2021 12:10 pm)
Welcome to Browntown!
Home of the Brown Note!
Home of the Brown Note!
-
- Posts: 484
- Joined: Thu Aug 13, 2020 8:37 pm
- Has thanked: 441 times
- Been thanked: 148 times
Re: Holton BB-345 twin-spin (first actual picture on p.2)
Hmm...

- These users thanked the author prairieboy1 for the post:
- Doc (Mon Jul 12, 2021 12:12 pm)
1916 Holton "Mammoth" 3 valve BBb Upright Bell Tuba
1935 King "Symphony" Bass 3 valve BBb Tuba
1998 King "2341" 4 valve BBb Tuba
1970 Yamaha "321" 4 valve BBb Tuba (Yard Goat)
1935 King "Symphony" Bass 3 valve BBb Tuba
1998 King "2341" 4 valve BBb Tuba
1970 Yamaha "321" 4 valve BBb Tuba (Yard Goat)
-
- Posts: 163
- Joined: Tue Aug 25, 2020 4:15 pm
- Location: Dunkirk, MD
- Has thanked: 31 times
- Been thanked: 46 times
Re: Holton BB-345 twin-spin (first actual picture on p.2)
Getting anxious to start getting updates again.
At the beginning of this project, I was thinking that I wanted to get a big, round, fancy thumb ring "bling". I'm been playing on a circa 2021 King sousaphone here at the Army School of Music. It has a giant thumb ring and is useless. If it had one just a bit bigger than my thumb, I would have a lot better control of the instrument. Even though I think that is more important on a sousaphone, I think I'll stick with the original, Holton ring.
At the beginning of this project, I was thinking that I wanted to get a big, round, fancy thumb ring "bling". I'm been playing on a circa 2021 King sousaphone here at the Army School of Music. It has a giant thumb ring and is useless. If it had one just a bit bigger than my thumb, I would have a lot better control of the instrument. Even though I think that is more important on a sousaphone, I think I'll stick with the original, Holton ring.
- the elephant
- Posts: 3378
- Joined: Thu Aug 13, 2020 8:39 am
- Location: 404 - Not Found
- Has thanked: 1896 times
- Been thanked: 1336 times
Re: Holton BB-345 twin-spin (first actual picture on p.2)
Joe, I wish I could have applied that level of detail to my Holton when I had it apart. It is much better (dare I say "very well done"?) but to my way of thinking it *should* have been better. I skipped some work to bend the inner branches and the small end of the bottom bow to completely fix the Rusk cuts and the weird factory shapes. Because of this, I had a devil of a time aligning stuff to look the way I wanted. I am satisfied with what I have, as it is just for me. The alignment issues are small and are more of a bruise to my ego rather than an actual issue. It is not ever going to be for sale until after I croak, so I won't have to deal with the aspect of having someone carefully scrutinize my work to justify my high-as-poop asking price.
It is my horn. I like it. I just wish I liked it a little more. I guess the more time I dump into a project like this the higher your expectations get, so that on a quickie "slick out" job (your term) a flaw that is small is not a big deal, but when you have like a thousand hours in it a small flaw become huge and glaring, even if no one else really notices it, your eye is drawn to it right away. It is easy for me to obsess over these small details, and that can erode some of my satisfaction with a horn over time. It's a good thing I like this tuba so much, I guess.
I am enjoying following this thread. Please keep us up to date and blessed with a wealth of hornporn, sir.
It is my horn. I like it. I just wish I liked it a little more. I guess the more time I dump into a project like this the higher your expectations get, so that on a quickie "slick out" job (your term) a flaw that is small is not a big deal, but when you have like a thousand hours in it a small flaw become huge and glaring, even if no one else really notices it, your eye is drawn to it right away. It is easy for me to obsess over these small details, and that can erode some of my satisfaction with a horn over time. It's a good thing I like this tuba so much, I guess.
I am enjoying following this thread. Please keep us up to date and blessed with a wealth of hornporn, sir.

- These users thanked the author the elephant for the post:
- Yorkboy (Tue Aug 17, 2021 4:27 pm)

- bloke
- Mid South Music
- Posts: 19293
- Joined: Thu Aug 13, 2020 8:55 am
- Location: western Tennessee - near Memphis
- Has thanked: 3843 times
- Been thanked: 4088 times
Re: Holton BB-345 twin-spin (first actual picture on p.2)
None of my work approaches “perfect“, and my ego probably prohibits me from showing too many of the flaws. That having been said, my overblown ego may be the thing that has encouraged me to fix stuff pretty good and to play fairly well - in spite of the lack of any gifts of “natural abilities“.
No Holton 345 is close to “perfect“ in the first place, but - maybe like crappy Harley Davidson’s from the same era - there is some draw to working on them (“Americana”...??), and trying to coax them into being the best they can be.
In the distant past - when I had fewer resources and had never chopped on anything before – I made a three-valve model 340 into a C, and later, I just did a really nice restoration on a not-too-badly-beat-up 345 B-flat (a tuba that is now somewhere around Long Island, New York).
This customer-owned B-flat seemed to offer some better-than-average tuning characteristics, but the bottom bow was so smashed in that I wonder if those tuning characteristics will remain - after it is reassembled.
The one that is being fixed up to sell – and I think there’s someone who is very interested in it, already - is a wild card, because when I bought it it wasn’t in playing condition. Years before Dave Secrest retired, I did have the pistons rebuilt on the one that I’m fixing up to sell, but never made myself find time to do the restoration job.
I think the strategy of pulling out a like instrument from the attic - while repairing one for a customer - is a good tack, which encourages (disciplines?) me to get some of my stuff fixed up and sold.
I’m going to be following this same strategy with a customer Miraphone 185 B-flat and one that is in the attic, in a few short months.
Anderson is backing off glass bead blasting service, so I’m going to have to teach myself how to do it. I’ve owned a nice big unit for several years, but never got it going. The person at Anderson -,who has been doing it - is encouraging, and tells me that - as long as I keep the pressure down and the nozzle distance away - that it’s not difficult, and the only real danger (outside of denting - if not following the previous guidelines) is going through thin spots...but these instruments really don’t have any thin spots, so I’m good on that.
I’m tempted to go ahead and subject the cute little compact Holton tuba to the same finish...??
In the meantime, I have at least another hard week of school repairs left here, and surely some “emergency“ add-ons from band directors who didn’t bother to look at their stuff last spring or summer.
Once all of those people settle down, i’m going to be “blueprinting“ (as best as can be managed) both of these 345 valvesets and mounting them. After that, I’ll be pulling worthless crap/scraps out of the attic and teaching myself how to glass bead blast.
No Holton 345 is close to “perfect“ in the first place, but - maybe like crappy Harley Davidson’s from the same era - there is some draw to working on them (“Americana”...??), and trying to coax them into being the best they can be.
In the distant past - when I had fewer resources and had never chopped on anything before – I made a three-valve model 340 into a C, and later, I just did a really nice restoration on a not-too-badly-beat-up 345 B-flat (a tuba that is now somewhere around Long Island, New York).
This customer-owned B-flat seemed to offer some better-than-average tuning characteristics, but the bottom bow was so smashed in that I wonder if those tuning characteristics will remain - after it is reassembled.
The one that is being fixed up to sell – and I think there’s someone who is very interested in it, already - is a wild card, because when I bought it it wasn’t in playing condition. Years before Dave Secrest retired, I did have the pistons rebuilt on the one that I’m fixing up to sell, but never made myself find time to do the restoration job.
I think the strategy of pulling out a like instrument from the attic - while repairing one for a customer - is a good tack, which encourages (disciplines?) me to get some of my stuff fixed up and sold.
I’m going to be following this same strategy with a customer Miraphone 185 B-flat and one that is in the attic, in a few short months.
Anderson is backing off glass bead blasting service, so I’m going to have to teach myself how to do it. I’ve owned a nice big unit for several years, but never got it going. The person at Anderson -,who has been doing it - is encouraging, and tells me that - as long as I keep the pressure down and the nozzle distance away - that it’s not difficult, and the only real danger (outside of denting - if not following the previous guidelines) is going through thin spots...but these instruments really don’t have any thin spots, so I’m good on that.
I’m tempted to go ahead and subject the cute little compact Holton tuba to the same finish...??
In the meantime, I have at least another hard week of school repairs left here, and surely some “emergency“ add-ons from band directors who didn’t bother to look at their stuff last spring or summer.
Once all of those people settle down, i’m going to be “blueprinting“ (as best as can be managed) both of these 345 valvesets and mounting them. After that, I’ll be pulling worthless crap/scraps out of the attic and teaching myself how to glass bead blast.
- Doc
- Posts: 2472
- Joined: Thu Aug 13, 2020 9:48 am
- Location: Downtown Browntown
- Has thanked: 846 times
- Been thanked: 767 times
- Contact:
Re: Holton BB-345 twin-spin (first actual picture on p.2)
Bead-blasted brass (sprayed with lacquer?) or bead-blasted silver?
Welcome to Browntown!
Home of the Brown Note!
Home of the Brown Note!
- bloke
- Mid South Music
- Posts: 19293
- Joined: Thu Aug 13, 2020 8:55 am
- Location: western Tennessee - near Memphis
- Has thanked: 3843 times
- Been thanked: 4088 times
Re: Holton BB-345 twin-spin (first actual picture on p.2)
sand/glass-bead -blasting the unfinished brass, prior to silver plating
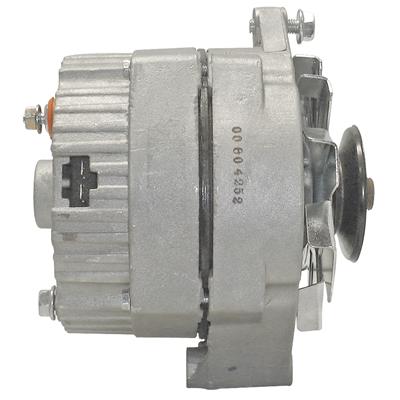
Note to @the elephant:
Please don't copy down this serial number !
Other than the distance of the nozzle and the air pressure (due to sheet brass being so easy to dent or blast right through it), it's the same operation that is done by big companies that sell used (aka: "remanufactured") automobile parts:
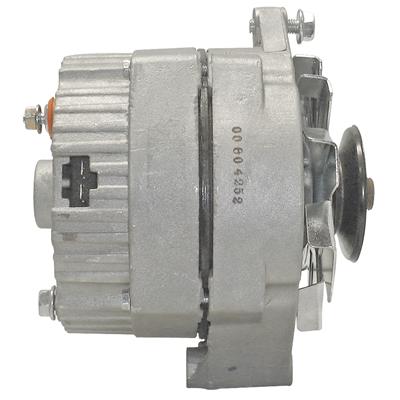
Note to @the elephant:
Please don't copy down this serial number !

- bloke
- Mid South Music
- Posts: 19293
- Joined: Thu Aug 13, 2020 8:55 am
- Location: western Tennessee - near Memphis
- Has thanked: 3843 times
- Been thanked: 4088 times
Re: Holton BB-345 twin-spin (first actual picture on p.2)
I have a pair of pretty seriously damaged old Yamaha 321 B-flat tubas to repair for a middle school - along with an easy double horn repair, a few add-on tuba repairs (Jupiter-y Jinbao-y stuff) from another school - which are not extensive, and one of those Yamaha 202 shoulder-mount-only Yamaha things - for a school with a whole bunch of high-end (vintage/pro-grade) saxophone and harmony woodwind repairs that Mrs. bloke is doing. ... I’ve already done the tricky repairs on the 202, and it now only needs dent removal - which I will probably do about an hour before Mrs. bloke tells me she’s finished with the last woodwind instrument for that school.
————
After all of that – which shouldn’t take that long, I will be back to Holton 345 valvesets, final assembly of both 345 tubas, and teaching myself how to glass bead blast.
Once the Anderson odyssey has been made - and everyone happily has their Holton instruments, I will be moving on to the pair of Miraphone model 184 B-flats (same as with the Holtons: repairing one for a customer, and simultaneously repairing another one to sell), and then, I’m going to take on those minor alterations to that Miraphone kaiser orchester B-flat (model 90 - from the early-mid 1960’s), which should allow it to much more easily be played perfectly in tune - with its four rotors. I suspect (??) I’ll be offering that beautiful instrument (w/custom slimline hard case) for sale.
I’m not going to get too far ahead of myself, here, because what typically happens is that people start asking me about buying stuff that can’t possibly be made ready to sell until several months out. Rest assured, the bloke-barn is jam-packed with “cool” (“cool”, as defined by tuba nerds).
Mostly, this is just a intermediate thread bump - to keep this thread from languishing, as I am quite eager to get back to the pair of Holton tubas.
————
After all of that – which shouldn’t take that long, I will be back to Holton 345 valvesets, final assembly of both 345 tubas, and teaching myself how to glass bead blast.
Once the Anderson odyssey has been made - and everyone happily has their Holton instruments, I will be moving on to the pair of Miraphone model 184 B-flats (same as with the Holtons: repairing one for a customer, and simultaneously repairing another one to sell), and then, I’m going to take on those minor alterations to that Miraphone kaiser orchester B-flat (model 90 - from the early-mid 1960’s), which should allow it to much more easily be played perfectly in tune - with its four rotors. I suspect (??) I’ll be offering that beautiful instrument (w/custom slimline hard case) for sale.
I’m not going to get too far ahead of myself, here, because what typically happens is that people start asking me about buying stuff that can’t possibly be made ready to sell until several months out. Rest assured, the bloke-barn is jam-packed with “cool” (“cool”, as defined by tuba nerds).
Mostly, this is just a intermediate thread bump - to keep this thread from languishing, as I am quite eager to get back to the pair of Holton tubas.
-
- Posts: 163
- Joined: Tue Aug 25, 2020 4:15 pm
- Location: Dunkirk, MD
- Has thanked: 31 times
- Been thanked: 46 times
Re: Holton BB-345 twin-spin (first actual picture on p.2)
Excited to start getting updates again soon
I was hoping the completion of the Holton would match up with my return home from the Army School of Music, but it looks like it may be closer to matching up with the birth of my first child
Of course if you decide that you are brave enough to lacquer it (especially if it would save me $$$$$ vs Silver), I'm always happy to hear you out.

I was hoping the completion of the Holton would match up with my return home from the Army School of Music, but it looks like it may be closer to matching up with the birth of my first child
Of course if you decide that you are brave enough to lacquer it (especially if it would save me $$$$$ vs Silver), I'm always happy to hear you out.
bloke wrote: ↑Tue Aug 17, 2021 8:07 am I have a pair of pretty seriously damaged old Yamaha 321 B-flat tubas to repair for a middle school - along with an easy double horn repair, a few add-on tuba repairs (Jupiter-y Jinbao-y stuff) from another school - which are not extensive, and one of those Yamaha 202 shoulder-mount-only Yamaha things - for a school with a whole bunch of high-end (vintage/pro-grade) saxophone and harmony woodwind repairs that Mrs. bloke is doing. ... I’ve already done the tricky repairs on the 202, and it now only needs dent removal - which I will probably do about an hour before Mrs. bloke tells me she’s finished with the last woodwind instrument for that school.
————
After all of that – which shouldn’t take that long, I will be back to Holton 345 valvesets, final assembly of both 345 tubas, and teaching myself how to glass bead blast.![]()
- bloke
- Mid South Music
- Posts: 19293
- Joined: Thu Aug 13, 2020 8:55 am
- Location: western Tennessee - near Memphis
- Has thanked: 3843 times
- Been thanked: 4088 times
Re: Holton BB-345 twin-spin (first ac tual picture on p.2)
I wish they were both done, along with the rest of the school repairs and the pair of 184s.
I can do some beautiful lacquer jobs on trumpets and trombones, but tubas really need epoxy lacquer and more of a lacquer booth.
I lacquered that shorty Miraphone (sort of) “frankentuba” (recording bell flair) that I sold to a local school, but there were probably a couple of minor runs in it, and probably due to me trying to put a ton of nitrocellulose lacquer on it - so it would hold up.
I just don’t have some gigantic HVAC system (again: nor much of a booth) to drop air moisture level down low enough to use no drying retarder, and drying retarder (which prevents blushing, due to humidity) encourages runs, dust, and bugs.
Finally, though blessed with better health than many my age, I’m about to turn 65, and really don’t savor the prospect of holding up a 20 pound tuba body for an hour or two (and having to completely prevent it from touching any part of my clothing or body) in front of a buffing machine. Again, with the exhaust going in the buffing room, there really is no such thing as air conditioning, so - within a few minutes - I’m dropping salty sweat droplets on freshly-polished surfaces.
...It would help, if someone would mow, spray weeds, and spray to kill these armyworms (as malathion and I don’t seem to get along too well), but I doubt that there will be any volunteers…and that stuff all takes time away from work.
I can do some beautiful lacquer jobs on trumpets and trombones, but tubas really need epoxy lacquer and more of a lacquer booth.
I lacquered that shorty Miraphone (sort of) “frankentuba” (recording bell flair) that I sold to a local school, but there were probably a couple of minor runs in it, and probably due to me trying to put a ton of nitrocellulose lacquer on it - so it would hold up.
I just don’t have some gigantic HVAC system (again: nor much of a booth) to drop air moisture level down low enough to use no drying retarder, and drying retarder (which prevents blushing, due to humidity) encourages runs, dust, and bugs.
Finally, though blessed with better health than many my age, I’m about to turn 65, and really don’t savor the prospect of holding up a 20 pound tuba body for an hour or two (and having to completely prevent it from touching any part of my clothing or body) in front of a buffing machine. Again, with the exhaust going in the buffing room, there really is no such thing as air conditioning, so - within a few minutes - I’m dropping salty sweat droplets on freshly-polished surfaces.
...It would help, if someone would mow, spray weeds, and spray to kill these armyworms (as malathion and I don’t seem to get along too well), but I doubt that there will be any volunteers…and that stuff all takes time away from work.