Sheet metal vs Tube Metal
Forum rules
This section is for posts that are directly related to performance, performers, or equipment. Social issues are allowed, as long as they are directly related to those categories. If you see a post that you cannot respond to with respect and courtesy, we ask that you do not respond at all.
This section is for posts that are directly related to performance, performers, or equipment. Social issues are allowed, as long as they are directly related to those categories. If you see a post that you cannot respond to with respect and courtesy, we ask that you do not respond at all.
Sheet metal vs Tube Metal
Hey all
I just got an email from a salesperson who said x tuba is made of sheet brass and y tuba is made of tube metal.
What is the difference between these two? I always thought brass was just brass.
Thanks.
I just got an email from a salesperson who said x tuba is made of sheet brass and y tuba is made of tube metal.
What is the difference between these two? I always thought brass was just brass.
Thanks.
-
- Posts: 1343
- Joined: Mon Oct 26, 2020 2:31 pm
- Location: Portugal
- Has thanked: 6 times
- Been thanked: 169 times
Re: Sheet metal vs Tube Metal
Brass is just brass!? Haven't you heard of York brass, that makes you sound like Arnold Jacobs?
One thing about tube brass is that tubas aren't tubes, so - correct me if I'm oversimplifying - as a tube is widened to make a conical tuba branch, the wide end gets thinner, and the tuba thus is made of pieces whose thickness varies gradually between joints and abruptly across them. A tuba made of sheet will be more or less the thickness of the sheet all over. And the stresses in the metal will be different, but that can maybe be addressed by cryo treatments.
One thing about tube brass is that tubas aren't tubes, so - correct me if I'm oversimplifying - as a tube is widened to make a conical tuba branch, the wide end gets thinner, and the tuba thus is made of pieces whose thickness varies gradually between joints and abruptly across them. A tuba made of sheet will be more or less the thickness of the sheet all over. And the stresses in the metal will be different, but that can maybe be addressed by cryo treatments.
- the elephant
- Posts: 3401
- Joined: Thu Aug 13, 2020 8:39 am
- Location: 404 - Not Found
- Has thanked: 1902 times
- Been thanked: 1345 times
Re: Sheet metal vs Tube Metal
The salesperson is trying very hard to sell you something. Right now, some makers are offering some horns made using current hydro-forming methods AND classic hand-hammering. These are not the same animal at all, acoustically, and the metal in hand-hammered stuff tends to be thinner and more or less evenly thinner, whereas using a hydraulic blow-out press gives you a perfect outer shape, but walls that taper in thickness from one end of the part to the other, making them respond slightly differently, and they are (usually) heavier.
Keep in mind that ALL tubas are made from flat, rolled-up ribbons of sheet brass. ALL of them. It is how they are joined into tubes and how the tubes are shaped that make these differences.
Some salespeople only understand this at a root level and when pressed for details will just make up something that sounds good to them (and you).
The main detail in manufacturing these instruments that trips these folks up (and causes issues when they give this mixed up, inaccurate information to buyers) is that you can draw or roll and seam small tubing. However, even the drawn tubing starts as sheet brass that goes through rollers and forms until it is a tube, then seamed up using one of several methods. (Yamaha used to use the term "plasma welded" but I think this is not really accurate, and just sales hype.)
So using the very loosely defined term "hand-" anything is just salesmanship unless they can actually explain specifically what they mean by that to you, which 99% of the time is not going to happen, despite their using glossy brochures or a nicely built website, which will always be just as vague. Handmade, hand-hammered, hand-fitted, hand-lapped, hand-rolled, et cetera, are all buzz words that have no meaning out of context. ALL tubas are handmade to a certain extent. ALL of them. Always.
It is the amount of handwork they receive that dictates price in most cases when there are options given to the buyer. For instance, the term "one-piece bell" was a huge buzz term in the 1980s. It still is. But there is no such thing, only a one-piece bell FLARE. A big disc of brass is placed onto a spinning lathe and someone forms it to a mandrel as it spins. That is brazed onto a rolled and seamed bell "tail" or "stem". So two pieces. Sorry, spin doctors. Two pieces.
A traditional bell is actually ONE PIECE from end to end, but there is a triangular gusset at the flare to fill in the gap made when hand-hammering the bell sheet around forms and mandrels to shape. It is cut and brazed into place at the appropriate time in the formation of the bell's shape.
Don't worry about car salesmanship tactics. Play the horns side by side to see which one you prefer. If you can't tell, get the cheaper one by all means. If you can't try them out in person then get a local friend (perhaps from here) to try them out for you and give you a private review and suggestions.
Honestly, I have A/B-ed a number of Meinl-Weston tubas available in both hydro- and hand-formed versions. Usually, the handmade one is a good bit lighter and they respond better for me, personally, but I know others who did not find enough of a difference between the two to merit the extra money, which can be considerable. I also have played one or two of both types where I preferred the cheaper version to the one with hand-hammered bells or outer branches.
As far as the rather confused explanation you were given regarding sheet brass versus tube brass, even rotary valve casings start as sheet (or bar) brass and are rolled, seamed, cut off, and machined to shape.
Keep in mind that ALL tubas are made from flat, rolled-up ribbons of sheet brass. ALL of them. It is how they are joined into tubes and how the tubes are shaped that make these differences.
Some salespeople only understand this at a root level and when pressed for details will just make up something that sounds good to them (and you).
The main detail in manufacturing these instruments that trips these folks up (and causes issues when they give this mixed up, inaccurate information to buyers) is that you can draw or roll and seam small tubing. However, even the drawn tubing starts as sheet brass that goes through rollers and forms until it is a tube, then seamed up using one of several methods. (Yamaha used to use the term "plasma welded" but I think this is not really accurate, and just sales hype.)
So using the very loosely defined term "hand-" anything is just salesmanship unless they can actually explain specifically what they mean by that to you, which 99% of the time is not going to happen, despite their using glossy brochures or a nicely built website, which will always be just as vague. Handmade, hand-hammered, hand-fitted, hand-lapped, hand-rolled, et cetera, are all buzz words that have no meaning out of context. ALL tubas are handmade to a certain extent. ALL of them. Always.
It is the amount of handwork they receive that dictates price in most cases when there are options given to the buyer. For instance, the term "one-piece bell" was a huge buzz term in the 1980s. It still is. But there is no such thing, only a one-piece bell FLARE. A big disc of brass is placed onto a spinning lathe and someone forms it to a mandrel as it spins. That is brazed onto a rolled and seamed bell "tail" or "stem". So two pieces. Sorry, spin doctors. Two pieces.
A traditional bell is actually ONE PIECE from end to end, but there is a triangular gusset at the flare to fill in the gap made when hand-hammering the bell sheet around forms and mandrels to shape. It is cut and brazed into place at the appropriate time in the formation of the bell's shape.
Don't worry about car salesmanship tactics. Play the horns side by side to see which one you prefer. If you can't tell, get the cheaper one by all means. If you can't try them out in person then get a local friend (perhaps from here) to try them out for you and give you a private review and suggestions.
Honestly, I have A/B-ed a number of Meinl-Weston tubas available in both hydro- and hand-formed versions. Usually, the handmade one is a good bit lighter and they respond better for me, personally, but I know others who did not find enough of a difference between the two to merit the extra money, which can be considerable. I also have played one or two of both types where I preferred the cheaper version to the one with hand-hammered bells or outer branches.
As far as the rather confused explanation you were given regarding sheet brass versus tube brass, even rotary valve casings start as sheet (or bar) brass and are rolled, seamed, cut off, and machined to shape.
- These users thanked the author the elephant for the post (total 3):
- peterbas (Sun Sep 12, 2021 3:08 pm) • Worth (Mon Sep 13, 2021 3:51 am) • spirtuba (Mon Sep 13, 2021 7:19 am)

- bort2.0
- Posts: 5254
- Joined: Thu Aug 13, 2020 9:13 am
- Location: Minneapolis
- Has thanked: 336 times
- Been thanked: 999 times
Re: Sheet metal vs Tube Metal
Hydro formed tubing is not uniformly thick the entire length of the tube. It's thicker at the starting end than the end, because of the way it's extruded. Not by much, but it's different. The theory is that after a whole bunch of big/small mismatch joints, it can add up and make things a little wonky. Also, the thicker parts obviously weigh more than the thinner... So the tuba overall has more weight.
Hand hammered tubing is more uniformly thick (or thin, rather), and makes for more seamless joints along the way, and uniformly lighter metal.
How much difference IRL? IDK... I think most tuba comparisons like this are only relevant as A/B tests side by side. Leave with one or the other, and forget the one left behind, and you'll always like the one you have and think the other was better haha.
Hand hammered tubing is more uniformly thick (or thin, rather), and makes for more seamless joints along the way, and uniformly lighter metal.
How much difference IRL? IDK... I think most tuba comparisons like this are only relevant as A/B tests side by side. Leave with one or the other, and forget the one left behind, and you'll always like the one you have and think the other was better haha.
-
- Posts: 189
- Joined: Thu Aug 13, 2020 6:26 pm
- Location: Tampa, FL
- Has thanked: 81 times
- Been thanked: 48 times
Re: Sheet metal vs Tube Metal
Thank you to the OP for asking and to each of the contributors (and whoever follows) for laying out common sense answers, and expanding on them into general brass instrument fabrication. Certainly fascinating on many levels.
2014 Wisemann 900
2013 Miraphone 188
2013 Miraphone 188
-
- Posts: 343
- Joined: Fri Aug 14, 2020 7:03 am
- Has thanked: 116 times
- Been thanked: 93 times
Re: Sheet metal vs Tube Metal
I'd add a little from my day-job background (engineer). Tube can be made from rolled and welded flat stock, or it can be drawn off of billet/rod. Drawn tube may be limited to the smaller diameters, but it wouldn't have a seam, even a welded seam.
Part of the advantage of hand worked metal is that you can control how it is deformed, and also the internal stress is applied more evenly. After metal is worked for bell forming, it is generally heat treated in some combination of ways. It might be annealed to soften it and get rid of the internal stress from forming and welding, and then it might be heated and quenched to reintroduce more uniform internal stress. A fully soft annealed bell would sound dead, but something with some internal stress rings a little and is a bit harder, gives more treble overtones.
I have horns that are hand formed and some that are hydro formed. Yes, there's a difference in sound/feel. The audience may not hear it, but you can probably feel it.
I don't know if there are welded tuba bells, but I know some trombone bells are welded like the Yamahas. Welding is a higher temp process and joins the material by melting in the same material (brass or copper) instead of a lower temp material like tin/silver solder. You can argue that two pieces welded together constitute a single piece. Solder can be melted out to get your original pieces back, but welds have to be cut to take them apart.
Part of the advantage of hand worked metal is that you can control how it is deformed, and also the internal stress is applied more evenly. After metal is worked for bell forming, it is generally heat treated in some combination of ways. It might be annealed to soften it and get rid of the internal stress from forming and welding, and then it might be heated and quenched to reintroduce more uniform internal stress. A fully soft annealed bell would sound dead, but something with some internal stress rings a little and is a bit harder, gives more treble overtones.
I have horns that are hand formed and some that are hydro formed. Yes, there's a difference in sound/feel. The audience may not hear it, but you can probably feel it.
I don't know if there are welded tuba bells, but I know some trombone bells are welded like the Yamahas. Welding is a higher temp process and joins the material by melting in the same material (brass or copper) instead of a lower temp material like tin/silver solder. You can argue that two pieces welded together constitute a single piece. Solder can be melted out to get your original pieces back, but welds have to be cut to take them apart.
-
- Posts: 1343
- Joined: Mon Oct 26, 2020 2:31 pm
- Location: Portugal
- Has thanked: 6 times
- Been thanked: 169 times
Re: Sheet metal vs Tube Metal
I have a sousaphone bell that rings a little. I'm not sure I see how this resonance would generally be a good thing, though. I mean, wouldn't a resonant metal bell have a few specific frequencies, and tend to just speak when the pitch has an overtone that roughly matches that frequency?bone-a-phone wrote: ↑Mon Sep 13, 2021 8:28 am A fully soft annealed bell would sound dead, but something with some internal stress rings a little and is a bit harder, gives more treble overtones.
-
- Posts: 343
- Joined: Fri Aug 14, 2020 7:03 am
- Has thanked: 116 times
- Been thanked: 93 times
Re: Sheet metal vs Tube Metal
Yeah, every system has a natural resonant frequency. Ringing itself is not necessarily a benefit, a lot of people recoil in horror. But dead soft bell material would be bad in several ways. Mechanically it helps to have a horn that doesn't bend under its own weight, and also there is a tiny bit of feedback from the metal vibration back into the sound, and personally I like to feel a horn vibrating in my hands when playing it.donn wrote: ↑Mon Sep 13, 2021 8:35 amI have a sousaphone bell that rings a little. I'm not sure I see how this resonance would generally be a good thing, though. I mean, wouldn't a resonant metal bell have a few specific frequencies, and tend to just speak when the pitch has an overtone that roughly matches that frequency?bone-a-phone wrote: ↑Mon Sep 13, 2021 8:28 am A fully soft annealed bell would sound dead, but something with some internal stress rings a little and is a bit harder, gives more treble overtones.
My 88h resonates at F# and my 79h resonates at Ab. Violins have the dreaded wolf tone. I understand manufacturers try to push the resonant frequency between notes, or to an out of the way spot. Like the difference between a trash can lid and Capt. America's shield.
- bloke
- Mid South Music
- Posts: 19334
- Joined: Thu Aug 13, 2020 8:55 am
- Location: western Tennessee - near Memphis
- Has thanked: 3854 times
- Been thanked: 4103 times
Re: Sheet metal vs Tube Metal
Tuba bows - that made of sheet metal - are pretty cool, but the interior shape is obviously the thing. I suspect that some of the nicer instruments feature bows made of expanded tubes that have been sanded down with a belt sander on their smaller/thicker ends.
- jtm
- Posts: 1109
- Joined: Sat Aug 15, 2020 2:51 pm
- Location: Austin, Texas
- Has thanked: 698 times
- Been thanked: 209 times
Re: Sheet metal vs Tube Metal
How obvious are the seams in a bell with a tapered insert? Does lacquer normally hide them?
John Morris
This practicing trick actually seems to be working!
playing some old German rotary tubas for free
This practicing trick actually seems to be working!
playing some old German rotary tubas for free
- Rick Denney
- Resident Genius
- Posts: 1032
- Joined: Thu Aug 13, 2020 8:24 am
- Has thanked: 57 times
- Been thanked: 335 times
Re: Sheet metal vs Tube Metal
It depends on the alloy used in the brazing material. They usually cut a zipper seam to overlap the brass, braze it, and then grind it down smooth. You'll see the zipper pattern in the brazing material if it has more (or less) copper in it, or if it was ever allowed to patina. Usually masked pretty well by color buffing and lacquering, but the older instruments that used a gusset don't have that and the gusset is easy to see.
Rick "silver plating covers it up" Denney
Rick "silver plating covers it up" Denney
- These users thanked the author Rick Denney for the post:
- bloke (Tue Sep 14, 2021 10:02 am)
- bloke
- Mid South Music
- Posts: 19334
- Joined: Thu Aug 13, 2020 8:55 am
- Location: western Tennessee - near Memphis
- Has thanked: 3854 times
- Been thanked: 4103 times
Re: Sheet metal vs Tube Metal
It does, and it's curious how - sometimes, after considerable oxidation has formed - they are highlighted in the oxidation.
For quite a few months now (due to others' things taking precedence over my own) I have been pulled off the restoration of a will-be-for-sale "13-feet-long bugle period instrument, which points in an odd direction" (with 160-year-old rotors in astonishingly fine condition) which is all nickel silver and (as it is grey) the epic seams are all wonderfully visible.
-
- Posts: 343
- Joined: Fri Aug 14, 2020 7:03 am
- Has thanked: 116 times
- Been thanked: 93 times
Re: Sheet metal vs Tube Metal
Here's an image of an old tuba(probably cerveney) I owned at one point with a V insert. This was older than 1960. All my stories about the origin of this horn were second hand.
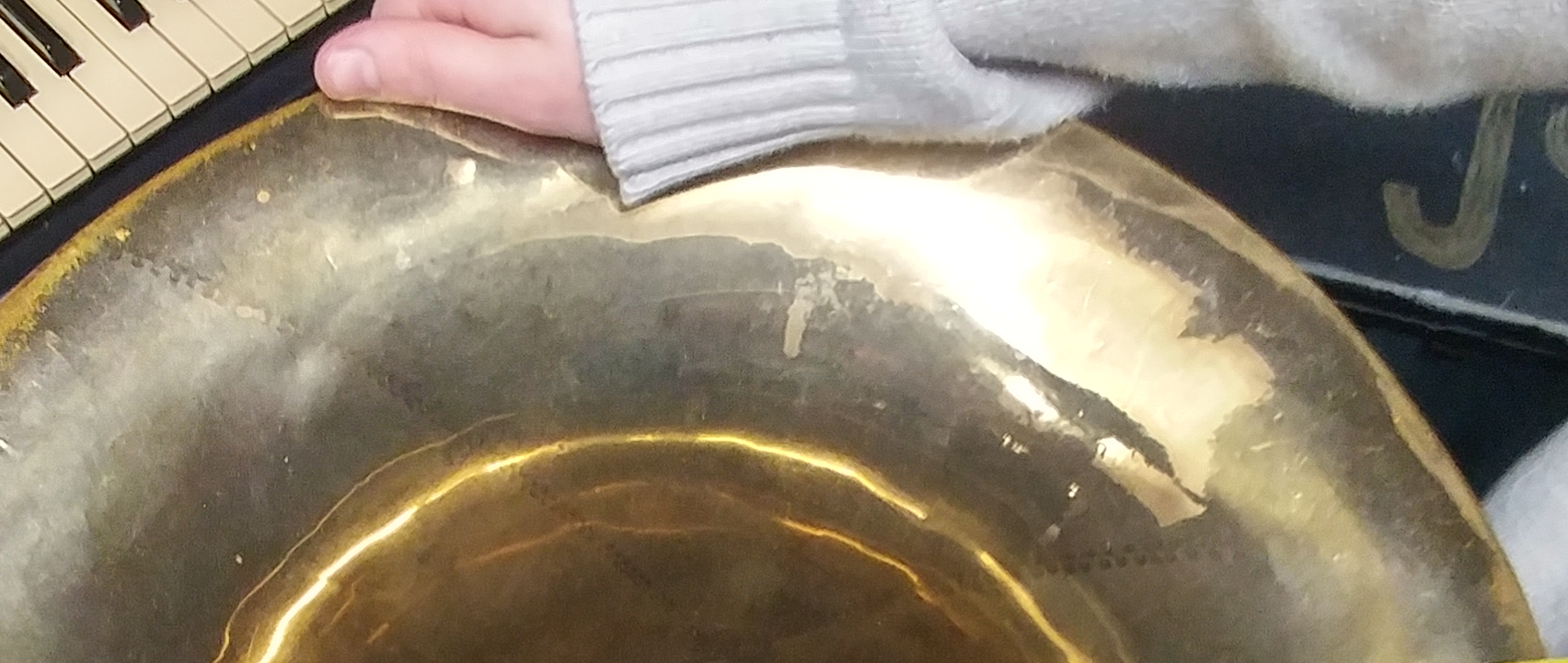
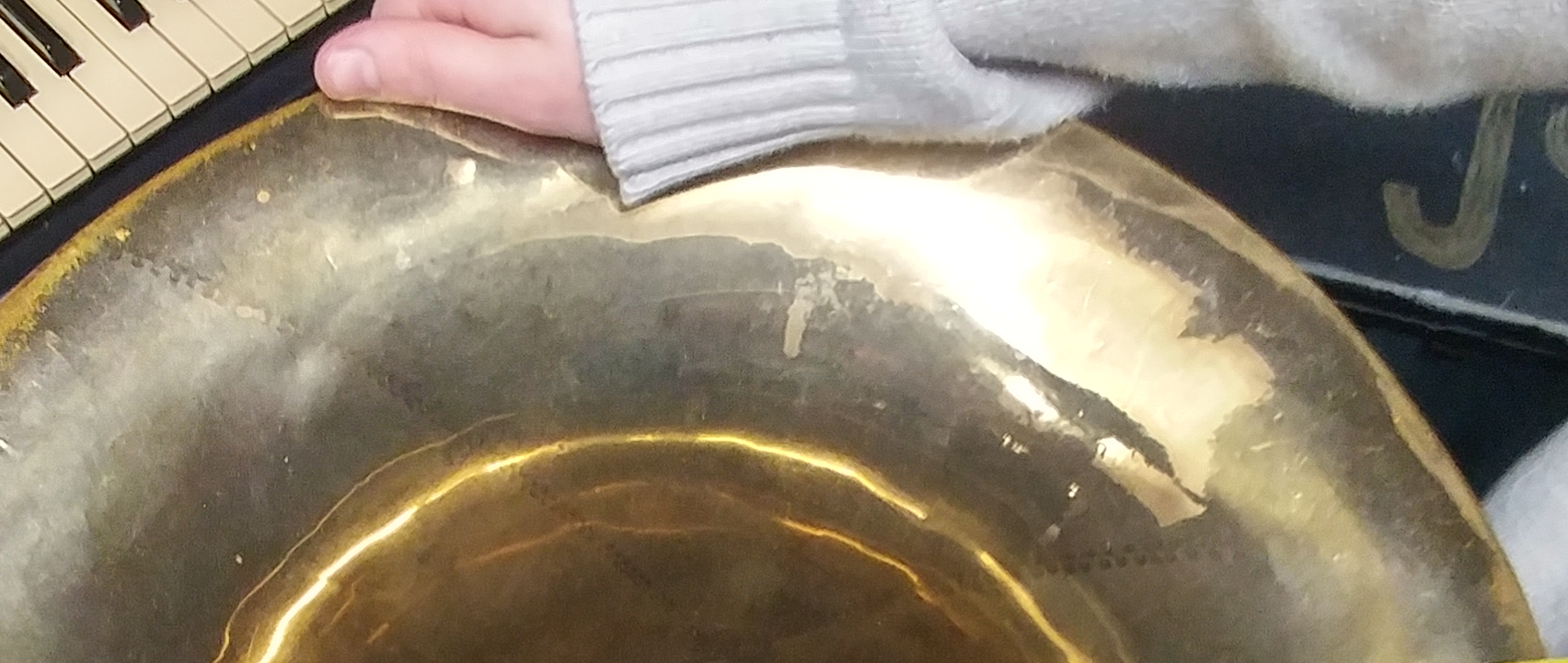
- the elephant
- Posts: 3401
- Joined: Thu Aug 13, 2020 8:39 am
- Location: 404 - Not Found
- Has thanked: 1902 times
- Been thanked: 1345 times
Re: Sheet metal vs Tube Metal
Here is an example of the seam of a hammered branch. It is running along the inside face of the back of the top bow of this 1971 Mirafone 186 CC.

Here is the bell of that tuba when I had the garland off and was brazing cracks and holes closed. You can see one seam of the gusset as a lighter line in the bell.

Same…

Here is what it looks like on the bottom bow when the guard will cover it up. The technician was probably thinking that if you can't see it, why bother to completely finish cleaning up that seam?


Here is the bell of that tuba when I had the garland off and was brazing cracks and holes closed. You can see one seam of the gusset as a lighter line in the bell.

Same…

Here is what it looks like on the bottom bow when the guard will cover it up. The technician was probably thinking that if you can't see it, why bother to completely finish cleaning up that seam?

- These users thanked the author the elephant for the post:
- York-aholic (Wed Sep 15, 2021 5:32 am)

- jtm
- Posts: 1109
- Joined: Sat Aug 15, 2020 2:51 pm
- Location: Austin, Texas
- Has thanked: 698 times
- Been thanked: 209 times
Re: Sheet metal vs Tube Metal
Thanks for the pictures and explanations. My tuba shows none of those marks, to my eye, so maybe I'm safe from it being collectible.
John Morris
This practicing trick actually seems to be working!
playing some old German rotary tubas for free
This practicing trick actually seems to be working!
playing some old German rotary tubas for free
- bloke
- Mid South Music
- Posts: 19334
- Joined: Thu Aug 13, 2020 8:55 am
- Location: western Tennessee - near Memphis
- Has thanked: 3854 times
- Been thanked: 4103 times
Re: Sheet metal vs Tube Metal
One other thing that may draw ire (and I touched on this before) but tubas are not xylophones, and neither are they cymbals nor jaw harps.
Annealed sheet brass is very malleable, and is a traditional way (still considered viable today, obviously) to enclose a column of air. The sound of a tuba - unless whacked - is made by vibrating the column of air from the small end of the tuba.
Yes… Even a coat of paint in a chapel can affect “the sound“, but the type of paint in the chapel is not going to affect “the sound and “as much as “replacing the organ with a new one“… and the sound alteration offered by the paint may possibly not be perceptible to humans - and maybe not even to humans who believe that they can perceive the difference.
Annealed sheet brass is very malleable, and is a traditional way (still considered viable today, obviously) to enclose a column of air. The sound of a tuba - unless whacked - is made by vibrating the column of air from the small end of the tuba.
Yes… Even a coat of paint in a chapel can affect “the sound“, but the type of paint in the chapel is not going to affect “the sound and “as much as “replacing the organ with a new one“… and the sound alteration offered by the paint may possibly not be perceptible to humans - and maybe not even to humans who believe that they can perceive the difference.
-
- Posts: 1343
- Joined: Mon Oct 26, 2020 2:31 pm
- Location: Portugal
- Has thanked: 6 times
- Been thanked: 169 times
Re: Sheet metal vs Tube Metal
Even a plastic tuba can sound more or less like any other tuba, which would be surprising if you thought the metallurgical character of brass would make any significant difference. Plastic is after all very different from brass. That is not to say that materials make no difference, just that it's very hard to predict what that difference is going to be.
- the elephant
- Posts: 3401
- Joined: Thu Aug 13, 2020 8:39 am
- Location: 404 - Not Found
- Has thanked: 1902 times
- Been thanked: 1345 times
Re: Sheet metal vs Tube Metal
I agree. I have no problems making a fiberglass Conn sousaphone sound as good as an all-brass one (to a listener in an audience) even though I hate how they *feel* when I play them. I have tooted on one of those fiberglass rotary tubas (can't remember who made it) and thought was a very nice sound, if somewhat dead in the hands; the listener could not detect much of a difference beyond it being obvious that I did not *like* the horn as much as the metal one I compared it to. Once I adjusted my attitude he could not tell a difference at all.
I have played several plastic instruments, and own a Tiger Trumpet and a PBone. I like them both (with metal mouthpieces). I am not much of a player of the trumpet or trombone, so I cannot really appreciate how bad these horns are; to me, they sound pretty characteristic of their types, despite my shortcomings as a player of either instrument.
I see no benefit or detriment to one-piece bell flares with a stem grafted onto the end versus a one-piece bell with a gusset grafted into the gap in the flare, so long as both are very well made. If I played on an old, beat tuba with visible seams and a bell that has been crushed and repaired several times, playing on a brand new "one-piece" bell (flare) would seem like an improvement. Likewise, spending all my time on some Yamaha student trumpet with a "one-piece" bell (flare) and then switching over to a traditional, hand-hammered bell with a gusset would seem like an improvement, too.
Six of one, half a dozen of the other. A really nice bell can be made using either method. I also do not put much stock in metallurgy beyond shading the sound's upper overtones, which only really advanced players or listeners will appreciate, in my experience.
When I ask colleagues to listen to a horn I am using in order to give me an opinion on the tonal characteristics, only three tubas have ever really grabbed any of them: Marty's old Cerveny Harmonia F, my current Miraphone 186, and a Meinl-Weston 32 with a 1941 York bell. I attribute these responses to the bell shape and physical condition more than to the alloys used in their construction. I have used lots of different horns at work, and all of them ended up sounding like me to others, regardless of them being rose, gold, or plain yellow brass, or even plastic. It is the shape of the container more than what the container is made of, I think. Beyond that basic level, it is just us doing a lot of hand-wringing and fussing.
I like building methods that take handwork. I am a traditionalist. I like labor-intensive stuff. I like old-school engraving. I like visible seams. I like seeing lots of old farts full-time employed doing these things and do not care so much for automation, laborsaving devices, robots, etc.
Prosit!
I have played several plastic instruments, and own a Tiger Trumpet and a PBone. I like them both (with metal mouthpieces). I am not much of a player of the trumpet or trombone, so I cannot really appreciate how bad these horns are; to me, they sound pretty characteristic of their types, despite my shortcomings as a player of either instrument.
I see no benefit or detriment to one-piece bell flares with a stem grafted onto the end versus a one-piece bell with a gusset grafted into the gap in the flare, so long as both are very well made. If I played on an old, beat tuba with visible seams and a bell that has been crushed and repaired several times, playing on a brand new "one-piece" bell (flare) would seem like an improvement. Likewise, spending all my time on some Yamaha student trumpet with a "one-piece" bell (flare) and then switching over to a traditional, hand-hammered bell with a gusset would seem like an improvement, too.
Six of one, half a dozen of the other. A really nice bell can be made using either method. I also do not put much stock in metallurgy beyond shading the sound's upper overtones, which only really advanced players or listeners will appreciate, in my experience.
When I ask colleagues to listen to a horn I am using in order to give me an opinion on the tonal characteristics, only three tubas have ever really grabbed any of them: Marty's old Cerveny Harmonia F, my current Miraphone 186, and a Meinl-Weston 32 with a 1941 York bell. I attribute these responses to the bell shape and physical condition more than to the alloys used in their construction. I have used lots of different horns at work, and all of them ended up sounding like me to others, regardless of them being rose, gold, or plain yellow brass, or even plastic. It is the shape of the container more than what the container is made of, I think. Beyond that basic level, it is just us doing a lot of hand-wringing and fussing.
I like building methods that take handwork. I am a traditionalist. I like labor-intensive stuff. I like old-school engraving. I like visible seams. I like seeing lots of old farts full-time employed doing these things and do not care so much for automation, laborsaving devices, robots, etc.
Prosit!

- bloke
- Mid South Music
- Posts: 19334
- Joined: Thu Aug 13, 2020 8:55 am
- Location: western Tennessee - near Memphis
- Has thanked: 3854 times
- Been thanked: 4103 times
Re: Sheet metal vs Tube Metal
As much as I appreciate my friends/colleagues, I suspect that - when I might ask them about a new instrument - either they
- really don't hear much difference ("bloke playing this" vs. "bloke playing that")...or...
- (being 200+ lbs.) they might tend to patronize me...or...
- they offer opinions on sonic characteristics with which I would disagree, were I one of the 2nd-party listeners.
I have a section-mate who's always asking if he sounded ok on this/that/the-other.
He's an Indiana graduate/Kleinhammer student, and plays just fine.
I remind him that I'm a relatively-unschooled mercenary dollar-chasin' tuba hillbilly, and then tell him that everything he played sucked, because none of it drowned out the orchestra.
I might post some cool "seam pics" of my nickel silver OTS uncivil-era E-flat, because
- The seams are very pronounced (so much so, that they're sorta fun to look at).
- I'd like to generate some pre-interest for when I FINALLY get the thing slicked out.
- really don't hear much difference ("bloke playing this" vs. "bloke playing that")...or...
- (being 200+ lbs.) they might tend to patronize me...or...
- they offer opinions on sonic characteristics with which I would disagree, were I one of the 2nd-party listeners.

I have a section-mate who's always asking if he sounded ok on this/that/the-other.
He's an Indiana graduate/Kleinhammer student, and plays just fine.
I remind him that I'm a relatively-unschooled mercenary dollar-chasin' tuba hillbilly, and then tell him that everything he played sucked, because none of it drowned out the orchestra.
I might post some cool "seam pics" of my nickel silver OTS uncivil-era E-flat, because
- The seams are very pronounced (so much so, that they're sorta fun to look at).
- I'd like to generate some pre-interest for when I FINALLY get the thing slicked out.