The Great Kurath Re-Tubing
- bloke
- Mid South Music
- Posts: 19349
- Joined: Thu Aug 13, 2020 8:55 am
- Location: western Tennessee - near Memphis
- Has thanked: 3854 times
- Been thanked: 4107 times
Re: The Great Kurath Re-Tubing
I discovered – a while back – in the real world (vs. from a book) that hardening stainless steel does not stiffen it.
I wondered if the bronze wouldn’t be much stiffer than brass, but I had trouble finding those stats on the Internet. I’m glad Rick knew where to look.
Based on experience – as well as looking at many old 1960s Miraphone and Melton levers – I suspect you can use brass for your hinge tube with no problem.
As you know, McMaster sells some 1/4 inch brass bar stock with a 1/8 inch hole inside. If you don’t have anything pre-drilled that is that beefy, you can either buy a piece from them or I probably have some around here - left over from cimbasso /Holton/etc. – that I could mail to you.
(For years - until I ran out of it, for such needs I cut up unfinished Bundy baritone saxophone keys that I bought from a scrapyard in South Bend, decades ago. That key stock is chunky – chunkier than Selmer, Paris key stock for baritone saxophones.)
I wondered if the bronze wouldn’t be much stiffer than brass, but I had trouble finding those stats on the Internet. I’m glad Rick knew where to look.
Based on experience – as well as looking at many old 1960s Miraphone and Melton levers – I suspect you can use brass for your hinge tube with no problem.
As you know, McMaster sells some 1/4 inch brass bar stock with a 1/8 inch hole inside. If you don’t have anything pre-drilled that is that beefy, you can either buy a piece from them or I probably have some around here - left over from cimbasso /Holton/etc. – that I could mail to you.
(For years - until I ran out of it, for such needs I cut up unfinished Bundy baritone saxophone keys that I bought from a scrapyard in South Bend, decades ago. That key stock is chunky – chunkier than Selmer, Paris key stock for baritone saxophones.)
- These users thanked the author bloke for the post:
- the elephant (Tue May 10, 2022 7:19 am)
- the elephant
- Posts: 3404
- Joined: Thu Aug 13, 2020 8:39 am
- Location: 404 - Not Found
- Has thanked: 1902 times
- Been thanked: 1345 times
Re: The Great Kurath Re-Tubing
I think I can drill out a 20 mm long hole, but I anticipate breaking several bits in the process. I have what I need, but I need the bits. I found them at McMaster-Carr. I am debating getting two very good ones or four good ones. I am very careful and do not need these bits specifically for anything, so I think four of the good ones ought to do it, as the two very good ones are more expensive. If I owned a much nicer drill press (no runout, a removable spindle, features that actually worked, a better bed, and an X/Y adjustable vise) I would just get one excellent bit in this size. But I own an old, beater Ryobi from 2008. So the good bits are probably what I will get. (Okay, maybe just three of them their shipping is very expensive, usually double the cost of what I buy, and no options are ever given.)
So when you say that brass would be okay, know that I am going to braze the hinge tube to stainless steel rod. I am not sure that will work so well. I know nickel silver is specified as working with the silver brazing rod and flux I am going to use, and brass is not recommended — I don't understand why this is. Anyway, so I will first try to make a hinge tube from the SSs and then from nickel silver, specifically to have a much thicker wall than the Allied flute hinge tube I have been using.
By the way, the lever I have on the horn right now is actually 4.5 mm and not 3.5, but the SS rod is 5.5 mm — I know it will make a difference, but maybe not one I can feel. Whatever. I love screwing around in the shop like this.
I'm learnding…
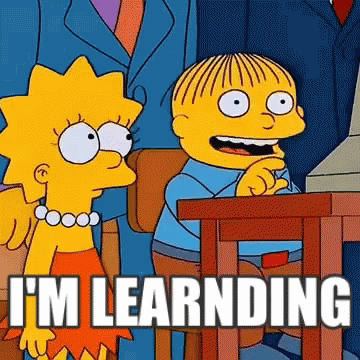
So when you say that brass would be okay, know that I am going to braze the hinge tube to stainless steel rod. I am not sure that will work so well. I know nickel silver is specified as working with the silver brazing rod and flux I am going to use, and brass is not recommended — I don't understand why this is. Anyway, so I will first try to make a hinge tube from the SSs and then from nickel silver, specifically to have a much thicker wall than the Allied flute hinge tube I have been using.
By the way, the lever I have on the horn right now is actually 4.5 mm and not 3.5, but the SS rod is 5.5 mm — I know it will make a difference, but maybe not one I can feel. Whatever. I love screwing around in the shop like this.
I'm learnding…
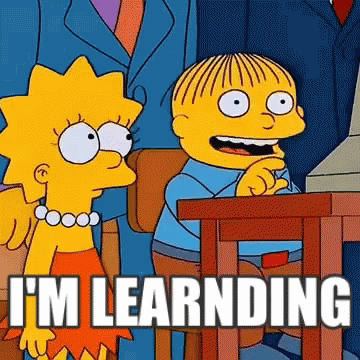

- bloke
- Mid South Music
- Posts: 19349
- Joined: Thu Aug 13, 2020 8:55 am
- Location: western Tennessee - near Memphis
- Has thanked: 3854 times
- Been thanked: 4107 times
Re: The Great Kurath Re-Tubing
Yeah… I continue to fail to embrace the fact that you are going with stainless steel. I’m finally embracing it. (i’m slow)
For a wildly-long J-shaped water key lever on the bottom of my cimbasso, I made it out of brass but merely lead-soldered a rib to it - most of the way down – oriented 90° to the to the primary piece of brass stock. That definitely stiffened it up plenty, and that goofy thing is possibly (??) 18 inches long.
For a wildly-long J-shaped water key lever on the bottom of my cimbasso, I made it out of brass but merely lead-soldered a rib to it - most of the way down – oriented 90° to the to the primary piece of brass stock. That definitely stiffened it up plenty, and that goofy thing is possibly (??) 18 inches long.
- These users thanked the author bloke for the post:
- the elephant (Tue May 10, 2022 2:47 pm)
- Rick Denney
- Resident Genius
- Posts: 1032
- Joined: Thu Aug 13, 2020 8:24 am
- Has thanked: 57 times
- Been thanked: 335 times
Re: The Great Kurath Re-Tubing
303 has a stiffness of 28,000 ksi, same as other austenitic stainless steels.
McMaster has 304 tubing, but if you need the 303 for the brazing, you'll have to make what you need.
There are alternatives to using a drill press. But I know what you mean: I have some craptastic Tractor Supply "Clarke Metal Working" drill press that I foolishly bought 12 or 15 years ago. I was able to tram in the table but the quill is off-center and there is 0.060" of runout at the end of a bit. (Yes, a whole 16th of an inch!) Grrrr! I thought it might the craptastic chuck that came with it, but I replaced the chuck with a good ball-bearing chuck. And then I thought it was the arbor, but I replaced that too--bought three from Amazon and kept only the best one. Nope--those are all straight. Sometimes the morse taper isn't machined properly, but this one is. The problem seems to be that the quill has a curve in it--the arbor hole is centered but the taper isn't exactly aligned with the center of quill travel, and so the farther the bit is from the arbor, the bigger the error circle it describes.
I've even tried shimming the morse taper with brass shim stock, and that helped, but now the tang is the only thing that keeps the arbor from spinning in the quill. Not good.
I've actually looked at some cheapie vertical mills from Grizzly and others, but I'm just not ready to spend that kind of money yet.
For drilling down the length of rod, though, I would prefer a lathe, and chuck the bit into the tailstock and the tubing in the lathe chuck. Feed the non-rotating bit onto the spinning tube using the tailstock leadscrew.
There might be a Makersmith club or some such in your area, Wade. I've looked into it here and the one here has all the basic machine tools plus some CNC stuff. I haven't joined it yet but when I have a project I will.
Rick "wants a small lathe and a mill now that there's a place for them" Denney
McMaster has 304 tubing, but if you need the 303 for the brazing, you'll have to make what you need.
There are alternatives to using a drill press. But I know what you mean: I have some craptastic Tractor Supply "Clarke Metal Working" drill press that I foolishly bought 12 or 15 years ago. I was able to tram in the table but the quill is off-center and there is 0.060" of runout at the end of a bit. (Yes, a whole 16th of an inch!) Grrrr! I thought it might the craptastic chuck that came with it, but I replaced the chuck with a good ball-bearing chuck. And then I thought it was the arbor, but I replaced that too--bought three from Amazon and kept only the best one. Nope--those are all straight. Sometimes the morse taper isn't machined properly, but this one is. The problem seems to be that the quill has a curve in it--the arbor hole is centered but the taper isn't exactly aligned with the center of quill travel, and so the farther the bit is from the arbor, the bigger the error circle it describes.
I've even tried shimming the morse taper with brass shim stock, and that helped, but now the tang is the only thing that keeps the arbor from spinning in the quill. Not good.
I've actually looked at some cheapie vertical mills from Grizzly and others, but I'm just not ready to spend that kind of money yet.
For drilling down the length of rod, though, I would prefer a lathe, and chuck the bit into the tailstock and the tubing in the lathe chuck. Feed the non-rotating bit onto the spinning tube using the tailstock leadscrew.
There might be a Makersmith club or some such in your area, Wade. I've looked into it here and the one here has all the basic machine tools plus some CNC stuff. I haven't joined it yet but when I have a project I will.
Rick "wants a small lathe and a mill now that there's a place for them" Denney
- These users thanked the author Rick Denney for the post:
- the elephant (Tue May 10, 2022 2:48 pm)
- bloke
- Mid South Music
- Posts: 19349
- Joined: Thu Aug 13, 2020 8:55 am
- Location: western Tennessee - near Memphis
- Has thanked: 3854 times
- Been thanked: 4107 times
Re: The Great Kurath Re-Tubing
For something that requires a lathe better than my crappy atlas one, I just take it 8 miles down to the small town near me and this talented old guy - who looks a farmhand - knocks it out for me…and for non-fancy prices.
bloke “far more practical than proud“
bloke “far more practical than proud“
- These users thanked the author bloke for the post:
- the elephant (Tue May 10, 2022 2:46 pm)
- bloke
- Mid South Music
- Posts: 19349
- Joined: Thu Aug 13, 2020 8:55 am
- Location: western Tennessee - near Memphis
- Has thanked: 3854 times
- Been thanked: 4107 times
Re: The Great Kurath Re-Tubing
EVENTUALLY (when I get around to it)...
I have an early not-worn/not-beat-up Hirsbrunner (Nirschl valveset) with the interchangeable receivers.
It came with a large shank receiver, but I was able to pick up two others (both: small shank).
One of them will remain small shank, and one will become "euphonium" shank.
With my Atlas lathe and my smaller Jarno reamer...now that's something I can easily handle here.
...I wonder how many of those vintage instruments are both
- not worn
...and...
- are featuring all three sizes of receivers.
please: no p.m.'s about this instrument. I'll eventually offer it up for sale, and it will be posted on tubaforum prior to any other venue.
I have an early not-worn/not-beat-up Hirsbrunner (Nirschl valveset) with the interchangeable receivers.
It came with a large shank receiver, but I was able to pick up two others (both: small shank).
One of them will remain small shank, and one will become "euphonium" shank.
With my Atlas lathe and my smaller Jarno reamer...now that's something I can easily handle here.
...I wonder how many of those vintage instruments are both
- not worn
...and...
- are featuring all three sizes of receivers.
please: no p.m.'s about this instrument. I'll eventually offer it up for sale, and it will be posted on tubaforum prior to any other venue.
- the elephant
- Posts: 3404
- Joined: Thu Aug 13, 2020 8:39 am
- Location: 404 - Not Found
- Has thanked: 1902 times
- Been thanked: 1345 times
Re: The Great Kurath Re-Tubing
Okay, still looking at NS 6mm round or 1/8"x1/4" flat bar stock, however…
I got the stainless to braze *very* nicely. I did a few experimental joints and had zero issues. Of course, the only one I remembered to photograph is the one where I did not feet in enough of the BAg-5 45% rod. It bonds very well and took little time as I decided to use my BA 6mm torch tip. Holy Mother of Gas, that tip works like a miracle!
I also was able to end drill some of the 5.5mm SS into a hinge tube. I was quite pleased by this!
So I have everything I need for the lever in SS, the ability to end drill a hinge tube, and then braze the parts together into a functioning lever.
Joe, I am even using one of the nifty 1.5" NS discs you sent me as the base for the saddle. This is going to be very nice, as well as quite stout, I think. I will cut, drill, and braze it all together tomorrow. I need a break right now.
All in all, today was quite the learning experience.
This will look nice and be very strong. I do not think that flex will be much of an issue.


Left: New, uber sexy lever. Right: Kurath saddle that will be crushed and melted.

This thing worms all over the place when heated enough to flow solder. You can see the end clock over about a millimeter. When it cools it worms back to its original shape — pulling the precisely aligned slide tube out of alignment. I can't wait to get this part off of this tuba. It works when it is part of a much heavier, larger piece (the Willson bracket that combines this section and the huge thumb ring "wing") bit it is a nightmare to work with it by itself.

I got the stainless to braze *very* nicely. I did a few experimental joints and had zero issues. Of course, the only one I remembered to photograph is the one where I did not feet in enough of the BAg-5 45% rod. It bonds very well and took little time as I decided to use my BA 6mm torch tip. Holy Mother of Gas, that tip works like a miracle!
I also was able to end drill some of the 5.5mm SS into a hinge tube. I was quite pleased by this!
So I have everything I need for the lever in SS, the ability to end drill a hinge tube, and then braze the parts together into a functioning lever.
Joe, I am even using one of the nifty 1.5" NS discs you sent me as the base for the saddle. This is going to be very nice, as well as quite stout, I think. I will cut, drill, and braze it all together tomorrow. I need a break right now.
All in all, today was quite the learning experience.

This will look nice and be very strong. I do not think that flex will be much of an issue.


Left: New, uber sexy lever. Right: Kurath saddle that will be crushed and melted.

This thing worms all over the place when heated enough to flow solder. You can see the end clock over about a millimeter. When it cools it worms back to its original shape — pulling the precisely aligned slide tube out of alignment. I can't wait to get this part off of this tuba. It works when it is part of a much heavier, larger piece (the Willson bracket that combines this section and the huge thumb ring "wing") bit it is a nightmare to work with it by itself.


-
- Posts: 1434
- Joined: Thu Aug 13, 2020 10:39 pm
- Location: SoCal
- Has thanked: 1561 times
- Been thanked: 467 times
Re: The Great Kurath Re-Tubing
Dang it! Now you have me wanting me to redo/replace the saddle on my little York Eb.
Thanks a lot!

Thanks a lot!

- These users thanked the author York-aholic for the post:
- the elephant (Tue May 10, 2022 7:45 pm)
Some old Yorks, Martins, and perhaps a King rotary valved CC
- the elephant
- Posts: 3404
- Joined: Thu Aug 13, 2020 8:39 am
- Location: 404 - Not Found
- Has thanked: 1902 times
- Been thanked: 1345 times
Re: The Great Kurath Re-Tubing
So after I had quit for the day the new thumb ring lock nut arrived on my doorstep. I liked the one I got at Ace but it was their largest and it was really too small for my taste. I had to hack off the base and then drill out and re-tap it to 1/4-28 threads.
The next week I found the same nut at the correct thread pitch and it was a lot larger.
Here is it. I hacked off the base and filed it smooth, then installed it. I like this a lot!

The next week I found the same nut at the correct thread pitch and it was a lot larger.
Here is it. I hacked off the base and filed it smooth, then installed it. I like this a lot!

- These users thanked the author the elephant for the post:
- York-aholic (Tue May 10, 2022 7:56 pm)

- the elephant
- Posts: 3404
- Joined: Thu Aug 13, 2020 8:39 am
- Location: 404 - Not Found
- Has thanked: 1902 times
- Been thanked: 1345 times
Re: The Great Kurath Re-Tubing
This might cause you to have a seizure. Proceed with caution.
I have overlaid the two swing paths of the current lever and the one I will make tomorrow.
The green/yellow stuff is the lever in the photograph. (Positions corrected for parallax.) The red/blue stuff is what I will have when I am finished. You can clearly see — well, clearly in a sort of an insane way — that the new lever will have a swing path that is much better for the thumb, comparatively.
The red thumb path is a lot better than the yellow one, but the blue path of the minibal and rod is FAR better than the green one.
Goodnight, y'all…

I have overlaid the two swing paths of the current lever and the one I will make tomorrow.
The green/yellow stuff is the lever in the photograph. (Positions corrected for parallax.) The red/blue stuff is what I will have when I am finished. You can clearly see — well, clearly in a sort of an insane way — that the new lever will have a swing path that is much better for the thumb, comparatively.
The red thumb path is a lot better than the yellow one, but the blue path of the minibal and rod is FAR better than the green one.
Goodnight, y'all…



- bloke
- Mid South Music
- Posts: 19349
- Joined: Thu Aug 13, 2020 8:55 am
- Location: western Tennessee - near Memphis
- Has thanked: 3854 times
- Been thanked: 4107 times
Re: The Great Kurath Re-Tubing
I just think you should convert any screws to Phillips - so this instrument will then be Yama-cool.
- the elephant
- Posts: 3404
- Joined: Thu Aug 13, 2020 8:39 am
- Location: 404 - Not Found
- Has thanked: 1902 times
- Been thanked: 1345 times
Re: The Great Kurath Re-Tubing
I'm about halfway there. The stainless was a marvelous choice. It works well, it brazes just like brass. It is difficult to bend with a 2 lb. "baby" sledgehammer, so bending it with my thumb will not be happening.
There is a lot more to do but I think all this work should come out as a genuine improvement to the tuba.






There is a lot more to do but I think all this work should come out as a genuine improvement to the tuba.






- These users thanked the author the elephant for the post (total 3):
- Rick Denney (Wed May 11, 2022 2:56 pm) • York-aholic (Wed May 11, 2022 3:02 pm) • Tubajug (Wed May 11, 2022 6:20 pm)

- Tubajug
- Posts: 745
- Joined: Thu Aug 13, 2020 10:27 am
- Location: Nebraska
- Has thanked: 225 times
- Been thanked: 202 times
Re: The Great Kurath Re-Tubing
Is the paddle a nickel disc?
Jordan
King 2341 with Holton Monster Eb Bell
King/Conn Eb Frankentuba
Pan AmeriConn BBb Helicon
Yamaha YBB-103
"No one else is placed exactly as we are in our opportune human orbits."
King 2341 with Holton Monster Eb Bell
King/Conn Eb Frankentuba
Pan AmeriConn BBb Helicon
Yamaha YBB-103
"No one else is placed exactly as we are in our opportune human orbits."
- the elephant
- Posts: 3404
- Joined: Thu Aug 13, 2020 8:39 am
- Location: 404 - Not Found
- Has thanked: 1902 times
- Been thanked: 1345 times
Re: The Great Kurath Re-Tubing
The bracket/saddle is on the horn. I was too lazy to swap torch tips. I will never make that mistake again. That big honking tip I use to braze played havoc with my brain, and the work I did was apprentice-level sloppy. It was frustrating. But I was already in a bad mood, so, you know, everyone: pile on… <sigh>
I was in a pretty great mood today up until about 6:00 p.m. when yet another Irwin M3x0.5 tap broke off in the work for me. That is four in the last month. I have used about ten sizes of taps recently for projects around the house, but this size keeps breaking. I suspect they are having QC issues at that plant on that line. Because this is ridiculous. I have solid skills with threading things and seldom snap taps off. Well, until this last batch of four M3x0.5 doozies came into my life. Super brittle, they break when oiled, when dry, but mostly when backing out to break a chip. TINK. The tap is toast; the workpiece is toast, and my day is toast.
So I was wanting to wrap things up and I did the no-no of trying to use this big-ass torch tip for a little job.
I am an idiot.
The bracket is on. It fits well. (I did a spiffy job of shaping the disc into a foot that fits the piston casing like it was made for that purpose. Nice!
So, here is where this project is now…
Bracket on and made. Axle made. First experiments with the stainless stuff came out nice, and now that I have the pivot point in actual three-dimensional goodness I can take careful measurements of the lever I made today and make the final version I may not get to that this week, though as I am about to have a spate of playing all over the place for several days.
I took photos to confirm my measurements/adjustments to the lever, and they are below.
I must say that the stainless is nothing at all like the nickel silver I used. I cannot even begin to flex this lever; not at all. I have not yet tried to clean it up. I did not want to eat a bunch of buffing compound as I had a pretty big lunch and "wanted to watch my carb intake". I'll get to that sometime while I am busy being a tuba player. It will only take me an hour to set up, do the work, and tear down, so I can do it early in the morning. I am worried about this, as the material gets a sort of rough texture when it is brazed, and cleanup is a bit different than what I normally do.
The huge, disappointing mess on my valve casings will get cleaned up in stages, and I am not pleased about it, but there it is.
Here are some pics…
The hated Kurath bracket is GONE! HOORAY! The new bracket is installed. There is a lot of crap to clean up. Oh, well. I like the assembly that I made.


Lever up… The thumb pad portion needs to be 10 mm longer and the angle needs to be a bit different.

Lever down… Yep, it needs to be longer. Not a problem.

The drop-bar DOES NOT FLEX AT ALL. Whew! I tried a different joint this time as per a suggestion from a friend. It worked well, but I did not see that it was a little out of alignment. I can fix that next time. I think I like the joint. Instead of wallowing out a radiused end to fit over a perpendicular bar, I cut a flat notch into the perpendicular bar and left the end of the other one flat, to make a very strong butt joint. I think it worked well. I just need to triple-check that nothing slipped when I tightened the brazing fixture down. (I had gobs of flux on there, and could not see it. But I could have felt the edge, and I didn't. I will do this in the future when I have to glob on that much brazing flux paste. THIS IS A STRONG LEVER!

I was in a pretty great mood today up until about 6:00 p.m. when yet another Irwin M3x0.5 tap broke off in the work for me. That is four in the last month. I have used about ten sizes of taps recently for projects around the house, but this size keeps breaking. I suspect they are having QC issues at that plant on that line. Because this is ridiculous. I have solid skills with threading things and seldom snap taps off. Well, until this last batch of four M3x0.5 doozies came into my life. Super brittle, they break when oiled, when dry, but mostly when backing out to break a chip. TINK. The tap is toast; the workpiece is toast, and my day is toast.
So I was wanting to wrap things up and I did the no-no of trying to use this big-ass torch tip for a little job.
I am an idiot.
The bracket is on. It fits well. (I did a spiffy job of shaping the disc into a foot that fits the piston casing like it was made for that purpose. Nice!
So, here is where this project is now…
Bracket on and made. Axle made. First experiments with the stainless stuff came out nice, and now that I have the pivot point in actual three-dimensional goodness I can take careful measurements of the lever I made today and make the final version I may not get to that this week, though as I am about to have a spate of playing all over the place for several days.
I took photos to confirm my measurements/adjustments to the lever, and they are below.
I must say that the stainless is nothing at all like the nickel silver I used. I cannot even begin to flex this lever; not at all. I have not yet tried to clean it up. I did not want to eat a bunch of buffing compound as I had a pretty big lunch and "wanted to watch my carb intake". I'll get to that sometime while I am busy being a tuba player. It will only take me an hour to set up, do the work, and tear down, so I can do it early in the morning. I am worried about this, as the material gets a sort of rough texture when it is brazed, and cleanup is a bit different than what I normally do.
The huge, disappointing mess on my valve casings will get cleaned up in stages, and I am not pleased about it, but there it is.
Here are some pics…
The hated Kurath bracket is GONE! HOORAY! The new bracket is installed. There is a lot of crap to clean up. Oh, well. I like the assembly that I made.


Lever up… The thumb pad portion needs to be 10 mm longer and the angle needs to be a bit different.

Lever down… Yep, it needs to be longer. Not a problem.

The drop-bar DOES NOT FLEX AT ALL. Whew! I tried a different joint this time as per a suggestion from a friend. It worked well, but I did not see that it was a little out of alignment. I can fix that next time. I think I like the joint. Instead of wallowing out a radiused end to fit over a perpendicular bar, I cut a flat notch into the perpendicular bar and left the end of the other one flat, to make a very strong butt joint. I think it worked well. I just need to triple-check that nothing slipped when I tightened the brazing fixture down. (I had gobs of flux on there, and could not see it. But I could have felt the edge, and I didn't. I will do this in the future when I have to glob on that much brazing flux paste. THIS IS A STRONG LEVER!

Last edited by the elephant on Wed May 11, 2022 7:08 pm, edited 1 time in total.

- the elephant
- Posts: 3404
- Joined: Thu Aug 13, 2020 8:39 am
- Location: 404 - Not Found
- Has thanked: 1902 times
- Been thanked: 1345 times
Re: The Great Kurath Re-Tubing
It is nickel silver flat sheet stock, like a fat, curved-sided rectangle, bent over a steel rod. It is in the lower right of this photograph. I scribed the shape onto the surface and then did a quick cutout job prior to the pic. After that, I did the more careful shaping of the edge and then hammered it over a mandrel.
If you look carefully, you can see the scribe line in the upper left corner of the part. I used the Sharpie to make it easier for me to see the scribe line outdoors where I work, Yes, there is also a circle scribed there that I ended up not liking for the platen as it was too small for my fat thumb.

Here are a couple of views of the finished platen. And yes, I "un-brazed" it and used it again. It looks weird, but I like how it feels.


- These users thanked the author the elephant for the post (total 3):
- York-aholic (Wed May 11, 2022 7:56 pm) • Tubajug (Wed May 11, 2022 8:04 pm) • prairieboy1 (Thu May 12, 2022 9:41 am)

- the elephant
- Posts: 3404
- Joined: Thu Aug 13, 2020 8:39 am
- Location: 404 - Not Found
- Has thanked: 1902 times
- Been thanked: 1345 times
Re: The Great Kurath Re-Tubing
In case anyone reading this G.A.S. and also managed to miss my post about it, here is a link to my horn/tuba duet book, completely reset, including 39 pages of fully legal arrangements.
Last edited by the elephant on Wed May 18, 2022 8:30 pm, edited 1 time in total.

- the elephant
- Posts: 3404
- Joined: Thu Aug 13, 2020 8:39 am
- Location: 404 - Not Found
- Has thanked: 1902 times
- Been thanked: 1345 times
Re: The Great Kurath Re-Tubing
Okay, so version 3 of the lever did not fly, either. It has the same issue, but there is no flex in the part. I have come to realize that it is definitely the design. It is too long to be essentially a triangle pinned at two sides while the third is being smashed down by my fat hand.
So there is no way to make the lever *feel* like I want. It was like this before, but the lever was so much shorter that the flexiness was nothing I paid any mind to. The greater length means the play is just that much more apparent.
So I will make one more, and I will do some work using flat bar stock despite my hating that sort of lever. Whatever. I will likely remove it as soon as I am comfortable taking off the six valve "training wheels". Time for the fat guy to man up.
Anyway, the experience of using the stainless steel was pretty cool. The lever I got from the material is really good, but the angles are still a bit off from what I want. Again, this is a much more complex problem than most levers. I am quick at making very nice levers, usually, but this one is a real stinker of a math problem. I am pleased that the SS worked so well, and this last lever has a hinge tube that I center/end drilled by eye that is very close to dead-on, but still not great. I hope to have a lathe by Christmas, as many of the things I have worked on recently would have been very fast, easy, and ACCURATE if I even had a working lathe. As things stand, though, my "eyecrometer" is not as accurate as it was before I developed diabetes.
This is the current effort, and the stainless polished up very nicely with the green buffing compound.



So there is no way to make the lever *feel* like I want. It was like this before, but the lever was so much shorter that the flexiness was nothing I paid any mind to. The greater length means the play is just that much more apparent.
So I will make one more, and I will do some work using flat bar stock despite my hating that sort of lever. Whatever. I will likely remove it as soon as I am comfortable taking off the six valve "training wheels". Time for the fat guy to man up.
Anyway, the experience of using the stainless steel was pretty cool. The lever I got from the material is really good, but the angles are still a bit off from what I want. Again, this is a much more complex problem than most levers. I am quick at making very nice levers, usually, but this one is a real stinker of a math problem. I am pleased that the SS worked so well, and this last lever has a hinge tube that I center/end drilled by eye that is very close to dead-on, but still not great. I hope to have a lathe by Christmas, as many of the things I have worked on recently would have been very fast, easy, and ACCURATE if I even had a working lathe. As things stand, though, my "eyecrometer" is not as accurate as it was before I developed diabetes.
This is the current effort, and the stainless polished up very nicely with the green buffing compound.



- These users thanked the author the elephant for the post (total 2):
- prairieboy1 (Wed May 18, 2022 8:35 pm) • Rick Denney (Sat May 21, 2022 7:17 pm)

- the elephant
- Posts: 3404
- Joined: Thu Aug 13, 2020 8:39 am
- Location: 404 - Not Found
- Has thanked: 1902 times
- Been thanked: 1345 times
Re: The Great Kurath Re-Tubing
I watch too many automotive frame-off restoration videos. I have come to realize that I am doing the same sort of work to my tubas. I am doing the thing whereby you tear a car apart, fully rebuild everything, make massive modifications and improvements, slap it back together to get it running and dial in everything, then take it completely apart and clean up all the halfway work you did while slapping it together to make sure everything is working the way you want.
That means that what I have said all along about all my horns, is that there will come a day when I have it all fixed to my satisfaction and they will have to come back apart and be put together really carefully. I might even (*gasp*) buff and lacquer or silver plate them. Joe has shown me that this is not difficult, just expensive, and the results are very nice, indeed. I know I can lacquer the horns here at the house, but I would need to practice on a few junker horns first. I used to be pretty good at it. But that was in the 1990s so my skills and confidence are pretty badly atrophied. I have a decent trumpet that is in need of new lacquer, so I will probably start with that. Having two of my horns set up with removable valve sections takes a lot of the stress out of the picture.
As much as I don't want to do this, I have said all along that I would. And all sins can be corrected at that time. There are some small alignment issues on my *good* 186 that I could address at that time. There is a multitude of details on this tuba and the Holton that need to be looked at to make me happy.
So this summer I will finally purchase a spray rig and start painting stuff with it, eventually moving over to clear lacquer on polished brass.
We'll see where this leads me.
Until then, I have to build these freaking levers for my F tuba.
I'll post more if I ever get anything accomplished.
Ciao, y'all.
That means that what I have said all along about all my horns, is that there will come a day when I have it all fixed to my satisfaction and they will have to come back apart and be put together really carefully. I might even (*gasp*) buff and lacquer or silver plate them. Joe has shown me that this is not difficult, just expensive, and the results are very nice, indeed. I know I can lacquer the horns here at the house, but I would need to practice on a few junker horns first. I used to be pretty good at it. But that was in the 1990s so my skills and confidence are pretty badly atrophied. I have a decent trumpet that is in need of new lacquer, so I will probably start with that. Having two of my horns set up with removable valve sections takes a lot of the stress out of the picture.
As much as I don't want to do this, I have said all along that I would. And all sins can be corrected at that time. There are some small alignment issues on my *good* 186 that I could address at that time. There is a multitude of details on this tuba and the Holton that need to be looked at to make me happy.
So this summer I will finally purchase a spray rig and start painting stuff with it, eventually moving over to clear lacquer on polished brass.
We'll see where this leads me.
Until then, I have to build these freaking levers for my F tuba.
I'll post more if I ever get anything accomplished.
Ciao, y'all.

- These users thanked the author the elephant for the post:
- prairieboy1 (Wed May 18, 2022 8:35 pm)

- the elephant
- Posts: 3404
- Joined: Thu Aug 13, 2020 8:39 am
- Location: 404 - Not Found
- Has thanked: 1902 times
- Been thanked: 1345 times
Re: The Great Kurath Re-Tubing
I followed a dead-end idea today. That was a very complex and time-consuming lever.
Then I revisited my other lever (the stainless one) that is so dang stout that I love it, but the angles and lengths are not where they need to be, so I also loathe it. I took my time and came up with a perfect lever for this situation and my hand.
Then I ruined it.
So I remade that, as identically as I could, and it is really great. Details later. Here are some pics. My hand position is so much better now, this tuba feels like a different instrument to me.
I would type more, but this took me nine hours today and I am simply shot. In those nine hours, I also did several needed tasks for my shop, including some rearrangement of my huge, red, rolling tool cabinets. I also tore down my brazing jig and cleaned the snot out of it, and filed the six jaw pieces flat and smooth again. Much better. Then I spent about two hours working out what I did not like about the last lever and then transferring that to paper, which took another couple of hours. So I guess I actually spent five hours making three levers.
In the end, I wrapped it up at like 8:30 p.m. and I need to eat and read and go to bed.
Looking at it, I am *already* seeing possible improvements. GAAAH! SOMEBODY MAKE IT STOP!

I reused the Kurath platen as it is of a superior size and shape compared with the one I made.

Up — No pain!

Down — Also no pain!

Then I revisited my other lever (the stainless one) that is so dang stout that I love it, but the angles and lengths are not where they need to be, so I also loathe it. I took my time and came up with a perfect lever for this situation and my hand.
Then I ruined it.
So I remade that, as identically as I could, and it is really great. Details later. Here are some pics. My hand position is so much better now, this tuba feels like a different instrument to me.
I would type more, but this took me nine hours today and I am simply shot. In those nine hours, I also did several needed tasks for my shop, including some rearrangement of my huge, red, rolling tool cabinets. I also tore down my brazing jig and cleaned the snot out of it, and filed the six jaw pieces flat and smooth again. Much better. Then I spent about two hours working out what I did not like about the last lever and then transferring that to paper, which took another couple of hours. So I guess I actually spent five hours making three levers.
In the end, I wrapped it up at like 8:30 p.m. and I need to eat and read and go to bed.
Looking at it, I am *already* seeing possible improvements. GAAAH! SOMEBODY MAKE IT STOP!

I reused the Kurath platen as it is of a superior size and shape compared with the one I made.

Up — No pain!

Down — Also no pain!


- the elephant
- Posts: 3404
- Joined: Thu Aug 13, 2020 8:39 am
- Location: 404 - Not Found
- Has thanked: 1902 times
- Been thanked: 1345 times
Re: The Great Kurath Re-Tubing
This looks horrible and convoluted, but I assure you it is quite simple. The 6th linkage will be a bear to bend, but other than that it is pretty straightforward. Note that any lever that is not straight will have a tendency to flop around between the two ball ends. I have some of those pillow blocks I made (the little ones, not the bigass Lego-looking things) that will keep these long rods aligned nicely. I worked all this out some time back and then got on a tangent and ended up dropping that idea, but the blocks mostly made. These work well as a guide to keep the floppiness from rearing its ugly head.
Essentially, 6th wraps through the rotors and then bends upwards and is routed through two blocks. There is a short, straight rod between the lever and the long rod.
The 5th is operable by both hands, so it runs in a Z from the valve up to the thumb lever in a location where there is zero flexiness. The bottom of the drop rod where the 5th link arm currently lives will be connected to the upper 5th lever via a short, straight rod. The upper and lower connection points have hard limits of travel, and there is one in each direction, so the flexiness issue is more or less eliminated.
Now, don't laugh at my childlike illustration, or at least don't let me hear you laughing at it. I'd likely cry at this point. HAHAHA!!!

Essentially, 6th wraps through the rotors and then bends upwards and is routed through two blocks. There is a short, straight rod between the lever and the long rod.
The 5th is operable by both hands, so it runs in a Z from the valve up to the thumb lever in a location where there is zero flexiness. The bottom of the drop rod where the 5th link arm currently lives will be connected to the upper 5th lever via a short, straight rod. The upper and lower connection points have hard limits of travel, and there is one in each direction, so the flexiness issue is more or less eliminated.
Now, don't laugh at my childlike illustration, or at least don't let me hear you laughing at it. I'd likely cry at this point. HAHAHA!!!

- These users thanked the author the elephant for the post (total 3):
- Tubajug (Sat May 21, 2022 6:26 am) • York-aholic (Sat May 21, 2022 7:10 am) • prairieboy1 (Sat May 21, 2022 3:19 pm)
