The Great Kurath Re-Tubing
- the elephant
- Posts: 3414
- Joined: Thu Aug 13, 2020 8:39 am
- Location: 404 - Not Found
- Has thanked: 1907 times
- Been thanked: 1353 times
Re: The Great Kurath Re-Tubing
Yep. Thanks!
I have decided to buy some quarter-inch brass plate (or 5 mm, whichever is easier to find in a small square that is cheap) and cut it to fit like the Willson, but locating the ring where I want it. The fact that I do not need to also incorporate the lever (as on the Willson part) makes this much easier/cheaper. I like my reuse of the ridiculous Kurath lever bracket, but I can make a better one myself out of some nickel silver bar stock. (I am rather "un-bad" at making levers and brackets.) My Rube Goldberg lever was temporary at best, because its location (dictated by the location of the one it replaced) was always a PITA for me, causing pain in the tendon of my thumb. I knew it was going to be moved.
What made this an issue *now* is that I had the idea to rotate the pic of the Holton setup to get the pistons as close to the angle of the Kurath one and compare what I have on both. (These piston sets, as you know, both were made by Herr Nirschl, but the vertical ones have an offset 1st and the 45º ones have an offset 4th. I can only approximate stuff because of this.
Drawing the approximate triangle between the Holton's 1st, 4th and the location of where my thumb rests when the lever is not activated seemed like a good place to start. Oddly, I noted my own "ergonomic consistency" once the two could be laid side-by-side: though the thumb rings are at very different angles when the horns are upright when the pistons are tilted (so they are pretty close to the same angles), both thumb rings are set as the same angle in relation to that triangle.
Cool.
Anyway, I now have a very good idea of where to start with my initial cutting of the thumb ring plate. I have an NS crook of the correct ID (like 18.5 mm) that will fit neatly over that 1st knuckle, and it seems to share the same inner radius, so I think I may have the part needed to silver solder to the brass plate like the Willson bracket. I need to make it a little longer to the side, and it does not have to hang down so low since no lever will be fitted to it.
I have the fatty thumb ring (very Cerveny-esque) but it is cut down on the bottom to allow it to be brazed to its thick brass mounting plate. I might just Dremel that plate off in the shape of the fat tube so that it is round all the way around the annulus, just with a brass insert at the bottom. I am not sure if this will be thick enough, but whatever. Despite this, I am pretty sure it will be stronger than any force I could ever manage to apply to it. If I can solver solder the Voigt threaded piece with its captured lock collar I can also braze its brass receiver onto the plate, so that I use the Voigt hardware to connect the original ring to my new bracket/baseplate/chingadera.
If I become lazy in this process (and I'm sure I will as it drags on) I will just use the Voigt ring with the mounting socket brazed onto my bracket. (I really like those fat thumb rings, though, so who knows WTF I'll end up doing?)
Regardless of the thumb LEVER, though, what I have will not work and I don't want to alter it, so I will make a new one. It flexes just a bit because of how long and thin it is, so part of it will be from some heavier rod stock. The bracket that I hate so much is because it is SO HEAVY that it causes thermal expansion issues and affects the slide alignment. How I have it now works great, but it is not yet anchored to the 3rd slide, so it, being yellow brass, is a bit flexy. I am not sure whether it is worth it to try and deal with the heat issue again, as the end that would connect to the 3rd slide is the end that lengthens and twists when it is heated.
Honestly, making a nickel silver one would be better as that stuff is stiff, so you can use thinner stock and not have to apply so much freaking heat to get soft solder to flow beneath it. I still have to think about this some. I *really* hate the Kurath bracket, so this will probably happen. I just hate creating more work on top of other created work, lumped on top of stuff that *needs* to be done.
And now I need to log off and spend some time scuffing the pate with the fingertips…
I have decided to buy some quarter-inch brass plate (or 5 mm, whichever is easier to find in a small square that is cheap) and cut it to fit like the Willson, but locating the ring where I want it. The fact that I do not need to also incorporate the lever (as on the Willson part) makes this much easier/cheaper. I like my reuse of the ridiculous Kurath lever bracket, but I can make a better one myself out of some nickel silver bar stock. (I am rather "un-bad" at making levers and brackets.) My Rube Goldberg lever was temporary at best, because its location (dictated by the location of the one it replaced) was always a PITA for me, causing pain in the tendon of my thumb. I knew it was going to be moved.
What made this an issue *now* is that I had the idea to rotate the pic of the Holton setup to get the pistons as close to the angle of the Kurath one and compare what I have on both. (These piston sets, as you know, both were made by Herr Nirschl, but the vertical ones have an offset 1st and the 45º ones have an offset 4th. I can only approximate stuff because of this.
Drawing the approximate triangle between the Holton's 1st, 4th and the location of where my thumb rests when the lever is not activated seemed like a good place to start. Oddly, I noted my own "ergonomic consistency" once the two could be laid side-by-side: though the thumb rings are at very different angles when the horns are upright when the pistons are tilted (so they are pretty close to the same angles), both thumb rings are set as the same angle in relation to that triangle.
Cool.
Anyway, I now have a very good idea of where to start with my initial cutting of the thumb ring plate. I have an NS crook of the correct ID (like 18.5 mm) that will fit neatly over that 1st knuckle, and it seems to share the same inner radius, so I think I may have the part needed to silver solder to the brass plate like the Willson bracket. I need to make it a little longer to the side, and it does not have to hang down so low since no lever will be fitted to it.
I have the fatty thumb ring (very Cerveny-esque) but it is cut down on the bottom to allow it to be brazed to its thick brass mounting plate. I might just Dremel that plate off in the shape of the fat tube so that it is round all the way around the annulus, just with a brass insert at the bottom. I am not sure if this will be thick enough, but whatever. Despite this, I am pretty sure it will be stronger than any force I could ever manage to apply to it. If I can solver solder the Voigt threaded piece with its captured lock collar I can also braze its brass receiver onto the plate, so that I use the Voigt hardware to connect the original ring to my new bracket/baseplate/chingadera.
If I become lazy in this process (and I'm sure I will as it drags on) I will just use the Voigt ring with the mounting socket brazed onto my bracket. (I really like those fat thumb rings, though, so who knows WTF I'll end up doing?)
Regardless of the thumb LEVER, though, what I have will not work and I don't want to alter it, so I will make a new one. It flexes just a bit because of how long and thin it is, so part of it will be from some heavier rod stock. The bracket that I hate so much is because it is SO HEAVY that it causes thermal expansion issues and affects the slide alignment. How I have it now works great, but it is not yet anchored to the 3rd slide, so it, being yellow brass, is a bit flexy. I am not sure whether it is worth it to try and deal with the heat issue again, as the end that would connect to the 3rd slide is the end that lengthens and twists when it is heated.
Honestly, making a nickel silver one would be better as that stuff is stiff, so you can use thinner stock and not have to apply so much freaking heat to get soft solder to flow beneath it. I still have to think about this some. I *really* hate the Kurath bracket, so this will probably happen. I just hate creating more work on top of other created work, lumped on top of stuff that *needs* to be done.
And now I need to log off and spend some time scuffing the pate with the fingertips…
Last edited by the elephant on Fri Jan 14, 2022 7:28 pm, edited 1 time in total.
- These users thanked the author the elephant for the post:
- prairieboy1 (Tue Jan 04, 2022 7:10 pm)

- bloke
- Mid South Music
- Posts: 19373
- Joined: Thu Aug 13, 2020 8:55 am
- Location: western Tennessee - near Memphis
- Has thanked: 3859 times
- Been thanked: 4119 times
Re: The Great Kurath Re-Tubing
You should congratulate me:
In spite of that being long, I was able to follow all of what you typed.
- Thumb rings - that are located too high on the instrument (too close to the rim of the bell) - SUCK…and probably suck for just about everyone. Anytime I see this, I credit it to designer laziness.
- Sometimes, thumb rings are located in just about the right place (and/or are even incredibly adjustable), but are made so as the >angle< of them defines them as ”impossible”. This is the case with the model 5450 tuba. After re-brazing the ring to the (otherwise) incredibly adjustable mount arm (at about a 40° [??] angle, rather that “straight-on”), suddenly it fit my hand perfectly.

something else:
This doesn't require "genius", but one also needs to be able to figure out (not only that something is "wrong", but also) what is "right".
In spite of that being long, I was able to follow all of what you typed.


- Thumb rings - that are located too high on the instrument (too close to the rim of the bell) - SUCK…and probably suck for just about everyone. Anytime I see this, I credit it to designer laziness.
- Sometimes, thumb rings are located in just about the right place (and/or are even incredibly adjustable), but are made so as the >angle< of them defines them as ”impossible”. This is the case with the model 5450 tuba. After re-brazing the ring to the (otherwise) incredibly adjustable mount arm (at about a 40° [??] angle, rather that “straight-on”), suddenly it fit my hand perfectly.

something else:
This doesn't require "genius", but one also needs to be able to figure out (not only that something is "wrong", but also) what is "right".
- These users thanked the author bloke for the post:
- the elephant (Tue Jan 04, 2022 11:41 am)
- the elephant
- Posts: 3414
- Joined: Thu Aug 13, 2020 8:39 am
- Location: 404 - Not Found
- Has thanked: 1907 times
- Been thanked: 1353 times
Re: The Great Kurath Re-Tubing
Okay, I had written today off for getting anything done on this project. I was happily wasting time on the couch ingesting heated bean juice and then I typed all that above.
So of course, being bored out of my skull usually when I "relax" (heh, yeah, right…) I decided to get that big ring ready for use by removing the base plate. But as I said above, I did not want to saw off the ring where it was sawn before to be mounted flat to this base plate unless forced to do so. So I Dremeled away most of the material and then listened to Ella and Louis while I filed and sanded and eyeballed… and eventually buffed.
It came out decent enough, but the remainder of the base plate is yellow brass, so this has very definite good and bad sides. I also knicked up the ring with the center quick release collar of the Dremel tool, which pissed me off to no end. Judicious filing and sanding hid the worst of that, and the ring is pitted (as is much of the horn) due to crappy lacquer and decades of acidic sweat from at least one of the POs. So with the unavoidable flaws that already existed, my mini-FUBARs will be fine and I'm not going to go all OCD on this. <whew!>
"He was such a fine big boy. I thought you knew." (The quote had nothing to do with this. It is a quote used by a buddy in the Army for a variety of situations and is what popped into my head when I first saw this photo. Can you name the ref?)

You can see how the plate was just hammered around two slugs so that the skinny end sort of wrapped around/behind the slide tube. The rest could have been flat. The person who made this wasted a lot of time on it, considering it is not adjustable at all and was located in a terrible place. I could not get my thumb through it *and* on the paddle for the lever without contorting my hand and F-ing up my hand position on the buttons.


I took this to look at it from the side without visual distractions. I saw some still-too-thick stuff and took it back outside.

DONE!

Here is the original join line between the brass plate and the hollow NS ring's tubing…

A comparison with the above photos…

This will work nicely, so I need to go ahead with making a base plate that will locate this here and not look like Home Depot-fueled, bad DIY plumbing work. If I get that far I will make a new lever and bracket.

So of course, being bored out of my skull usually when I "relax" (heh, yeah, right…) I decided to get that big ring ready for use by removing the base plate. But as I said above, I did not want to saw off the ring where it was sawn before to be mounted flat to this base plate unless forced to do so. So I Dremeled away most of the material and then listened to Ella and Louis while I filed and sanded and eyeballed… and eventually buffed.
It came out decent enough, but the remainder of the base plate is yellow brass, so this has very definite good and bad sides. I also knicked up the ring with the center quick release collar of the Dremel tool, which pissed me off to no end. Judicious filing and sanding hid the worst of that, and the ring is pitted (as is much of the horn) due to crappy lacquer and decades of acidic sweat from at least one of the POs. So with the unavoidable flaws that already existed, my mini-FUBARs will be fine and I'm not going to go all OCD on this. <whew!>
"He was such a fine big boy. I thought you knew." (The quote had nothing to do with this. It is a quote used by a buddy in the Army for a variety of situations and is what popped into my head when I first saw this photo. Can you name the ref?)

You can see how the plate was just hammered around two slugs so that the skinny end sort of wrapped around/behind the slide tube. The rest could have been flat. The person who made this wasted a lot of time on it, considering it is not adjustable at all and was located in a terrible place. I could not get my thumb through it *and* on the paddle for the lever without contorting my hand and F-ing up my hand position on the buttons.


I took this to look at it from the side without visual distractions. I saw some still-too-thick stuff and took it back outside.

DONE!

Here is the original join line between the brass plate and the hollow NS ring's tubing…

A comparison with the above photos…

This will work nicely, so I need to go ahead with making a base plate that will locate this here and not look like Home Depot-fueled, bad DIY plumbing work. If I get that far I will make a new lever and bracket.

- These users thanked the author the elephant for the post (total 4):
- hrender (Tue Jan 04, 2022 5:44 pm) • prairieboy1 (Tue Jan 04, 2022 7:10 pm) • bloke (Tue Jan 04, 2022 9:02 pm) • York-aholic (Wed Jan 05, 2022 8:34 am)

- the elephant
- Posts: 3414
- Joined: Thu Aug 13, 2020 8:39 am
- Location: 404 - Not Found
- Has thanked: 1907 times
- Been thanked: 1353 times
HELP! MIRAPHONE 180 OWNERS PLEASE READ!
I am in need of a few very careful measurements from the main tuning slide of a Miraphone 180 F tuba. (I don't need *any* other measurements from anything else; thanks, though.)
A — inside radius/span of the crook only
B — inside distance/span between the two outer MTS tubes
C — bore of inner MTS leg (if the tube end is not perfectly circular or is rounded in, then the bore size of the outer tubes)
For C, I am looking to confirm a measurement of .737"/18.77 mm bore of the inner tube (or .769"/19.54 mm bore of the outer tube), or a definite confirmation that this is NOT the case for either tube.
I need this info sort of soon, so I will cross-post this in hopes of an answer before January 10th. THANKS!

A — inside radius/span of the crook only
B — inside distance/span between the two outer MTS tubes
C — bore of inner MTS leg (if the tube end is not perfectly circular or is rounded in, then the bore size of the outer tubes)
For C, I am looking to confirm a measurement of .737"/18.77 mm bore of the inner tube (or .769"/19.54 mm bore of the outer tube), or a definite confirmation that this is NOT the case for either tube.
I need this info sort of soon, so I will cross-post this in hopes of an answer before January 10th. THANKS!


- the elephant
- Posts: 3414
- Joined: Thu Aug 13, 2020 8:39 am
- Location: 404 - Not Found
- Has thanked: 1907 times
- Been thanked: 1353 times
Re: The Great Kurath Re-Tubing
Okay, I think I now have everything I need to to the complete 5th valve "transmission" on the way.
In other news, UPS (never a great choice when shipping OUT of Mississippi) has a spotty record with me for lost or damaged packages that goes back over torturous 20 years. This time they lost a package that was ON THE DAMNED TRUCK about to be delivered to me. The driver *thinks* it may have fallen through the busted open tape seal of a much larger box that it was on top of in the truck's bay. (Seriously, it was in a small box and the trucks have a special rack for small boxes so as to not have this sort of crap happen. Come on, man — do your job better!)
It has been missing since December 22nd, the morning it arrived at the Vicksburg hub, was scanned in, and then scanned as on the truck out for delivery.
It was a single knurled thumb screw for this tuba. UPS's system for filing a claim will not allow me to file a claim. Because of course it won't. There is no published number to call the small, barn-sized UPS hub in Vicksburg. It is so small that you can drive down there and get them to search for it while you wait, but since it was likely delivered to another party inside their damaged package it is probably gone forever.
After waiting a long time for them to get this sorted on their own (since it shows up as an overdue, lost package on their computer) and getting nothing from them, and being unable (not allowed?) to file a claim, I finally called McMaster-Carr and they made it good for me without question and shipped out another one as I spoke to the agent on the phone.
I received an email with the new order, then the tracking number, then notice that it had shipped, all while I was on the phone. I suppose that they had what I needed right next to the shipping desk of that office, and they got it packed and labeled just as the UPS guy drove up on his morning pickup run. How unusual, but excellent. (I once worked as an "Assembly Monkey" at a small, very high-end company where I soldered together the old-school "thinnet" ethernet cards for the Navy and Marine Corps, made super-high-quality telephone exchange patch cables for US Sprint… stuff like that… and every day it was an All Hands General Quarters emergency (meaning "Assembly Monkeys" had to temporarily become "Shipping Monkeys" in order to get that day's shipping packaged and labeled in time for the UPS pickup. We had very strict government-set production deadlines to meet every day, so I know how it feels when you get a last-minute order that you think you can build, and then squeak through the shipping process just in time for the UPS guy to drive up. It's kind of a rush, actually. So I hope that person got a kick out of making sure that my order was fulfilled and shipped in under fifteen minutes.
McMaster-Carr
UPS
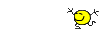
In other news, UPS (never a great choice when shipping OUT of Mississippi) has a spotty record with me for lost or damaged packages that goes back over torturous 20 years. This time they lost a package that was ON THE DAMNED TRUCK about to be delivered to me. The driver *thinks* it may have fallen through the busted open tape seal of a much larger box that it was on top of in the truck's bay. (Seriously, it was in a small box and the trucks have a special rack for small boxes so as to not have this sort of crap happen. Come on, man — do your job better!)
It has been missing since December 22nd, the morning it arrived at the Vicksburg hub, was scanned in, and then scanned as on the truck out for delivery.
It was a single knurled thumb screw for this tuba. UPS's system for filing a claim will not allow me to file a claim. Because of course it won't. There is no published number to call the small, barn-sized UPS hub in Vicksburg. It is so small that you can drive down there and get them to search for it while you wait, but since it was likely delivered to another party inside their damaged package it is probably gone forever.
After waiting a long time for them to get this sorted on their own (since it shows up as an overdue, lost package on their computer) and getting nothing from them, and being unable (not allowed?) to file a claim, I finally called McMaster-Carr and they made it good for me without question and shipped out another one as I spoke to the agent on the phone.
I received an email with the new order, then the tracking number, then notice that it had shipped, all while I was on the phone. I suppose that they had what I needed right next to the shipping desk of that office, and they got it packed and labeled just as the UPS guy drove up on his morning pickup run. How unusual, but excellent. (I once worked as an "Assembly Monkey" at a small, very high-end company where I soldered together the old-school "thinnet" ethernet cards for the Navy and Marine Corps, made super-high-quality telephone exchange patch cables for US Sprint… stuff like that… and every day it was an All Hands General Quarters emergency (meaning "Assembly Monkeys" had to temporarily become "Shipping Monkeys" in order to get that day's shipping packaged and labeled in time for the UPS pickup. We had very strict government-set production deadlines to meet every day, so I know how it feels when you get a last-minute order that you think you can build, and then squeak through the shipping process just in time for the UPS guy to drive up. It's kind of a rush, actually. So I hope that person got a kick out of making sure that my order was fulfilled and shipped in under fifteen minutes.


- These users thanked the author the elephant for the post:
- prairieboy1 (Mon Jan 17, 2022 10:29 am)

Re: The Great Kurath Re-Tubing
Speaking as an IT guy who gets a lot of calls and emails with "Hey, could you <...> right away?" requests, it's a satisfying part of the job to be able to say, "Sure, just give me 5 minutes," and then be able to complete the request. Props to McMaster-Carr for having people like that on staff.
- These users thanked the author hrender for the post:
- the elephant (Thu Jan 06, 2022 2:11 pm)
- Three Valves
- Posts: 4613
- Joined: Thu Aug 13, 2020 4:07 pm
- Location: The Land of Pleasant Living
- Has thanked: 818 times
- Been thanked: 505 times
Re: The Great Kurath Re-Tubing
I can smell brass and compound!!
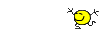
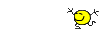
- These users thanked the author Three Valves for the post:
- the elephant (Thu Jan 06, 2022 7:47 pm)
Thought Criminal
Mack Brass Artiste
TU422L with TU25
1964 Conn 36k with CB Arnold Jacobs
Accent (By B&S) 952R with Bach12
The Fourth Estate is the Fifth Column
Mack Brass Artiste
TU422L with TU25
1964 Conn 36k with CB Arnold Jacobs
Accent (By B&S) 952R with Bach12
The Fourth Estate is the Fifth Column
- the elephant
- Posts: 3414
- Joined: Thu Aug 13, 2020 8:39 am
- Location: 404 - Not Found
- Has thanked: 1907 times
- Been thanked: 1353 times
Re: The Great Kurath Re-Tubing
Note to self (after today's UPS delivery):
A 1.5" x 0.25" x 12.0" bar of nickel silver could easily be used to bludgeon someone to death. Wow. Isn't this stuff lighter than yellow brass? I think I may sleep with this by my side instead of having a pistol in the nightstand drawer, home invaders be damned…

A 1.5" x 0.25" x 12.0" bar of nickel silver could easily be used to bludgeon someone to death. Wow. Isn't this stuff lighter than yellow brass? I think I may sleep with this by my side instead of having a pistol in the nightstand drawer, home invaders be damned…


- bloke
- Mid South Music
- Posts: 19373
- Joined: Thu Aug 13, 2020 8:55 am
- Location: western Tennessee - near Memphis
- Has thanked: 3859 times
- Been thanked: 4119 times
Re: The Great Kurath Re-Tubing
OK if you don’t cut the rest of it into long strips and solder them - *lengthwise, of course - to the outside of your bell, you will never get that world-class tone and resonance that you’ve been seeking.
___________
*Otherwise, it would totally disrupt the sound waves, and using brass ones - as we all know - would make it play out of tune.
___________
*Otherwise, it would totally disrupt the sound waves, and using brass ones - as we all know - would make it play out of tune.
- These users thanked the author bloke for the post:
- the elephant (Fri Jan 14, 2022 7:27 pm)
- the elephant
- Posts: 3414
- Joined: Thu Aug 13, 2020 8:39 am
- Location: 404 - Not Found
- Has thanked: 1907 times
- Been thanked: 1353 times
Re: The Great Kurath Re-Tubing
I just ordered and paid for a box of fun stuff for this project.
And then…
I did it again, as I had a hair-brained, redneck idea that my mama would slap me for if she knew what it was.
And I sent in another order ASAP in hopes to have it piggybacked on my order from a few days ago. However, I think this will not happen, as this order involve some of their excellent custom work and *ahem* shop labor charges. If I can get what I want I will be tickled, and it will make this F tuba a one-of-a-kind for both Willson and Kurath.
Lucky for me, I am decent at drawing pictures in Apple's Markup app within the Photos app. I sent a detailed description with the drawing, and an explanation of what I intend to do, so as to help the technician get my two weird requests.
This is going to be very fun! I will be adding a 6th valve to the horn to give Joe's F tuba "lifestyle" a try. The 5th valve on my horn is grossly inadequate as it leaks pretty badly. Rather than dink around with the swaging tool or tap-tap-tapping between the knuckles, I decided to burn up the last of my Christmas gig money on a new 5th valve with all the correctly-sized crooks, runners, and slide tubes. Then, tonight, I added this custom valve with knuckle IDs and orientations that I need, as well as the correctly-sized crooks, runners, and slide tubing.
I have now performed on this horn with the new bore profile and it works very nicely. I have to take it all down to fine-tune some tube lengths and work out an alignment issue from the factory that bugs the snot out of me. I will plug in the new 5th/6th section at that time.
Woo-hoo!
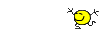
And then…
I did it again, as I had a hair-brained, redneck idea that my mama would slap me for if she knew what it was.
And I sent in another order ASAP in hopes to have it piggybacked on my order from a few days ago. However, I think this will not happen, as this order involve some of their excellent custom work and *ahem* shop labor charges. If I can get what I want I will be tickled, and it will make this F tuba a one-of-a-kind for both Willson and Kurath.
Lucky for me, I am decent at drawing pictures in Apple's Markup app within the Photos app. I sent a detailed description with the drawing, and an explanation of what I intend to do, so as to help the technician get my two weird requests.
This is going to be very fun! I will be adding a 6th valve to the horn to give Joe's F tuba "lifestyle" a try. The 5th valve on my horn is grossly inadequate as it leaks pretty badly. Rather than dink around with the swaging tool or tap-tap-tapping between the knuckles, I decided to burn up the last of my Christmas gig money on a new 5th valve with all the correctly-sized crooks, runners, and slide tubes. Then, tonight, I added this custom valve with knuckle IDs and orientations that I need, as well as the correctly-sized crooks, runners, and slide tubing.
I have now performed on this horn with the new bore profile and it works very nicely. I have to take it all down to fine-tune some tube lengths and work out an alignment issue from the factory that bugs the snot out of me. I will plug in the new 5th/6th section at that time.
Woo-hoo!
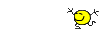
- These users thanked the author the elephant for the post:
- prairieboy1 (Mon Jan 17, 2022 10:30 am)

- the elephant
- Posts: 3414
- Joined: Thu Aug 13, 2020 8:39 am
- Location: 404 - Not Found
- Has thanked: 1907 times
- Been thanked: 1353 times
Re: The Great Kurath Re-Tubing
The 5th casing in this illustration is upside down compared with how the valve is installed on the 186. I need the normal IN port to be one tube size larger. I then need the cork plate oriented 90º from where it normally goes. The rotor will not change, but it will rotate in the opposite direction when this is assembled.
The slide will point downwards and will live between the pistons and the 3rd/4th slide side of the horn behind the 4th slide. There is ample room for this within the frame of the tuba.
The lever will be a bear, but I am good with levers, and I am a stubborn pig, so I will eventually sort it out.

The slide will point downwards and will live between the pistons and the 3rd/4th slide side of the horn behind the 4th slide. There is ample room for this within the frame of the tuba.
The lever will be a bear, but I am good with levers, and I am a stubborn pig, so I will eventually sort it out.

- These users thanked the author the elephant for the post (total 2):
- York-aholic (Fri Jan 14, 2022 7:24 pm) • prairieboy1 (Mon Jan 17, 2022 10:30 am)

- Tubajug
- Posts: 746
- Joined: Thu Aug 13, 2020 10:27 am
- Location: Nebraska
- Has thanked: 226 times
- Been thanked: 203 times
Re: The Great Kurath Re-Tubing
Will it be a double thumb trigger (side by side)?
Jordan
King 2341 with Holton Monster Eb Bell
King/Conn Eb Frankentuba
Pan AmeriConn BBb Helicon
Yamaha YBB-103
"No one else is placed exactly as we are in our opportune human orbits."
King 2341 with Holton Monster Eb Bell
King/Conn Eb Frankentuba
Pan AmeriConn BBb Helicon
Yamaha YBB-103
"No one else is placed exactly as we are in our opportune human orbits."
- the elephant
- Posts: 3414
- Joined: Thu Aug 13, 2020 8:39 am
- Location: 404 - Not Found
- Has thanked: 1907 times
- Been thanked: 1353 times
Re: The Great Kurath Re-Tubing
I think I will leave the 5th lever for my R thumb, but will extend it to work for LH, too, and have 6th set up next to that, for use with LH, 5 & 6 being like 1 & 2 with 4th down. And then we shall see what all that six-valved hullabaloo is about.
- These users thanked the author the elephant for the post:
- Tubajug (Sat Jan 15, 2022 7:26 am)

- the elephant
- Posts: 3414
- Joined: Thu Aug 13, 2020 8:39 am
- Location: 404 - Not Found
- Has thanked: 1907 times
- Been thanked: 1353 times
Re: The Great Kurath Re-Tubing
ASK AND YE SHALL RECEIVE!
Eva sent me an email. Christian had this assembled for me, I do not think the knuckles have yet been hard soldered in place, in case it was not correct, but baby, they NAILED IT for me. It definitely was worth my time and effort to create that silly graphic up above to the detail level I did, because it must have been perfectly clear, so he assembled it with no issues whatsoever. (This is *much* improved over my experience with them creating a custom leadpipe for my 186. Getting it right in only two tries is very good, but the fact that the first try went all the way to my front door only for it to be discovered that it was not at all what I had thought I described. The second one was perfect, but it cost them a bunch of labor time and a nickel silver leadpipe tube for nothing. Assembling it "dry" first and labeling it as he did saved a ton of time and money. Great job, Christian Niedermaier and Eva Staudinger!)
This will eventually make its way to Mississippi and will become this tuba's 6th valve. How freaking cool is that???

Eva sent me an email. Christian had this assembled for me, I do not think the knuckles have yet been hard soldered in place, in case it was not correct, but baby, they NAILED IT for me. It definitely was worth my time and effort to create that silly graphic up above to the detail level I did, because it must have been perfectly clear, so he assembled it with no issues whatsoever. (This is *much* improved over my experience with them creating a custom leadpipe for my 186. Getting it right in only two tries is very good, but the fact that the first try went all the way to my front door only for it to be discovered that it was not at all what I had thought I described. The second one was perfect, but it cost them a bunch of labor time and a nickel silver leadpipe tube for nothing. Assembling it "dry" first and labeling it as he did saved a ton of time and money. Great job, Christian Niedermaier and Eva Staudinger!)
This will eventually make its way to Mississippi and will become this tuba's 6th valve. How freaking cool is that???

- These users thanked the author the elephant for the post (total 3):
- York-aholic (Mon Jan 17, 2022 8:44 am) • bloke (Mon Jan 17, 2022 10:00 am) • prairieboy1 (Mon Jan 17, 2022 10:31 am)

- the elephant
- Posts: 3414
- Joined: Thu Aug 13, 2020 8:39 am
- Location: 404 - Not Found
- Has thanked: 1907 times
- Been thanked: 1353 times
Re: The Great Kurath Re-Tubing
I ordered this and the larger 5th valve in all nickel silver. Yeah, laugh at me if you will, but the option was only $20 more per valve. Usually, with two of the same part, the nickel silver one costs double what the brass one does. Since almost all of the cost of a completed rotary valve assembly is machine shop labor time and not materials, and the ONLY part of these that normally comes in yellow brass is the case tube, a bump of about twenty bucks makes sense.
Regardless, I was very pleased to discover that I could get my new 5th and 6th valves in nickel silver for like $40 extra, total. They will likely never wear out since the only failure point can be the softer brass rotors. These can easily be replaced so long as the walls and bearings of the casing are still in excellent condition, and they will be because they are the harder wearing of the two surfaces.
[The fact that they feed into my love for silver-colored things over gold-colored things is just gravy for me. And a very tasty gravy, that.]
So, back to the one-off valve: It is just a stock 186 5th valve in NS. They do not drill the cork plate holes until they are ready to be assembled onto a horn, so catching one before this had happened was easy enough for them, I guess. (I know this because I once received four valves from them that had no cork plate holes, which pissed me off, because my shop equipment was not able to center, drill, and tap the holes as accurately as I liked — read: my cheap-assed Ryobi drill press had a terrible vise and the chuck had a lot of runout. I had to drill all the holes while holding each casing still with one hand and using a heavy Makita drill in the other, which is not all that conducive to accuracy. When I mentioned in my next order of valves to please make sure these holes were accurately drilled and tapped, they were like, "Whoops! Yes, we normally do this operation, but our man forgot! So sorry!)
The larger port is not actually larger. The end has been flared to fit the next valve, as they do for all their graduated bore horns. The "custom" operations are that the "wrong" port has to be flared, and the two threaded holes for the cork plate screws have to be oriented 90º counterclockwise to allow for the reversed rotation I need. I knew that if I provided enough information they would figure out the easiest way to make what I need. And it will be a factory-made part and not something I had to beat on in my carport.
Wunderbar!
Regardless, I was very pleased to discover that I could get my new 5th and 6th valves in nickel silver for like $40 extra, total. They will likely never wear out since the only failure point can be the softer brass rotors. These can easily be replaced so long as the walls and bearings of the casing are still in excellent condition, and they will be because they are the harder wearing of the two surfaces.
[The fact that they feed into my love for silver-colored things over gold-colored things is just gravy for me. And a very tasty gravy, that.]
So, back to the one-off valve: It is just a stock 186 5th valve in NS. They do not drill the cork plate holes until they are ready to be assembled onto a horn, so catching one before this had happened was easy enough for them, I guess. (I know this because I once received four valves from them that had no cork plate holes, which pissed me off, because my shop equipment was not able to center, drill, and tap the holes as accurately as I liked — read: my cheap-assed Ryobi drill press had a terrible vise and the chuck had a lot of runout. I had to drill all the holes while holding each casing still with one hand and using a heavy Makita drill in the other, which is not all that conducive to accuracy. When I mentioned in my next order of valves to please make sure these holes were accurately drilled and tapped, they were like, "Whoops! Yes, we normally do this operation, but our man forgot! So sorry!)
The larger port is not actually larger. The end has been flared to fit the next valve, as they do for all their graduated bore horns. The "custom" operations are that the "wrong" port has to be flared, and the two threaded holes for the cork plate screws have to be oriented 90º counterclockwise to allow for the reversed rotation I need. I knew that if I provided enough information they would figure out the easiest way to make what I need. And it will be a factory-made part and not something I had to beat on in my carport.
Wunderbar!
Last edited by the elephant on Mon Jan 17, 2022 10:09 am, edited 2 times in total.
- These users thanked the author the elephant for the post:
- prairieboy1 (Mon Jan 17, 2022 10:31 am)

- bloke
- Mid South Music
- Posts: 19373
- Joined: Thu Aug 13, 2020 8:55 am
- Location: western Tennessee - near Memphis
- Has thanked: 3859 times
- Been thanked: 4119 times
Re: The Great Kurath Re-Tubing
All great stuff. 
low-tech guy comment:
Due to the way they are shaped, old Erick Brand dent balls from those sets do a good (smooth/easy/factory-lookin’) job of flaring out rotor casing knuckles to a larger size - up to 3/4ths of an inch, obviously.
Since I prefer screwing around in other people’s forum threads over actually doing spending time working in the shop, I also will run a bicycle brake cable through one of those balls before pounding it in somewhere, so I can put the cable in the vice and yank the ball right back out.
low-tech guy comment:
Due to the way they are shaped, old Erick Brand dent balls from those sets do a good (smooth/easy/factory-lookin’) job of flaring out rotor casing knuckles to a larger size - up to 3/4ths of an inch, obviously.
Since I prefer screwing around in other people’s forum threads over actually doing spending time working in the shop, I also will run a bicycle brake cable through one of those balls before pounding it in somewhere, so I can put the cable in the vice and yank the ball right back out.
- These users thanked the author bloke for the post:
- the elephant (Mon Jan 17, 2022 10:16 am)
- the elephant
- Posts: 3414
- Joined: Thu Aug 13, 2020 8:39 am
- Location: 404 - Not Found
- Has thanked: 1907 times
- Been thanked: 1353 times
Re: The Great Kurath Re-Tubing
I was taught to use bicycle cable too, as it was much cheaper than ordering up the same from Ferree et al, and you can make whatever tool you need once you commit to making it yourself. However, I have the full set (up to .750") AND the lovely in-between set AND the set of five "extra" tuba balls, but none really fit this confusticated German metric-tun-not-whole-or-half-graduations Miraphone stuff, so that does not work. I have tried. Getting 19.54 (yeah, 19.5) stretched to match 20.35 is not going to work with the Ferree balls. I have a local "old fart/old school" machinist who is making me a set of slugs for my lathe and other general work that neatly fit all the most used Miraphone tubes to allow me to work on them more easily. I will see if he can grind me a set of five or six dent balls (with wire holes) of the sizes I need, too, since the bulk of my goofy work ideas use tubes of those specific sizes.
I need slugs/mandrels that are at least 8" long, and then the nice, watermelon-shaped balls with center holes in the following sizes:
.735"
.769"
.800"
.835"
.863"
.897"
.928"
.961"
.997"
1.006"
1.041"
This will make my silly ideas all much easier to realize with the final product looking pretty "factree"…
I need slugs/mandrels that are at least 8" long, and then the nice, watermelon-shaped balls with center holes in the following sizes:
.735"
.769"
.800"
.835"
.863"
.897"
.928"
.961"
.997"
1.006"
1.041"
This will make my silly ideas all much easier to realize with the final product looking pretty "factree"…
- These users thanked the author the elephant for the post:
- bloke (Mon Jan 17, 2022 10:20 am)

- the elephant
- Posts: 3414
- Joined: Thu Aug 13, 2020 8:39 am
- Location: 404 - Not Found
- Has thanked: 1907 times
- Been thanked: 1353 times
Re: The Great Kurath Re-Tubing
For expanding branch ends I have been using exhaust pipe expanders, but they mangle the tube enough that, even with very careful use and constant rotation to prevent waves and distortions, a ton of work with dent hammers still must be done to make it look like the tube came that way originally.

- bloke
- Mid South Music
- Posts: 19373
- Joined: Thu Aug 13, 2020 8:55 am
- Location: western Tennessee - near Memphis
- Has thanked: 3859 times
- Been thanked: 4119 times
Re: The Great Kurath Re-Tubing
While I am off on a BS sidebar regarding “making do“, it prompts me recall the time that I found a tuba bottom bow that was the perfect size overall, the perfect size on the large side, but a bit too small on the small side for the bell and the rest of the bugle I was using.
Finally, I found that a croquet ball - wrapped in two old towels, and pounded through the small end - was the magic formula to convert that bottom bow to just what I needed (actually: Buescher monster E-flat to Buescher 4/4 B-flat).
Finally, I found that a croquet ball - wrapped in two old towels, and pounded through the small end - was the magic formula to convert that bottom bow to just what I needed (actually: Buescher monster E-flat to Buescher 4/4 B-flat).
- These users thanked the author bloke for the post:
- the elephant (Mon Jan 17, 2022 10:26 am)
- the elephant
- Posts: 3414
- Joined: Thu Aug 13, 2020 8:39 am
- Location: 404 - Not Found
- Has thanked: 1907 times
- Been thanked: 1353 times
Re: The Great Kurath Re-Tubing
HAHAHA!!! I *love* redneck engineering. I do this sort of stuff all the time, and as I become less scared of the results (or more confident in my ability to finesse the results) I am doing more with Instrument repair.
BRAVO!
BRAVO!

