
The Great Kurath Re-Tubing
- the elephant
- Posts: 3775
- Joined: Thu Aug 13, 2020 8:39 am
- Location: Yazoo City, Mississippi (stop laughing!)
- Has thanked: 2186 times
- Been thanked: 1585 times
Re: The Great Kurath Re-Tubing
You nailed it. Phone camera. I keep thinking these things I see in the photos that I don't see IRL are "lens effects" and that I shouldn't worry about them. Yet I do…


- These users thanked the author the elephant for the post:
- bloke (Sat Dec 18, 2021 5:29 pm)

- matt g
- Posts: 2600
- Joined: Thu Aug 13, 2020 10:37 am
- Location: Southeastern New England
- Has thanked: 269 times
- Been thanked: 559 times
Re: The Great Kurath Re-Tubing
Most phone cameras lose the distortion when you are around “2x”.
Even something like a Canon 24-70mm F2.8L has a lot of distortion (fish eye effect) at 24mm focal length.
Even something like a Canon 24-70mm F2.8L has a lot of distortion (fish eye effect) at 24mm focal length.
Dillon/Walters CC (sold)
Meinl-Weston 2165 (sold)
Meinl-Weston 2165 (sold)
- bloke
- Mid South Music
- Posts: 20735
- Joined: Thu Aug 13, 2020 8:55 am
- Location: western Tennessee - near Memphis
- Has thanked: 4288 times
- Been thanked: 4548 times
Re: The Great Kurath Re-Tubing
(surely...??) Even our own eyes tend to do this...and certainly our spectacles contribute to this as well.
I measure stuff and do line-of-sight stuff (over-and-over-and-over) until I'm finally convinced that it's about as good as it can be.
bloke "Taking stuff back apart sucks...as I was trying to explain to Mrs. bloke, when I was installing that model 345 bottom bow, the other day."
I measure stuff and do line-of-sight stuff (over-and-over-and-over) until I'm finally convinced that it's about as good as it can be.
bloke "Taking stuff back apart sucks...as I was trying to explain to Mrs. bloke, when I was installing that model 345 bottom bow, the other day."
- the elephant
- Posts: 3775
- Joined: Thu Aug 13, 2020 8:39 am
- Location: Yazoo City, Mississippi (stop laughing!)
- Has thanked: 2186 times
- Been thanked: 1585 times
- the elephant
- Posts: 3775
- Joined: Thu Aug 13, 2020 8:39 am
- Location: Yazoo City, Mississippi (stop laughing!)
- Has thanked: 2186 times
- Been thanked: 1585 times
Re: The Great Kurath Re-Tubing
Tested! I used a tuner, three different mouthpieces, and played scales and arpeggios in all major and forms of the minor keys, along with two short vocalises that I have written out in all 12 keys, so having to play an out of tune note that is acceptable in one key will still stick out like a sore thumb in another one.
I tried to make sure I was not suffering from New Mouthpiece Syndrome and chomping on a whole lot of placebo effect by doing it this way. I won't know for sure what I think of all this until my Wednesday rehearsal where I have to use this horn (and the three masses I have on Christmas Eve).
However, I will say, with these qualifications*, that this tuba plays better in all ways. Everything feels *even* now. I can play Bydlo with no slide pulls and only one alternate, which is a pretty normal one for an F tuba. In fact, I can now play the horn from top to bottom with only in-the-staff and above-the-staff D played 3, in-the-staff C lipped down a very small bit, and below-the-staff Gb/F# played all five down, which is flat. (1345 is sharp. This is why we have a 6th valve, kiddies. I wouldn't mind having one on this tuba.)
The alterations to the MTS crooks, which were really worrying me, ended up opening up the low end a little, doing nothing response-wise to the rest of the horn, and perhaps sealed up some leaks so that pitch is better. There were FACTORY leaks in four places that I have found, thus far, which I find to be disappointing, but there have been a number of disappointing finds during this project. The horn still played very well as it was. It plays in a way that makes me smile, now, though.
I only reassembled it. None of the five or six removed braces have been reinstalled yet. None of the cleanup work has even been started. I will do all that on Monday and Tuesday. Today was when I had planned on doing this, but once I started testing the horn I just sat down and played for three hours. (I have two gigs tonight, so that may have been a "D'OH! Moment" on my part, but whatever.)
I was stoked the most by one particular piece that plays nicely in tune with a lot of clarity now, for the first time ever for me on any F tuba: Prokofiev Symphony 5. This tuba could probably actually do this in performance. I would have to work my behind off on air, but the horn now plays that well in tune down there with a much more even use of air. (ie - the resistance is a bit less in some areas and a bit more in others, so it has an evenness from top to bottom that I have only experienced on my current 186.)
It is not a miracle horn by any means, but it sure pleases me to no end! I have it so torn apart, brace-wise, that I will likely do both 4th slides on Monday, too.
What a happy surprise this project dumped in my lap. I just wanted to seal the horn up better and get some sexy nickel silver on it. And BOOM!
Nice!
_________
* Read: "excuses to bail out and change my story"

I tried to make sure I was not suffering from New Mouthpiece Syndrome and chomping on a whole lot of placebo effect by doing it this way. I won't know for sure what I think of all this until my Wednesday rehearsal where I have to use this horn (and the three masses I have on Christmas Eve).
However, I will say, with these qualifications*, that this tuba plays better in all ways. Everything feels *even* now. I can play Bydlo with no slide pulls and only one alternate, which is a pretty normal one for an F tuba. In fact, I can now play the horn from top to bottom with only in-the-staff and above-the-staff D played 3, in-the-staff C lipped down a very small bit, and below-the-staff Gb/F# played all five down, which is flat. (1345 is sharp. This is why we have a 6th valve, kiddies. I wouldn't mind having one on this tuba.)
The alterations to the MTS crooks, which were really worrying me, ended up opening up the low end a little, doing nothing response-wise to the rest of the horn, and perhaps sealed up some leaks so that pitch is better. There were FACTORY leaks in four places that I have found, thus far, which I find to be disappointing, but there have been a number of disappointing finds during this project. The horn still played very well as it was. It plays in a way that makes me smile, now, though.
I only reassembled it. None of the five or six removed braces have been reinstalled yet. None of the cleanup work has even been started. I will do all that on Monday and Tuesday. Today was when I had planned on doing this, but once I started testing the horn I just sat down and played for three hours. (I have two gigs tonight, so that may have been a "D'OH! Moment" on my part, but whatever.)
I was stoked the most by one particular piece that plays nicely in tune with a lot of clarity now, for the first time ever for me on any F tuba: Prokofiev Symphony 5. This tuba could probably actually do this in performance. I would have to work my behind off on air, but the horn now plays that well in tune down there with a much more even use of air. (ie - the resistance is a bit less in some areas and a bit more in others, so it has an evenness from top to bottom that I have only experienced on my current 186.)
It is not a miracle horn by any means, but it sure pleases me to no end! I have it so torn apart, brace-wise, that I will likely do both 4th slides on Monday, too.
What a happy surprise this project dumped in my lap. I just wanted to seal the horn up better and get some sexy nickel silver on it. And BOOM!
Nice!
_________
* Read: "excuses to bail out and change my story"

- These users thanked the author the elephant for the post (total 2):
- bloke (Sun Dec 19, 2021 4:21 pm) • prairieboy1 (Sun Dec 19, 2021 11:20 pm)

- the elephant
- Posts: 3775
- Joined: Thu Aug 13, 2020 8:39 am
- Location: Yazoo City, Mississippi (stop laughing!)
- Has thanked: 2186 times
- Been thanked: 1585 times
Re: The Great Kurath Re-Tubing
Now, place your bets on how long the New Mouthpiece Syndrome lasts. I tried very hard to sidestep the reality of NMS, just playing as I always play (faults and all) but this tuba just plays mo bettah.
So how long until things revert to their everyday mediocrity?
$50 ante, $50 minimum
Ready? Go!
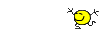
So how long until things revert to their everyday mediocrity?
$50 ante, $50 minimum

Ready? Go!
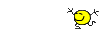

- the elephant
- Posts: 3775
- Joined: Thu Aug 13, 2020 8:39 am
- Location: Yazoo City, Mississippi (stop laughing!)
- Has thanked: 2186 times
- Been thanked: 1585 times
Re: The Great Kurath Re-Tubing
This post is a lot of blather about various detachable braces and my experience with them over time. No, really, that is all it is about. If you don't have an interest in them you can skip this and still live a full and satisfying life.
I made this valve section removable in the clever manner of my old Kalison Daryl Smith CC from back in the early 1990s. I loved that feature for several reasons, and when I first noticed the "new" King 2341 shared it I started compiling parts numbers, I took some photos, and I started scheming on how I could do this to my Holton 345.
I decided that the design of my Kurath was *much* simpler and cleaner, lending itself to this conversion pretty nicely. It also was dealing with a lot less weight, so it seemed to be safer, too. I was always worried that the very heavy 345 would snap detachable braces and I would have this dramatic scene on stage during the solo from "An American in Paris" where the valve section just fell off my horn in mid-phrase. (Ah, the imagery of that thought…)
I remembered the Daryl Smith having some rather thin, "dainty" braces that always worried me. I was told by a tech that these were a major weak point in the design and that if I did not need removable valves that I probably should have those braces replaced with heavier, fixed ones. I did not like that idea at all. (That was sometime in 1995.)
So I decided a few years ago to do this to the Kurath because one of our posters here was building a removable 5th valve for his tuba using the Conn-Selmer braces and leadpipe/5th valve three-piece "unions" that looked so nice.
I got him to give me all the part numbers and that started the whole mess. I got some in the mail and immediately disliked them because the weight of the valve section was hanging on by a ridiculously thin nub of yellow brass. The posts were big and thick and impressive, but the actual screw attachment parts were silver soldered to them via very small contact patches; *very* small. These made me nervous just looking at them.
I ended up using detachable braces from four makers on the Kurath and the Holton. Long story short, I greatly prefer the Instrument Innovations large brace sockets, but they are just too big to not look strange on the F tuba. My next choice is the brace made by Edwards. It is just like the smaller of the two from Instrument Innovations, but (unfortunately) is all brass, no nickel silver. However, the rod stock used is beefier than that used on the almost identical I.I. brace, and, importantly, the stop ring on the rod is a stronger design, IMHO.
None of the two I.I. braces or the Edwards brace have ever come loose, and none of them have ever gotten stuck so that I could not use my fingers to unscrew them.
The last maker was Yamaha. I have used several of their sousaphone braces, but all have needed to be altered to work the way I want them to. They fulfill a special need, which is to bind two tubes that are about 1/4" to 5/16" apart. NONE of the other braces can do this. They all need to be a certain minimum length, and none of them are of much use between two tubes that are close together.
Each brace used a different method to undo them. The Yamaha has a JIS Phillips head, the King uses an Allen key. The ones from Instrument Innovations and Edwards were knurled "barrel" braces for trombones — no tools needed.
After about six months of playing the Kurath with the detachable braces on it, I found a small flaw in my design. When I built the Holton out, I fixed this. The Holton is *very* well braced up, and I feel it is every bit as strong and stable as one with fixed braces.
Now I am doing a lot to the Kurath again, and it is like with a car. If you change the timing belt you usually change the water pump and thermostat, too, because of the old adage of "While you're in there you might as well do everything else…" So "while I'm in there," I have decided to work out a lot of small things. The big one (for me) is to make all seven existing breakpoints use braces that need no tools to undo. I have three connection points in the leadpipe, as well, and two are already like this, so I need to take care of the one that requires an Allen key. I am also adding a brace, and it, too, will be a trombone "thumb screw" type.
Unlike Joe, I *do* take some tools with me to gigs. I have had to repair instruments at gig sites many times over the years, and I once had a fender bender in the parking lot of a gig site that was over a hundred miles from my tools, and my first valve started hanging because the slide was bent just a bit. I could deal with the slide not working, but I could not play because of the first valve. I was parked, and the horn was out of the bag and resting on the rear seat of my car on top of the bag so that I could do some warming up away from the others. (I carry a folding chair and a stand with me everywhere.) Some damnable child piloting a large car from the early 1970s decided to do donuts in the mostly empty parking lot, and the moron clipped my car and tossed my tuba onto the floor, rendering it unplayable.
My foreman in the shop at the music store was also our 2nd oboist, and he carried a mobile repair shop in his van. Because of that, I was able to fire up an acetylene torch and unbind my 1st valve on the spot, and I was also able to repair the slide so that on stage you could not tell anything had happened. And the moron kid basically bought me another car in the process.
This experience has taught me to carry every tool needed to remove every screw on a horn, to carry replacement water key corks… even valve springs. (In 1994 I was at an MSO rehearsal and one of the steel (yes, steel) wire piston springs snapped in half on me and I lost my 3rd valve. Rehearsal happened to be on a Saturday morning, and the shop was about ten miles away, so I drove over and picked up a set of four new Allied springs and swapped the whole set out in my seat in the orchestra.
I will *always* carry certain tools with me, either in my car or in the gig bag.
So, my idea of making every breakpoint in the horn's valve section and leadpipe finger-removable started to look attractive as I was tired of having the JIS screwdriver, the Torx drive for the Minibal screws, and the Allen T wrench in my Mirapphone bags that have little to no storage space.
The Holton taught me just how short I could make the Edwards brace, and I realized the Kurath *could* have only thumb screw-type braces.
I bought four more, as well as the parts to make a fixed brace using the same parts. The MTS has a Kurath brace on the ferrules and an Edwards brace on the outer tubes, as well as an Edwards brace between the small side and the bottom bow, so I wanted the MTS brace to match.
If anyone wants to give one of these a try, here are the part numbers (and the current prices, which *will* go up every quarter)…
G-12736-0 — Brace Post Rod — $15
G-12704-0 — Threaded Flange — $5.60
G-12702-0 — Small Threaded Nut — $8.75
G-12700-0 — Stop Ring — $3.50
G-05800-0 — Brace Post — $7.75

Also, regarding the Yamaha sousaphone brace and its JIS screw, it has the infamous dot on the head, which means is shaped to accept the tip of a Japanese Industrial Standard screwdriver. A Phillips head is designed to cam out under enough torque. The JIS does not, so if you use a Phillips head on a very tightly installed JIS screw you will strip out the cross in the screw.
I hate these. I cannot find a JIS screwdriver of the right size head and length to be of any use to me. I have a German WiHa screwdriver that fits JIS pretty well, but it is really long, so not a good gig bag choice.
Early on I decided that I would replace this screw with hex head cap bolts that use the same Allen key as the King braces. I picked up some along with the correct clearance drill bit and a through-hole tap from McMaster-Carr for cheap and set about to modify all of these braces that I have in my parts bins. I am glad I did this, too.
However, now that I am trying to remove tools from the equation this no longer works.
Back to McMaster-Carr for some searcing and clicking through all the various filters, and I found this:

The original brace was like M3.5x1 or some such, and the new hardware used 5-44 threads. This new, long, knurled thumb screw uses 8-32 threads and these braces parts are just big enough to accept both the thread size and the width of the shoulder of the screw. This brace goes between two small tubes that are very close together, so getting your fingers in there to remove it is impossible unless you have clever, little raccoon hands. And I don't.
So this screw has a 3/16" long 8-32 threaded part, with a 1" long shoulder. It is a good grade of stainless, so it should not corrode against the brass over time, unlike mild steel. It will stick out far enough with a head that is fat enough for me to install or remove without too much of a fuss.

So as far as detachable braces go, Bubba Blue said it best…
Anyway, like I was sayin', shrimp is the fruit of the sea. You can barbecue it, boil it, broil it, bake it, saute it. There's, uh, shrimp kabobs, shrimp creole, shrimp gumbo, pan-fried, deep-fried, stir-fried, there's pineapple shrimp, lemon shrimp, coconut shrimp, pepper shrimp, shrimp soup, shrimp stew, shrimp salad, shrimp and potatoes, shrimp burger, shrimp sandwich. That — that's about it.

I made this valve section removable in the clever manner of my old Kalison Daryl Smith CC from back in the early 1990s. I loved that feature for several reasons, and when I first noticed the "new" King 2341 shared it I started compiling parts numbers, I took some photos, and I started scheming on how I could do this to my Holton 345.
I decided that the design of my Kurath was *much* simpler and cleaner, lending itself to this conversion pretty nicely. It also was dealing with a lot less weight, so it seemed to be safer, too. I was always worried that the very heavy 345 would snap detachable braces and I would have this dramatic scene on stage during the solo from "An American in Paris" where the valve section just fell off my horn in mid-phrase. (Ah, the imagery of that thought…)
I remembered the Daryl Smith having some rather thin, "dainty" braces that always worried me. I was told by a tech that these were a major weak point in the design and that if I did not need removable valves that I probably should have those braces replaced with heavier, fixed ones. I did not like that idea at all. (That was sometime in 1995.)
So I decided a few years ago to do this to the Kurath because one of our posters here was building a removable 5th valve for his tuba using the Conn-Selmer braces and leadpipe/5th valve three-piece "unions" that looked so nice.
I got him to give me all the part numbers and that started the whole mess. I got some in the mail and immediately disliked them because the weight of the valve section was hanging on by a ridiculously thin nub of yellow brass. The posts were big and thick and impressive, but the actual screw attachment parts were silver soldered to them via very small contact patches; *very* small. These made me nervous just looking at them.
I ended up using detachable braces from four makers on the Kurath and the Holton. Long story short, I greatly prefer the Instrument Innovations large brace sockets, but they are just too big to not look strange on the F tuba. My next choice is the brace made by Edwards. It is just like the smaller of the two from Instrument Innovations, but (unfortunately) is all brass, no nickel silver. However, the rod stock used is beefier than that used on the almost identical I.I. brace, and, importantly, the stop ring on the rod is a stronger design, IMHO.
None of the two I.I. braces or the Edwards brace have ever come loose, and none of them have ever gotten stuck so that I could not use my fingers to unscrew them.
The last maker was Yamaha. I have used several of their sousaphone braces, but all have needed to be altered to work the way I want them to. They fulfill a special need, which is to bind two tubes that are about 1/4" to 5/16" apart. NONE of the other braces can do this. They all need to be a certain minimum length, and none of them are of much use between two tubes that are close together.
Each brace used a different method to undo them. The Yamaha has a JIS Phillips head, the King uses an Allen key. The ones from Instrument Innovations and Edwards were knurled "barrel" braces for trombones — no tools needed.
After about six months of playing the Kurath with the detachable braces on it, I found a small flaw in my design. When I built the Holton out, I fixed this. The Holton is *very* well braced up, and I feel it is every bit as strong and stable as one with fixed braces.
Now I am doing a lot to the Kurath again, and it is like with a car. If you change the timing belt you usually change the water pump and thermostat, too, because of the old adage of "While you're in there you might as well do everything else…" So "while I'm in there," I have decided to work out a lot of small things. The big one (for me) is to make all seven existing breakpoints use braces that need no tools to undo. I have three connection points in the leadpipe, as well, and two are already like this, so I need to take care of the one that requires an Allen key. I am also adding a brace, and it, too, will be a trombone "thumb screw" type.
Unlike Joe, I *do* take some tools with me to gigs. I have had to repair instruments at gig sites many times over the years, and I once had a fender bender in the parking lot of a gig site that was over a hundred miles from my tools, and my first valve started hanging because the slide was bent just a bit. I could deal with the slide not working, but I could not play because of the first valve. I was parked, and the horn was out of the bag and resting on the rear seat of my car on top of the bag so that I could do some warming up away from the others. (I carry a folding chair and a stand with me everywhere.) Some damnable child piloting a large car from the early 1970s decided to do donuts in the mostly empty parking lot, and the moron clipped my car and tossed my tuba onto the floor, rendering it unplayable.
My foreman in the shop at the music store was also our 2nd oboist, and he carried a mobile repair shop in his van. Because of that, I was able to fire up an acetylene torch and unbind my 1st valve on the spot, and I was also able to repair the slide so that on stage you could not tell anything had happened. And the moron kid basically bought me another car in the process.
This experience has taught me to carry every tool needed to remove every screw on a horn, to carry replacement water key corks… even valve springs. (In 1994 I was at an MSO rehearsal and one of the steel (yes, steel) wire piston springs snapped in half on me and I lost my 3rd valve. Rehearsal happened to be on a Saturday morning, and the shop was about ten miles away, so I drove over and picked up a set of four new Allied springs and swapped the whole set out in my seat in the orchestra.
I will *always* carry certain tools with me, either in my car or in the gig bag.
So, my idea of making every breakpoint in the horn's valve section and leadpipe finger-removable started to look attractive as I was tired of having the JIS screwdriver, the Torx drive for the Minibal screws, and the Allen T wrench in my Mirapphone bags that have little to no storage space.
The Holton taught me just how short I could make the Edwards brace, and I realized the Kurath *could* have only thumb screw-type braces.
I bought four more, as well as the parts to make a fixed brace using the same parts. The MTS has a Kurath brace on the ferrules and an Edwards brace on the outer tubes, as well as an Edwards brace between the small side and the bottom bow, so I wanted the MTS brace to match.
If anyone wants to give one of these a try, here are the part numbers (and the current prices, which *will* go up every quarter)…
G-12736-0 — Brace Post Rod — $15
G-12704-0 — Threaded Flange — $5.60
G-12702-0 — Small Threaded Nut — $8.75
G-12700-0 — Stop Ring — $3.50
G-05800-0 — Brace Post — $7.75

Also, regarding the Yamaha sousaphone brace and its JIS screw, it has the infamous dot on the head, which means is shaped to accept the tip of a Japanese Industrial Standard screwdriver. A Phillips head is designed to cam out under enough torque. The JIS does not, so if you use a Phillips head on a very tightly installed JIS screw you will strip out the cross in the screw.
I hate these. I cannot find a JIS screwdriver of the right size head and length to be of any use to me. I have a German WiHa screwdriver that fits JIS pretty well, but it is really long, so not a good gig bag choice.
Early on I decided that I would replace this screw with hex head cap bolts that use the same Allen key as the King braces. I picked up some along with the correct clearance drill bit and a through-hole tap from McMaster-Carr for cheap and set about to modify all of these braces that I have in my parts bins. I am glad I did this, too.
However, now that I am trying to remove tools from the equation this no longer works.
Back to McMaster-Carr for some searcing and clicking through all the various filters, and I found this:

The original brace was like M3.5x1 or some such, and the new hardware used 5-44 threads. This new, long, knurled thumb screw uses 8-32 threads and these braces parts are just big enough to accept both the thread size and the width of the shoulder of the screw. This brace goes between two small tubes that are very close together, so getting your fingers in there to remove it is impossible unless you have clever, little raccoon hands. And I don't.
So this screw has a 3/16" long 8-32 threaded part, with a 1" long shoulder. It is a good grade of stainless, so it should not corrode against the brass over time, unlike mild steel. It will stick out far enough with a head that is fat enough for me to install or remove without too much of a fuss.

So as far as detachable braces go, Bubba Blue said it best…
Anyway, like I was sayin', shrimp is the fruit of the sea. You can barbecue it, boil it, broil it, bake it, saute it. There's, uh, shrimp kabobs, shrimp creole, shrimp gumbo, pan-fried, deep-fried, stir-fried, there's pineapple shrimp, lemon shrimp, coconut shrimp, pepper shrimp, shrimp soup, shrimp stew, shrimp salad, shrimp and potatoes, shrimp burger, shrimp sandwich. That — that's about it.

- the elephant
- Posts: 3775
- Joined: Thu Aug 13, 2020 8:39 am
- Location: Yazoo City, Mississippi (stop laughing!)
- Has thanked: 2186 times
- Been thanked: 1585 times
Re: The Great Kurath Re-Tubing
So I have the Edwards braces already on the horn where the 1st slide breaks from the bell, the small side of the MTS breaks from the bottom bow, and between the two outer MTS tubes.
I have two King braces between the 4th loop and the bugle on the top bow side away from the bell. I have two more between the bell and the other 4th slide.
I have the Yamaha brace between the big "hoop" of the 4th loop and the top bow where they used to be soldered directly together with no brace between them. I had to mangle the hoop a little on both ends to make enough space for a brace at this location. The inch-long thumb screw I just bought will work in that very tight and awkward space quite well.
Of course, when I redesign the 4th loop the two King braces between the inner 4th slide and the bell as well as this Yamaha brace will no longer have a home. I might need these parts in my new design, but I don't really know, yet.
Since it may be another year before I get around to redoing the 4th slide I decided to buy the needed hardware to get what I have up to snuff.
NOW insert the Bubba Blue quote…
I have two King braces between the 4th loop and the bugle on the top bow side away from the bell. I have two more between the bell and the other 4th slide.
I have the Yamaha brace between the big "hoop" of the 4th loop and the top bow where they used to be soldered directly together with no brace between them. I had to mangle the hoop a little on both ends to make enough space for a brace at this location. The inch-long thumb screw I just bought will work in that very tight and awkward space quite well.
Of course, when I redesign the 4th loop the two King braces between the inner 4th slide and the bell as well as this Yamaha brace will no longer have a home. I might need these parts in my new design, but I don't really know, yet.
Since it may be another year before I get around to redoing the 4th slide I decided to buy the needed hardware to get what I have up to snuff.
NOW insert the Bubba Blue quote…

- bloke
- Mid South Music
- Posts: 20735
- Joined: Thu Aug 13, 2020 8:55 am
- Location: western Tennessee - near Memphis
- Has thanked: 4288 times
- Been thanked: 4548 times
Re: The Great Kurath Re-Tubing
More than once or twice...
I've had people bring me boutique-label trombones (which feature braces such as that) whereby - when they tighten that detachable brace's nut enough to not rattle nor buzz, that tuning slide binds (and/or if a traditional rotor - as traditional rotor tolerances are considerably closer than the tolerances allowed on most trombones' gimmick valves - even the instrument's rotor catches). This has nothing to do with the brace being detachable, but only has to do with the person that installed the brace; it has to do with not allowing for the contraction that always occurs when a soldered brace cools. (Complicating the repair-shop correction of this situation, manufacturers tend to install this long brace first, and then attach other fixed/non-adjustable braces later - which works against simply heating the socket and letting out more brace rod...and - even when this can be accomplished - it can easily - then - mess up the alignment of other tuning slides, such as a trombone's main slide.) Of course, the same thing occurs when installing any traditional brace, any inside slide assembly, or when reassembling a trombone playing slide - after lathe-straightening the tubes. With me using bad grammar, Wade knows that this must be "allowed for".
Going off on a further tangent/analogy (IN SOMEONE'S ELSE THREAD, NO LESS
)
...The reason that most Acura and Lexus cars are pretty good is because most Honda and Toyota cars are pretty good. If a maker's standard line isn't particularly good, their luxury/boutique line may well be fancy, but might not actually be good.
To this point, it seems to me that - with a picky consumer - it would require a tremendous amount of confidence (confidence in a manufacturer/fabricator) to order a factory silver plated instrument.
I've had people bring me boutique-label trombones (which feature braces such as that) whereby - when they tighten that detachable brace's nut enough to not rattle nor buzz, that tuning slide binds (and/or if a traditional rotor - as traditional rotor tolerances are considerably closer than the tolerances allowed on most trombones' gimmick valves - even the instrument's rotor catches). This has nothing to do with the brace being detachable, but only has to do with the person that installed the brace; it has to do with not allowing for the contraction that always occurs when a soldered brace cools. (Complicating the repair-shop correction of this situation, manufacturers tend to install this long brace first, and then attach other fixed/non-adjustable braces later - which works against simply heating the socket and letting out more brace rod...and - even when this can be accomplished - it can easily - then - mess up the alignment of other tuning slides, such as a trombone's main slide.) Of course, the same thing occurs when installing any traditional brace, any inside slide assembly, or when reassembling a trombone playing slide - after lathe-straightening the tubes. With me using bad grammar, Wade knows that this must be "allowed for".
Going off on a further tangent/analogy (IN SOMEONE'S ELSE THREAD, NO LESS

...The reason that most Acura and Lexus cars are pretty good is because most Honda and Toyota cars are pretty good. If a maker's standard line isn't particularly good, their luxury/boutique line may well be fancy, but might not actually be good.
To this point, it seems to me that - with a picky consumer - it would require a tremendous amount of confidence (confidence in a manufacturer/fabricator) to order a factory silver plated instrument.
- the elephant
- Posts: 3775
- Joined: Thu Aug 13, 2020 8:39 am
- Location: Yazoo City, Mississippi (stop laughing!)
- Has thanked: 2186 times
- Been thanked: 1585 times
Re: The Great Kurath Re-Tubing
Yep. You always need to go back and tighten the nut down very tightly to eat up 100% of the gap, then heat the post from the other end to allow it to pop back out. These work really well and I have never had the issues with them that they frequently seem to have. I have fixed about a dozen of these on the trombones of friends and colleagues over the years.
If the rod end/stop ring do not fit this well when it is room temperature then you will have binding issues. (I did go back and refit that brace foot to the branch face. My photos are for me. They are what I use to look over my work, and most never get shared. I just share any that came out nicely or show something I think might be of interest. Most get deleted after about 24 hours.)

If the rod end/stop ring do not fit this well when it is room temperature then you will have binding issues. (I did go back and refit that brace foot to the branch face. My photos are for me. They are what I use to look over my work, and most never get shared. I just share any that came out nicely or show something I think might be of interest. Most get deleted after about 24 hours.)

- These users thanked the author the elephant for the post:
- bloke (Tue Dec 21, 2021 1:45 pm)

- Tubajug
- Posts: 779
- Joined: Thu Aug 13, 2020 10:27 am
- Location: Nebraska
- Has thanked: 236 times
- Been thanked: 219 times
Re: The Great Kurath Re-Tubing
I like that they have the little stop ring, rather than the little "hockey puck" thing they had before. That was tricky for someone like me (without a lot of experience in this stuff or a way to really hold it in place while soldering) to get soldered on correctly. Luckily I somehow got it on my first try! Whew!
Great info here @the elephant !
Great info here @the elephant !
- These users thanked the author Tubajug for the post:
- the elephant (Tue Dec 21, 2021 3:02 pm)
Jordan
King 2341 with Holton Monster Eb Bell
King/Conn Eb Frankentuba
Pan AmeriConn BBb Helicon
Yamaha YBB-103
"No one else is placed exactly as we are in our opportune human orbits."
King 2341 with Holton Monster Eb Bell
King/Conn Eb Frankentuba
Pan AmeriConn BBb Helicon
Yamaha YBB-103
"No one else is placed exactly as we are in our opportune human orbits."
- the elephant
- Posts: 3775
- Joined: Thu Aug 13, 2020 8:39 am
- Location: Yazoo City, Mississippi (stop laughing!)
- Has thanked: 2186 times
- Been thanked: 1585 times
Re: The Great Kurath Re-Tubing
@Tubajug, the Instrument Innovations braces have that, and the Edwards braces do not. The Edwards braces also use a fatter post, which is nice. And I agree: this is the superior of the two designs.
_________________________
The above two posts that ramble on endlessly about braces were prompted by my having ordered some additional parts from that nice Lexi at Edwards. Yeah, I blathered on so long that I forgot to mention part of the reason for posting.
<sorry>
I have been looking at the MTS. I had not intended to "over brace" that part. I dislike the way two braces close together look. Only wide-span slides need to have a brace to preserve the alignment. On this tuba (and my Holton) the breakpoint between the bugle and the machine is at the MTS. So one leg lives on each half of the horn. I am not using the huge braces on this that I used on the Holton. It might be something I try in the future, but not right now.
Anyway, this tuba was knocked over on a tile floor at a gig about a year ago. There was absolutely no damage at all. IT IS A VERY HEAVY F TUBA. However, the MTS alignment suffered a little bit, and a little bit can cause the slide to not work all that well. Since this was pretty badly worn (and why I was replacing all this tubing) I just left it alone and kept it greased. I am hoping the addition of a brace that connects the two MTS outer tubes directly to each other will prevent this in the future.
So now we are back in the realm of the super-nitpicky. I am sad to have to use the ugly, bent up, weak Kurath braces, but the King alternatives were not good. Perhaps I will order up 50 or 60 of the new braces (to have a lot in stock so this sort of nonsense doesn't catch me up again) with the round feet and start over, replacing all of my beloved diamond-footed braces with these. Until then, I am reusing most of the Kurath braces. I tried to alter them so they at least matched themselves. (They are amazingly inconsistent in height, and the sockets are not centered on the flanges about half the time — craptacular and disappointing all at once.
So I have this Kurath brace on the MTS and now I have this Edwards brace. They are right next to one another and are obviously not from the same maker. It looks very nice — but homemade — to me. So I ordered up two of the brace feet from this "kit" so I could install a new MTS brace that matches the detachable brace between the outer tubes. This is the sort of thing that allows me to sleep for a few hours at night when all sorts of stress and other things keep me awake.
The lower brace in this pic will be replaced with one that has the fixed end foot on both ends, using the same rod stock. The only difference is the threaded barrel on the one side of the detachable one. I hope this makes the detachable brace look less odd.

_________________________
The above two posts that ramble on endlessly about braces were prompted by my having ordered some additional parts from that nice Lexi at Edwards. Yeah, I blathered on so long that I forgot to mention part of the reason for posting.
<sorry>
I have been looking at the MTS. I had not intended to "over brace" that part. I dislike the way two braces close together look. Only wide-span slides need to have a brace to preserve the alignment. On this tuba (and my Holton) the breakpoint between the bugle and the machine is at the MTS. So one leg lives on each half of the horn. I am not using the huge braces on this that I used on the Holton. It might be something I try in the future, but not right now.
Anyway, this tuba was knocked over on a tile floor at a gig about a year ago. There was absolutely no damage at all. IT IS A VERY HEAVY F TUBA. However, the MTS alignment suffered a little bit, and a little bit can cause the slide to not work all that well. Since this was pretty badly worn (and why I was replacing all this tubing) I just left it alone and kept it greased. I am hoping the addition of a brace that connects the two MTS outer tubes directly to each other will prevent this in the future.
So now we are back in the realm of the super-nitpicky. I am sad to have to use the ugly, bent up, weak Kurath braces, but the King alternatives were not good. Perhaps I will order up 50 or 60 of the new braces (to have a lot in stock so this sort of nonsense doesn't catch me up again) with the round feet and start over, replacing all of my beloved diamond-footed braces with these. Until then, I am reusing most of the Kurath braces. I tried to alter them so they at least matched themselves. (They are amazingly inconsistent in height, and the sockets are not centered on the flanges about half the time — craptacular and disappointing all at once.
So I have this Kurath brace on the MTS and now I have this Edwards brace. They are right next to one another and are obviously not from the same maker. It looks very nice — but homemade — to me. So I ordered up two of the brace feet from this "kit" so I could install a new MTS brace that matches the detachable brace between the outer tubes. This is the sort of thing that allows me to sleep for a few hours at night when all sorts of stress and other things keep me awake.
The lower brace in this pic will be replaced with one that has the fixed end foot on both ends, using the same rod stock. The only difference is the threaded barrel on the one side of the detachable one. I hope this makes the detachable brace look less odd.


- Tubajug
- Posts: 779
- Joined: Thu Aug 13, 2020 10:27 am
- Location: Nebraska
- Has thanked: 236 times
- Been thanked: 219 times
Re: The Great Kurath Re-Tubing
Ah, ok. I missed that they were different companies. Do you still silver solder the stop ring to the post?
Jordan
King 2341 with Holton Monster Eb Bell
King/Conn Eb Frankentuba
Pan AmeriConn BBb Helicon
Yamaha YBB-103
"No one else is placed exactly as we are in our opportune human orbits."
King 2341 with Holton Monster Eb Bell
King/Conn Eb Frankentuba
Pan AmeriConn BBb Helicon
Yamaha YBB-103
"No one else is placed exactly as we are in our opportune human orbits."
- the elephant
- Posts: 3775
- Joined: Thu Aug 13, 2020 8:39 am
- Location: Yazoo City, Mississippi (stop laughing!)
- Has thanked: 2186 times
- Been thanked: 1585 times
Re: The Great Kurath Re-Tubing
That is very easy to do. They say they are not working together, but the parts are IDENTICAL and FULLY INTERCHANGEABLE. So someone copied someone else, here. I really like the nickel silver barrel on the I.I. kit, but it cannot accept the larger 5.5 mm rod. I may drill some of them out And break up the all-brass look. Hmm… more stuff to think about…
I have not yet silver soldered any of these. When I built these I did not have a heat problem, except for the shortest one. And that one, my friend, as a BEAR to keep assembled properly and not accidentally solder the whole thing into one piece. So for these four I am about to build, and maybe for the three I have right now, I think this would be an excellent idea.
I'll post about it if I do it. Thanks for the brain fodder…

- the elephant
- Posts: 3775
- Joined: Thu Aug 13, 2020 8:39 am
- Location: Yazoo City, Mississippi (stop laughing!)
- Has thanked: 2186 times
- Been thanked: 1585 times
Re: The Great Kurath Re-Tubing
People…
PROOFREAD YOUR WORK! This monstrosity is in a common and expensive fake book. People sightread these at gigs, so this could cause some real trouble to a singer. Regardless, this is hilarious to me!
PROOFREAD YOUR WORK! This monstrosity is in a common and expensive fake book. People sightread these at gigs, so this could cause some real trouble to a singer. Regardless, this is hilarious to me!


- Tubajug
- Posts: 779
- Joined: Thu Aug 13, 2020 10:27 am
- Location: Nebraska
- Has thanked: 236 times
- Been thanked: 219 times
Re: The Great Kurath Re-Tubing
I also like that those Edwards parts come with flanges already attached (unless you're matching diamond feet). 

- These users thanked the author Tubajug for the post:
- the elephant (Tue Dec 21, 2021 5:16 pm)
Jordan
King 2341 with Holton Monster Eb Bell
King/Conn Eb Frankentuba
Pan AmeriConn BBb Helicon
Yamaha YBB-103
"No one else is placed exactly as we are in our opportune human orbits."
King 2341 with Holton Monster Eb Bell
King/Conn Eb Frankentuba
Pan AmeriConn BBb Helicon
Yamaha YBB-103
"No one else is placed exactly as we are in our opportune human orbits."
- bloke
- Mid South Music
- Posts: 20735
- Joined: Thu Aug 13, 2020 8:55 am
- Location: western Tennessee - near Memphis
- Has thanked: 4288 times
- Been thanked: 4548 times
Re: The Great Kurath Re-Tubing
On bus trips (even [so-called] "grown-ups" orchestra run-outs), to pass the time, we Mefis-area fokes sing songs in that manner (NO FAIR looking at the melody notes nor lyrics !!!the elephant wrote:video

One favorite is "Take Me Out To The Ballgame".
ie. "Me out to the ballgame take..." (etc...)
and then:
"Out to the ballgame take me..."
"To the ballgame take me out..."
etc., etc., etc...



bloke "It sorta woiks ya broin...know wut I mean, mian?"
- the elephant
- Posts: 3775
- Joined: Thu Aug 13, 2020 8:39 am
- Location: Yazoo City, Mississippi (stop laughing!)
- Has thanked: 2186 times
- Been thanked: 1585 times
- the elephant
- Posts: 3775
- Joined: Thu Aug 13, 2020 8:39 am
- Location: Yazoo City, Mississippi (stop laughing!)
- Has thanked: 2186 times
- Been thanked: 1585 times
Re: The Great Kurath Re-Tubing
In the Army, our very similar game was to loudly sing our parts to whichever march was called, but in 5/8, adding an eighth to cut-time or dropping one from 6/8.
Lots of fun!
Lots of fun!
- These users thanked the author the elephant for the post:
- bloke (Tue Dec 21, 2021 5:43 pm)

Re: The Great Kurath Re-Tubing
I got curious about this. According to a blog post I found, Sunflag is the only company that still sells legit JIS tools. They're carried domestically in case you still want/need a set of the drivers.the elephant wrote: ↑Tue Dec 21, 2021 9:47 am I hate these. I cannot find a JIS screwdriver of the right size head and length to be of any use to me. I have a German WiHa screwdriver that fits JIS pretty well, but it is really long, so not a good gig bag choice.
- These users thanked the author hrender for the post:
- the elephant (Tue Dec 21, 2021 9:39 pm)