Kurath/Willson F Tuba — Adding a 6th Valve
- the elephant
- Posts: 3413
- Joined: Thu Aug 13, 2020 8:39 am
- Location: 404 - Not Found
- Has thanked: 1906 times
- Been thanked: 1346 times
Re: Kurath/Willson F Tuba — Adding a 6th Valve
And because someone will ask:
Starting with low C
C - 13 or 4 (as needed)
B - 46
Bb - 45
A - 456
Ab - 1456 (This ought to be flat but it isn't.) EDIT: It is. Changed to 134, which is very nice.)
G - 12456 or 3456 (I'll decide at rehearsal tomorrow night which one works better for me.)
Gb - 23456
F - 0 (loud, rude, sharp, and squirrelly) — or — 13456 (sweet, delicate, focused, and IN TUNE)
Also, the top line Ab is screaming sharp played 2 but is flat played 23. However, it is dead on played 6th. Interesting. I am sure I will discover other fun stuff over time. I only played the horn for about two hours tonight. I need to adjust the two rings for my thumb and pinky. I think the pinky needs to be in a hook like on a trumpet. I have some difficulty moving my hand out of the rings and then back in while playing, so opening up that ring would make it a much easier target for me. And where I have the thumb ring is just wrong. I need to move it about an inch to one side.
Starting with low C
C - 13 or 4 (as needed)
B - 46
Bb - 45
A - 456
Ab - 1456 (This ought to be flat but it isn't.) EDIT: It is. Changed to 134, which is very nice.)
G - 12456 or 3456 (I'll decide at rehearsal tomorrow night which one works better for me.)
Gb - 23456
F - 0 (loud, rude, sharp, and squirrelly) — or — 13456 (sweet, delicate, focused, and IN TUNE)
Also, the top line Ab is screaming sharp played 2 but is flat played 23. However, it is dead on played 6th. Interesting. I am sure I will discover other fun stuff over time. I only played the horn for about two hours tonight. I need to adjust the two rings for my thumb and pinky. I think the pinky needs to be in a hook like on a trumpet. I have some difficulty moving my hand out of the rings and then back in while playing, so opening up that ring would make it a much easier target for me. And where I have the thumb ring is just wrong. I need to move it about an inch to one side.
Last edited by the elephant on Mon Feb 20, 2023 11:58 am, edited 1 time in total.
- These users thanked the author the elephant for the post:
- bloke (Sun Feb 19, 2023 9:47 pm)

- bloke
- Mid South Music
- Posts: 19367
- Joined: Thu Aug 13, 2020 8:55 am
- Location: western Tennessee - near Memphis
- Has thanked: 3857 times
- Been thanked: 4117 times
Re: Kurath/Willson F Tuba — Adding a 6th Valve
to Wade:
As you've seen me post, playing the five valve cimbasso with the #2 slide trigger often confuses me.
I'm not above writing in low pitch fingerings and even a "T" over F-sharp and B.
The six valve system makes a ton of sense. It's nothing more than a manual compensating system...well... until you get past low A, and have to mix and match
.
-------------
If that single valve works for that A-flat, that's great, but otherwise you have several ways to lower your instrument a major third: 23, 126, & 36.
As you've seen me post, playing the five valve cimbasso with the #2 slide trigger often confuses me.
I'm not above writing in low pitch fingerings and even a "T" over F-sharp and B.
The six valve system makes a ton of sense. It's nothing more than a manual compensating system...well... until you get past low A, and have to mix and match

-------------
If that single valve works for that A-flat, that's great, but otherwise you have several ways to lower your instrument a major third: 23, 126, & 36.
Last edited by bloke on Sun Feb 19, 2023 9:55 pm, edited 1 time in total.
- These users thanked the author bloke for the post:
- the elephant (Sun Feb 19, 2023 9:52 pm)
- the elephant
- Posts: 3413
- Joined: Thu Aug 13, 2020 8:39 am
- Location: 404 - Not Found
- Has thanked: 1906 times
- Been thanked: 1346 times
Re: Kurath/Willson F Tuba — Adding a 6th Valve
I have to write in fingerings or accidentals all the time. I penciled in a fingering chart on one of my orchestra parts for this week. I think I will be consulting it at least a few times, heh, heh…
This system really *is* better.
This system really *is* better.

- bloke
- Mid South Music
- Posts: 19367
- Joined: Thu Aug 13, 2020 8:55 am
- Location: western Tennessee - near Memphis
- Has thanked: 3857 times
- Been thanked: 4117 times
Re: Kurath/Willson F Tuba — Adding a 6th Valve
Never mind about those alternates I mentioned in the previous post. The ones involving 6 are obviously going to be flatter than 23... but of course you already know that.
-
- Posts: 1436
- Joined: Thu Aug 13, 2020 10:39 pm
- Location: SoCal
- Has thanked: 1565 times
- Been thanked: 468 times
Re: Kurath/Willson F Tuba — Adding a 6th Valve
That makes my brain hurt! I was going to say I’ll stick with my 5v Eb but now I’m thinking my 4v 712, or maybe just buy a sousaphone and call it good.the elephant wrote: ↑Sun Feb 19, 2023 9:42 pm And because someone will ask:
Starting with low C
C - 13 or 4 (as needed)
B - 46
Bb - 45
A - 456
Ab - 1456 (This ought to be flat but it isn't.)
G - 12456 or 3456 (I'll decide at rehearsal tomorrow night which one works better for me.)
Gb - 23456
F - 0 (loud, rude, sharp, and squirrelly) — or — 13456 (sweet, delicate, focused, and IN TUNE)

- These users thanked the author York-aholic for the post:
- the elephant (Sun Feb 19, 2023 11:34 pm)
Some old Yorks, Martins, and perhaps a King rotary valved CC
- bloke
- Mid South Music
- Posts: 19367
- Joined: Thu Aug 13, 2020 8:55 am
- Location: western Tennessee - near Memphis
- Has thanked: 3857 times
- Been thanked: 4117 times
Re: Kurath/Willson F Tuba — Adding a 6th Valve
I see that reaction from tuba players all the time. I guess an $8 plastic soprano recorder is just too complicated. It even has one hole that you only cover half of it sometimes.
- These users thanked the author bloke for the post:
- jonesbrass (Mon Feb 20, 2023 8:58 am)
- the elephant
- Posts: 3413
- Joined: Thu Aug 13, 2020 8:39 am
- Location: 404 - Not Found
- Has thanked: 1906 times
- Been thanked: 1346 times
Re: Kurath/Willson F Tuba — Adding a 6th Valve
And for the "More Valves = Stuffy" crowd, I added a valve and there is no difference whatsoever.
- These users thanked the author the elephant for the post (total 3):
- York-aholic (Mon Feb 20, 2023 8:20 am) • jonesbrass (Mon Feb 20, 2023 8:57 am) • bloke (Mon Feb 20, 2023 9:12 am)

- bloke
- Mid South Music
- Posts: 19367
- Joined: Thu Aug 13, 2020 8:55 am
- Location: western Tennessee - near Memphis
- Has thanked: 3857 times
- Been thanked: 4117 times
Re: Kurath/Willson F Tuba — Adding a 6th Valve
yeah...I'm headed out to the shop today to remove ALL of the valves from the big Miraphone...the elephant wrote: ↑Mon Feb 20, 2023 8:06 am And for the "More Valves = Stuffy" crowd, I added a valve and there is no difference whatsoever.

(actually, to - hopefully - get stop rod assemblies installed on the #1, #3, and #5 slides...' tired of them slipping out, slipping in, or falling out).
bloke "air column vibration'...not 'air flow', but there are quite a few things that I'm tired of stating over-and-over, which is why I don't teach...and - were it that I did teach - all of the group-thinkists would shun/scoff/etc., and my students would likely be blacklisted."
- the elephant
- Posts: 3413
- Joined: Thu Aug 13, 2020 8:39 am
- Location: 404 - Not Found
- Has thanked: 1906 times
- Been thanked: 1346 times
Re: Kurath/Willson F Tuba — Adding a 6th Valve
No, I am addressing the crowd who think that a 4th valve will screw up how a three-valved tuba "blows" or how adding a 5th valve will ruin a horn's "blow".
I used to buy into that because one of the most respected players/teachers in the US told me that about his horn:
If I added a 5th valve it would just screw up how the horn blows.
In 1985 I was prepared to believe this. Today, not so much. I am not saying this man was WRONG per se, just misinformed. That idea gets a lot of play in this community, even today.
I *like* axial-flow valves. I just think they are a mechanical P.O.S. that no one yet has figured out how to make properly. The modern ones with pressed-in roller bearings are a step in the wrong direction. Also, I agree with Joe that when you remove ALL resistance you kill the horn, so some horns are as good as they will ever get with rotors or pistons, that they were initially very well-designed. Adding valves, changing the type of valves, or moving each slide to an open wrap will not affect them enough to merit the cost of the work. And some horns were poorly designed, make a great sound, and could benefit from opening them up, however, you choose to do it.
The trick is to do this type of work enough to know beforehand what will or will not work or reach the point of diminishing returns.
Personally, I think ALL instruments that are in stock condition from big brands (esp. M-W, IMHO) can benefit from a complete rebuild. All instruments made by the big shops are compromises. They prototype until they have their ideal instrument, then they prototype that instrument until they have a profitable version. I have sought out and owned a lot of prototype instruments. If they are good they usually are a little better than the production version, using more handmade branches and such. (Some makers are infamous for using as many existing parts as they can to make a new model.)
Because of this, I think most production tubas that are slapped together in an assembly line of sorts can benefit from a lot of very careful handwork to make joints fit better, to correct alignment, to get details like burs in the valve guide channels, etc. (I'm talking to you, King.) All I have done to my Kurath, Holton 345, and Mirafone 186 is rebuild them with all the compromises or shortcuts deleted. If they had not needed to make money, and only built horns to be works of art devoid of the realities of business, I think they would have built these three tubas a lot more as I have made them.
And I just steered the conversational "wagon train" right off the cliff. (Sorry.) Yes, I like axial-flow valves — in theory — but in practice, as a mechanical device, they still are not ready for Prime Time, IMHO. I have installed many of them onto old Bach trombones over the years, and my work is as accurate (or more so?) than that of a hurried line worker at Conn-Selmer because I can take the time to do things over until they are perfect. And these valves simply hang partially closed after a certain amount of use. They just do. Or they leak. Teflon coatings, hard anodizing, roller bearings: they still hang partially closed. The theory is excellent but someone needs to rethink the Thayer valve, again: IMHO, based on about a quarter of a century of experience working on them. But for horns that need to be opened up as a Thayer can do, they are great. Just so long as you do not need them to work 100% of the time, heh, heh…
I used to buy into that because one of the most respected players/teachers in the US told me that about his horn:
If I added a 5th valve it would just screw up how the horn blows.
In 1985 I was prepared to believe this. Today, not so much. I am not saying this man was WRONG per se, just misinformed. That idea gets a lot of play in this community, even today.
I *like* axial-flow valves. I just think they are a mechanical P.O.S. that no one yet has figured out how to make properly. The modern ones with pressed-in roller bearings are a step in the wrong direction. Also, I agree with Joe that when you remove ALL resistance you kill the horn, so some horns are as good as they will ever get with rotors or pistons, that they were initially very well-designed. Adding valves, changing the type of valves, or moving each slide to an open wrap will not affect them enough to merit the cost of the work. And some horns were poorly designed, make a great sound, and could benefit from opening them up, however, you choose to do it.
The trick is to do this type of work enough to know beforehand what will or will not work or reach the point of diminishing returns.
Personally, I think ALL instruments that are in stock condition from big brands (esp. M-W, IMHO) can benefit from a complete rebuild. All instruments made by the big shops are compromises. They prototype until they have their ideal instrument, then they prototype that instrument until they have a profitable version. I have sought out and owned a lot of prototype instruments. If they are good they usually are a little better than the production version, using more handmade branches and such. (Some makers are infamous for using as many existing parts as they can to make a new model.)
Because of this, I think most production tubas that are slapped together in an assembly line of sorts can benefit from a lot of very careful handwork to make joints fit better, to correct alignment, to get details like burs in the valve guide channels, etc. (I'm talking to you, King.) All I have done to my Kurath, Holton 345, and Mirafone 186 is rebuild them with all the compromises or shortcuts deleted. If they had not needed to make money, and only built horns to be works of art devoid of the realities of business, I think they would have built these three tubas a lot more as I have made them.
And I just steered the conversational "wagon train" right off the cliff. (Sorry.) Yes, I like axial-flow valves — in theory — but in practice, as a mechanical device, they still are not ready for Prime Time, IMHO. I have installed many of them onto old Bach trombones over the years, and my work is as accurate (or more so?) than that of a hurried line worker at Conn-Selmer because I can take the time to do things over until they are perfect. And these valves simply hang partially closed after a certain amount of use. They just do. Or they leak. Teflon coatings, hard anodizing, roller bearings: they still hang partially closed. The theory is excellent but someone needs to rethink the Thayer valve, again: IMHO, based on about a quarter of a century of experience working on them. But for horns that need to be opened up as a Thayer can do, they are great. Just so long as you do not need them to work 100% of the time, heh, heh…

- the elephant
- Posts: 3413
- Joined: Thu Aug 13, 2020 8:39 am
- Location: 404 - Not Found
- Has thanked: 1906 times
- Been thanked: 1346 times
Re: Kurath/Willson F Tuba — Adding a 6th Valve
Yeah, so I switched over to my Sellmanserger Solo single-piece (which is not the same as my three-piece) and spent an hour and a half on New World's outer two movements. After some frustration and a lot of repositioning of slides all over the horn, I now have a fingering system that plays quite well. I incorporated a bunch of standard alternates that I *would* have used in the past — except that they made the low register so out of tune on this tuba — and now I have to do ZERO slide pulling!
NONE!
I may have to add a 6th to my Holton for sh**ts and giggles. Remember that the 5th section on that tuba is separate from the removable piston section, so I could make a 5th/6th section that was completely separate from the current 5th section, so if I did not like it I could change it back with pretty much zero work. I could also just use it when I need it. (There are a number of pieces where such a thing could be very handy. Currently, I can remove the 5th valve if I do not need it, saving a bit of weight on my back and in my lap. (I was honestly surprised at how much of a difference this could make to my back over a couple of weeks of work.)
This special 5th/6th section could have the 6th lever integral to it so that there is no vestigial lever bracket as there is when I remove the 5th valve from the tuba. (In fact, I no longer remove the lever, but lock it down with a little tchotchke I made.)
So, now that the better mouthpiece is back in play and I have really gone over the tuba to work out fingerings and slide settings, in the range directly affected by the 6th valve, the above fingering system works, but the Ab became too low. 1245 is also too low. I ended up using 134, which is spot on. Of course, this will become a technical hurdle for a while as it is outside of my "pattern" but it works so well for me that it shouldn't be an obstacle for very long.
New World I and IV rock on this tuba. It is a lot more aggressive than the Mirafone in that register. I am not sure I want that, though, so after tonight I may opt for the mellower 186. If I draw attention to myself the conductor may remember that I am not supposed to be playing on the outer movements and then I'll have to do the whole "wait to play 14 notes and then wait for the piece to end" ordeal.
Oh, and the very flat E/Eb/D just below the staff is mysteriously in tune now. I did some work on the second slide in prep to cut the outer tubes. (i.e. I cut the inner tubes) and suddenly everything right there is great except that the Eb is still a hair under pitch.
I have no idea why this is, but it is real and not a placebo effect. I was not looking for this result AT ALL in this series of modifications. In fact, I was still lipping these notes up when I noticed that I was overdoing it. The tuner says they are where they need to be, more or less.
WTF?
Currently, it is a beautiful day in Yazoo City, Mississippi, despite the dreary overcast. Clouds will not be raining on this parade.
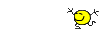
NONE!

I may have to add a 6th to my Holton for sh**ts and giggles. Remember that the 5th section on that tuba is separate from the removable piston section, so I could make a 5th/6th section that was completely separate from the current 5th section, so if I did not like it I could change it back with pretty much zero work. I could also just use it when I need it. (There are a number of pieces where such a thing could be very handy. Currently, I can remove the 5th valve if I do not need it, saving a bit of weight on my back and in my lap. (I was honestly surprised at how much of a difference this could make to my back over a couple of weeks of work.)
This special 5th/6th section could have the 6th lever integral to it so that there is no vestigial lever bracket as there is when I remove the 5th valve from the tuba. (In fact, I no longer remove the lever, but lock it down with a little tchotchke I made.)
So, now that the better mouthpiece is back in play and I have really gone over the tuba to work out fingerings and slide settings, in the range directly affected by the 6th valve, the above fingering system works, but the Ab became too low. 1245 is also too low. I ended up using 134, which is spot on. Of course, this will become a technical hurdle for a while as it is outside of my "pattern" but it works so well for me that it shouldn't be an obstacle for very long.
New World I and IV rock on this tuba. It is a lot more aggressive than the Mirafone in that register. I am not sure I want that, though, so after tonight I may opt for the mellower 186. If I draw attention to myself the conductor may remember that I am not supposed to be playing on the outer movements and then I'll have to do the whole "wait to play 14 notes and then wait for the piece to end" ordeal.
Oh, and the very flat E/Eb/D just below the staff is mysteriously in tune now. I did some work on the second slide in prep to cut the outer tubes. (i.e. I cut the inner tubes) and suddenly everything right there is great except that the Eb is still a hair under pitch.
I have no idea why this is, but it is real and not a placebo effect. I was not looking for this result AT ALL in this series of modifications. In fact, I was still lipping these notes up when I noticed that I was overdoing it. The tuner says they are where they need to be, more or less.
WTF?

Currently, it is a beautiful day in Yazoo City, Mississippi, despite the dreary overcast. Clouds will not be raining on this parade.
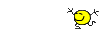
- These users thanked the author the elephant for the post (total 2):
- LeMark (Mon Feb 20, 2023 12:33 pm) • bloke (Mon Feb 20, 2023 12:45 pm)

- bloke
- Mid South Music
- Posts: 19367
- Joined: Thu Aug 13, 2020 8:55 am
- Location: western Tennessee - near Memphis
- Has thanked: 3857 times
- Been thanked: 4117 times
Re: Kurath/Willson F Tuba — Adding a 6th Valve
happy for you...
================================
Dvorak 9...
I always play everything that I play in the outer mvt's flawlessly.
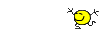
================================
Dvorak 9...
I always play everything that I play in the outer mvt's flawlessly.

one 'name' music director wrote:You know, there are some things that you can play on mvt's I and III..
me (unspoken) wrote:I've seen all sorts of tuba peeps' opinions on this - from the questionable-to-me to the ridiculous (such as 'most of the double bass part'), and - since friggin' John Rojak is covering the part - maybe (??) it will be covered just fine.
one 'name' music director wrote:nothing about me playing nothing in those mvt's.
- the elephant
- Posts: 3413
- Joined: Thu Aug 13, 2020 8:39 am
- Location: 404 - Not Found
- Has thanked: 1906 times
- Been thanked: 1346 times
Re: Kurath/Willson F Tuba — Adding a 6th Valve
I stated above that I wanted to remake the short arm and the two T hinge pieces because I ordered screws that have shoulders that are too short. Here is one of the original ones with a 5mm shoulder.

Here are the new screws with the two hinge tubes made. I had to drill them out, as you can see, and they needed to be about 6.75mm long as the shoulder of the new screws are 7mm long.



Here are the new screws with the two hinge tubes made. I had to drill them out, as you can see, and they needed to be about 6.75mm long as the shoulder of the new screws are 7mm long.


- These users thanked the author the elephant for the post:
- bloke (Tue Feb 28, 2023 6:58 pm)

- bloke
- Mid South Music
- Posts: 19367
- Joined: Thu Aug 13, 2020 8:55 am
- Location: western Tennessee - near Memphis
- Has thanked: 3857 times
- Been thanked: 4117 times
- the elephant
- Posts: 3413
- Joined: Thu Aug 13, 2020 8:39 am
- Location: 404 - Not Found
- Has thanked: 1906 times
- Been thanked: 1346 times
- bloke
- Mid South Music
- Posts: 19367
- Joined: Thu Aug 13, 2020 8:55 am
- Location: western Tennessee - near Memphis
- Has thanked: 3857 times
- Been thanked: 4117 times
Re: Kurath/Willson F Tuba — Adding a 6th Valve
Sorry, I can't remember the weird joke I was thinking of when I posted that. I was probably on LSD.
- These users thanked the author bloke for the post:
- the elephant (Sun Mar 12, 2023 4:21 pm)
- the elephant
- Posts: 3413
- Joined: Thu Aug 13, 2020 8:39 am
- Location: 404 - Not Found
- Has thanked: 1906 times
- Been thanked: 1346 times
Re: Kurath/Willson F Tuba — Adding a 6th Valve
I am still cramming for my soon-to-arrive burst of heavy, taxing, and important (to the organization) work. These gigs all need to be top-shelf, technically and musically, and there is a lot of difficult material that is not frequently in my Mississippi Musician's pabulum-infused diet of Pops music and light classics. Late March through the end of May is going to be a doozie this year…
With that being said, I am *still* working on these two long lever/linkage systems. Today took off the training wheels and deleted the right thumb lever and linkage that the upper 5th lever tied into. I made a one-piece rod to run between the lever and valve and nearly got the eyeballing of angles correct on the first try. It is good enough to leave in place until the summer. The 6th needs some adjusting, and I will look at that this week. The 5th is now at the height I want, too, so the difference between it and 6th is now ridiculous, but I can play it like that. I just hope this aspect is sorted out sooner than later.
A lot of work went into getting a thumb lever that would allow for the mechanics I prefer and still allow the linkage to reach downwards four inches to get a rod over to the valve. I made ten levers trying to sort out the various angles, offsets, and the like to get the perfect swing angle and throw length while moving my thrumb from the STUPID, PAINFUL location from the factory, which was so freaking terrible and heinous to use that he changed it for the later prototypes and the production horn. I have only seen the original setup on one other Kurath, another lacquered one with a lot of variation from the final horns. I had to build out a whole hand position from open space, then mate a lever up to that, and then to the valve, and it took forever because I wanted it to be absolutely right after spending all that time and money on getting it to work. I would get it working and would not like the action for whatever reason, and after all that I *needed* to be very happy, so I slogged away on that issue for what seemed to be an age. It was a real puzzler.
Also, this stuff was so complex and LONG, and it had to fit in and around different corners and tubes, so it could not be installed as a single-piece system, so my T hinges needed to be screwed together rather than the neat riveting done by factories on the T hinges in S arm systems. Since I have no machine tools, all my parts had to be above a certain size, and it all looks really chunky and heavy. It is. But it works so well, too, and I plan to use all that gear on an upcoming project… probably.
Then I decided to add a 6th valve because WHY T.F. NOT?
Now, all that time and work adds up to parts in a scrap box.
Sheesh.
Anyway, I no longer need nor want a thumb lever. I have crushed my thumbnail a few times with the lever bar when aggressively hitting 5th with the left index finger, and THAT CRAP HURTS LIKE HADES!!! Also, I can feel it beneath my thumb, so I sometimes forget and use it that way, and that screws up stuff for me with the 6th valve.
So it is all gone now, and it weighs a lot. The horn looks "cleaner" too.
All of this was deleted from the tuba.





With that being said, I am *still* working on these two long lever/linkage systems. Today took off the training wheels and deleted the right thumb lever and linkage that the upper 5th lever tied into. I made a one-piece rod to run between the lever and valve and nearly got the eyeballing of angles correct on the first try. It is good enough to leave in place until the summer. The 6th needs some adjusting, and I will look at that this week. The 5th is now at the height I want, too, so the difference between it and 6th is now ridiculous, but I can play it like that. I just hope this aspect is sorted out sooner than later.
A lot of work went into getting a thumb lever that would allow for the mechanics I prefer and still allow the linkage to reach downwards four inches to get a rod over to the valve. I made ten levers trying to sort out the various angles, offsets, and the like to get the perfect swing angle and throw length while moving my thrumb from the STUPID, PAINFUL location from the factory, which was so freaking terrible and heinous to use that he changed it for the later prototypes and the production horn. I have only seen the original setup on one other Kurath, another lacquered one with a lot of variation from the final horns. I had to build out a whole hand position from open space, then mate a lever up to that, and then to the valve, and it took forever because I wanted it to be absolutely right after spending all that time and money on getting it to work. I would get it working and would not like the action for whatever reason, and after all that I *needed* to be very happy, so I slogged away on that issue for what seemed to be an age. It was a real puzzler.
Also, this stuff was so complex and LONG, and it had to fit in and around different corners and tubes, so it could not be installed as a single-piece system, so my T hinges needed to be screwed together rather than the neat riveting done by factories on the T hinges in S arm systems. Since I have no machine tools, all my parts had to be above a certain size, and it all looks really chunky and heavy. It is. But it works so well, too, and I plan to use all that gear on an upcoming project… probably.
Then I decided to add a 6th valve because WHY T.F. NOT?
Now, all that time and work adds up to parts in a scrap box.
Sheesh.
Anyway, I no longer need nor want a thumb lever. I have crushed my thumbnail a few times with the lever bar when aggressively hitting 5th with the left index finger, and THAT CRAP HURTS LIKE HADES!!! Also, I can feel it beneath my thumb, so I sometimes forget and use it that way, and that screws up stuff for me with the 6th valve.
So it is all gone now, and it weighs a lot. The horn looks "cleaner" too.
All of this was deleted from the tuba.





- These users thanked the author the elephant for the post (total 2):
- bloke (Thu Mar 30, 2023 5:49 pm) • York-aholic (Thu Mar 30, 2023 11:44 pm)

- cjk
- Posts: 695
- Joined: Thu Aug 13, 2020 11:46 am
- Location: Atlanta, GA
- Has thanked: 265 times
- Been thanked: 147 times
Re: Kurath/Willson F Tuba — Adding a 6th Valve
Man I am super impressed that you have accomplished all this and doubly impressed that you did it all in your garage.the elephant wrote: ↑Sun Mar 12, 2023 4:21 pm ...
With that being said, I am *still* working on these two long lever/linkage systems. Today took off the training wheels and deleted the right thumb lever and linkage that the upper 5th lever tied into.
....


- the elephant
- Posts: 3413
- Joined: Thu Aug 13, 2020 8:39 am
- Location: 404 - Not Found
- Has thanked: 1906 times
- Been thanked: 1346 times
Re: Kurath/Willson F Tuba — Adding a 6th Valve
Actually, in my open-sided carport. Let me tell you about brazing with a strong wind blowing… oy…
And THANKS!

And THANKS!
- These users thanked the author the elephant for the post:
- cjk (Fri Mar 31, 2023 12:19 pm)

- the elephant
- Posts: 3413
- Joined: Thu Aug 13, 2020 8:39 am
- Location: 404 - Not Found
- Has thanked: 1906 times
- Been thanked: 1346 times
Re: Kurath/Willson F Tuba — Adding a 6th Valve
Playing Report:
Okay, so I recently performed a solo recital on this tuba, and am currently working up a brass quintet recital, so I have spent hundreds of hours with a tuner, metronome, drone pitch generator, and every mouthpiece I own, trying to find a "winning combination".
It seems to me that most well-designed tubas are pretty mouthpiece insensitive, whereas many are highly sensitive to changes in the bowl shape and depth. (I am speaking about intonation, rather than response issues.)
I have an idea that tubas that have the valve section placed in one of a few very advantageous "zones" along the taper are more stable, and that horns with valve machines located at the edge of one of these "zones" tend to be less stable in this regard. You can't just paste on a machine where the taper reaches the correct ID. There seems to be (again with that term) a "zone" or "zones" where you can safely have cylindrical tubing with little to no ill effects, A well-researched bugle will have these locations sniffed out, and the small-end wrap will be worked out so that the valves are squarely in the middle of one of these zones.
And most tubas have the valve machine within one of these zones, but some seem to have them right at the edge. If you move them an inch or two up or down suddenly the horn becomes "mouthpiece sensitive, when otherwise it would have been more stable. (I used to think that mouthpiece sensitivity was bunk, but all my messing with horns this past decade has made me think about this a lot more.)
So, with all this in mind, I suspect the original Kurath wrap (versus the later Willson wrap) was right at the edge of such a zone, and that he eventually dialed in the exact location (height?) of the valves and leadpipe through experimentation. And I may have uncovered this "trade secret" by doing all this work. The horn was about as dead to mouthpiece selection as you can get, but it was like a 2165 version of an F tuba: a little "hooty" and lacking in clarity.
The leadpipe I made (that properly met the 1st valve knuckle) had to be about an inch longer to end up in the same location at the receiver. This shifted the entire machine one inch farther down the taper once the MTS had been corrected to allow for the longer leadpipe. Add to that the fact that I installed one more valve and its "twisty" where it had earlier been straight tubing, and another shortening of the MTS to account for that added tubing, and now you have the end of the machine two full inches farther down the taper of the horn.
And now the tuba is extremely mouthpiece sensitive, more so than any other tuba I have played. I was worried that I had screwed something up, but I was wrong. I just had to find a mouthpiece type that it likes and then retune all the slides and "figure stuff out".
Now, with the fingerings that I had always used as alternates being used as the primary fingerings, and with the slides pulled appropriately, the LOW REGISTER response and intonation are far, far better than they have ever been. However, some things are now either not as good, or perhaps all this careful work has simply alerted me to stuff that I had been ignoring. (???)
My one issue seems to be 23 (sigh… it's always the 2-3 combo that is F'ed up) Db and Ab in the staff are very sharp. I can fix that, but then D and A played 3rd are then very flat, and as 12 they are very sharp. With six valves it is not easy to move the 1st slide (and no, using a trigger with my right thumb is 100% out of the question). I have to learn to work around these two notes. Also, low Gb is sharp as 23456, and 123456 is pretty much an F. Other than that, the horn is nicely evened out now.
I can play freely in the low register for the first time, ever. The low Bb had been very "low C-ish" as though a valve was halfway down. Now it has a more edgy tone but it is in tune and blows freely, so that alone is a boon to me. And now with the 6th valve replacing the 2nd the whole low range is very well in tune, which, of course, means that with the notes well centered it responds down there better, too.
Yesterday I spent two hours in the Snedecor book, and when I worked on the Malcolm Arnold "Quintet" everything was better in pitch and response and the new fingerings, while different, were much easier once I got used to them. I have become pretty adept at reading with six valves already. The transition was — for me — essentially effortless. Once I was past the initial slide setup and writing out of a fingering chart I never had to look back. I have definite, set fingerings for everything below the staff, with the pitch being stable enough that they work well in all 12 key centers. This is a great thing. The middle of the staff hovering around the sharp, open C is more of an issue. I have to play that C 13, but it is close enough that I can play it open in F or C major or A minor, but not in any other keys. The C# and G# are still problematic, but again, I will figure them out at some point.
I am amazed by how dead-on the sound and intonation of the Chaconne from the Arnold is now. And the "low-note-y" third movement is a lot easier and better, too.
I have decided to order a pair of custom-ported rotors from Miraphone that place the stems in better locations (to allow simpler/better linkage systems to be installed). I plan to build a new 56h/6th section that is detachable from the pistons because I have liked having that feature on my Holton. (It has been VERY handy.) Once that is done I can finally finish up this project by cleaning every joint to a high state and then lacquering the slides, buttons, caps, leadpipe, and bugle. I probably will NOT lacquer the piston section as I hate to have to burn up lacquer when I want to move something or take something apart. And the cheap lacquer I will be using will burn black when the flame hits it. If I ever set up to do epoxy lacquer and build a heating booth I might tackle the spaghetti of the machine, but until then — no way.)
I will be back with this thread once the final 5th/6th section has been built and the new linkages have been sorted. This will probably be in August.
Oh, and the winning mouthpiece?
Doug Elliott (1995)
R cup
R5E shank
4N 132 rim
I need to get either a Euro receiver or an R5 shank. But other than the thing only fitting in about 5/8" to 3/4" it does not wobble and it plays great. I just want to try a properly fitting shank to see what that does. (So as my ad says: WTB/WTT Doug Elliott old-style R5 Shank)

Okay, so I recently performed a solo recital on this tuba, and am currently working up a brass quintet recital, so I have spent hundreds of hours with a tuner, metronome, drone pitch generator, and every mouthpiece I own, trying to find a "winning combination".
It seems to me that most well-designed tubas are pretty mouthpiece insensitive, whereas many are highly sensitive to changes in the bowl shape and depth. (I am speaking about intonation, rather than response issues.)
I have an idea that tubas that have the valve section placed in one of a few very advantageous "zones" along the taper are more stable, and that horns with valve machines located at the edge of one of these "zones" tend to be less stable in this regard. You can't just paste on a machine where the taper reaches the correct ID. There seems to be (again with that term) a "zone" or "zones" where you can safely have cylindrical tubing with little to no ill effects, A well-researched bugle will have these locations sniffed out, and the small-end wrap will be worked out so that the valves are squarely in the middle of one of these zones.
And most tubas have the valve machine within one of these zones, but some seem to have them right at the edge. If you move them an inch or two up or down suddenly the horn becomes "mouthpiece sensitive, when otherwise it would have been more stable. (I used to think that mouthpiece sensitivity was bunk, but all my messing with horns this past decade has made me think about this a lot more.)
So, with all this in mind, I suspect the original Kurath wrap (versus the later Willson wrap) was right at the edge of such a zone, and that he eventually dialed in the exact location (height?) of the valves and leadpipe through experimentation. And I may have uncovered this "trade secret" by doing all this work. The horn was about as dead to mouthpiece selection as you can get, but it was like a 2165 version of an F tuba: a little "hooty" and lacking in clarity.
The leadpipe I made (that properly met the 1st valve knuckle) had to be about an inch longer to end up in the same location at the receiver. This shifted the entire machine one inch farther down the taper once the MTS had been corrected to allow for the longer leadpipe. Add to that the fact that I installed one more valve and its "twisty" where it had earlier been straight tubing, and another shortening of the MTS to account for that added tubing, and now you have the end of the machine two full inches farther down the taper of the horn.
And now the tuba is extremely mouthpiece sensitive, more so than any other tuba I have played. I was worried that I had screwed something up, but I was wrong. I just had to find a mouthpiece type that it likes and then retune all the slides and "figure stuff out".
Now, with the fingerings that I had always used as alternates being used as the primary fingerings, and with the slides pulled appropriately, the LOW REGISTER response and intonation are far, far better than they have ever been. However, some things are now either not as good, or perhaps all this careful work has simply alerted me to stuff that I had been ignoring. (???)
My one issue seems to be 23 (sigh… it's always the 2-3 combo that is F'ed up) Db and Ab in the staff are very sharp. I can fix that, but then D and A played 3rd are then very flat, and as 12 they are very sharp. With six valves it is not easy to move the 1st slide (and no, using a trigger with my right thumb is 100% out of the question). I have to learn to work around these two notes. Also, low Gb is sharp as 23456, and 123456 is pretty much an F. Other than that, the horn is nicely evened out now.
I can play freely in the low register for the first time, ever. The low Bb had been very "low C-ish" as though a valve was halfway down. Now it has a more edgy tone but it is in tune and blows freely, so that alone is a boon to me. And now with the 6th valve replacing the 2nd the whole low range is very well in tune, which, of course, means that with the notes well centered it responds down there better, too.
Yesterday I spent two hours in the Snedecor book, and when I worked on the Malcolm Arnold "Quintet" everything was better in pitch and response and the new fingerings, while different, were much easier once I got used to them. I have become pretty adept at reading with six valves already. The transition was — for me — essentially effortless. Once I was past the initial slide setup and writing out of a fingering chart I never had to look back. I have definite, set fingerings for everything below the staff, with the pitch being stable enough that they work well in all 12 key centers. This is a great thing. The middle of the staff hovering around the sharp, open C is more of an issue. I have to play that C 13, but it is close enough that I can play it open in F or C major or A minor, but not in any other keys. The C# and G# are still problematic, but again, I will figure them out at some point.
I am amazed by how dead-on the sound and intonation of the Chaconne from the Arnold is now. And the "low-note-y" third movement is a lot easier and better, too.
I have decided to order a pair of custom-ported rotors from Miraphone that place the stems in better locations (to allow simpler/better linkage systems to be installed). I plan to build a new 56h/6th section that is detachable from the pistons because I have liked having that feature on my Holton. (It has been VERY handy.) Once that is done I can finally finish up this project by cleaning every joint to a high state and then lacquering the slides, buttons, caps, leadpipe, and bugle. I probably will NOT lacquer the piston section as I hate to have to burn up lacquer when I want to move something or take something apart. And the cheap lacquer I will be using will burn black when the flame hits it. If I ever set up to do epoxy lacquer and build a heating booth I might tackle the spaghetti of the machine, but until then — no way.)
I will be back with this thread once the final 5th/6th section has been built and the new linkages have been sorted. This will probably be in August.
Oh, and the winning mouthpiece?
Doug Elliott (1995)
R cup
R5E shank
4N 132 rim
I need to get either a Euro receiver or an R5 shank. But other than the thing only fitting in about 5/8" to 3/4" it does not wobble and it plays great. I just want to try a properly fitting shank to see what that does. (So as my ad says: WTB/WTT Doug Elliott old-style R5 Shank)

