putting together sousaphone necks out of scraps
Posted: Sat Sep 21, 2024 7:57 pm
I posted a few pictures on the Facebook Frankentubas page, and I don't think I'm going to post any here.
...I just don't enjoy always having $1,000 to $1,500 (dealer cost) worth of King, Conn, Jupiter, and Yamaha necks available once the summer repair season is over, and the afterglow marching repair season dwindles on through Thanksgiving. I don't like being stuck with all that stock that's mostly not going to get sold until the following June, and not paid for probably until 2025 August or September.
I've got parts bins for all the various makes of sousaphone necks, and - so far, and in the past two weeks - I have put together a 20K neck that looks convincingly like new, a King neck - same, and - today - a Jupiter neck which was needed by 8:30 tonight for a marching band contest which - serendipitously - was only 35 minutes from here.
If things work out, I'll have enough salvage parts to make it through October and November, but - admittedly - I'm already having to get pretty creative. As just one example, to finish the King neck, I had to cut off a piece of small side reverse outside slide tubing from a King trombone bell section main tuning slide, because it was the same tubing size that they used for the male insertion part on the sousaphone neck. That customer did get an upgrade on that, because the trombone tuning slide part is made of nickel, instead of brass.
I've employed this strategy for two years (originally prompted by factories not being open very much and not making very much stuff, due to the worldwide economic shutdown behavioral experiment) - this being the third year and deciding to continue on with this strategy, and it is allowing me to keep more money in the bank rather than in parts stock, and - much more importantly- it's green.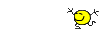
...I just don't enjoy always having $1,000 to $1,500 (dealer cost) worth of King, Conn, Jupiter, and Yamaha necks available once the summer repair season is over, and the afterglow marching repair season dwindles on through Thanksgiving. I don't like being stuck with all that stock that's mostly not going to get sold until the following June, and not paid for probably until 2025 August or September.
I've got parts bins for all the various makes of sousaphone necks, and - so far, and in the past two weeks - I have put together a 20K neck that looks convincingly like new, a King neck - same, and - today - a Jupiter neck which was needed by 8:30 tonight for a marching band contest which - serendipitously - was only 35 minutes from here.
If things work out, I'll have enough salvage parts to make it through October and November, but - admittedly - I'm already having to get pretty creative. As just one example, to finish the King neck, I had to cut off a piece of small side reverse outside slide tubing from a King trombone bell section main tuning slide, because it was the same tubing size that they used for the male insertion part on the sousaphone neck. That customer did get an upgrade on that, because the trombone tuning slide part is made of nickel, instead of brass.
I've employed this strategy for two years (originally prompted by factories not being open very much and not making very much stuff, due to the worldwide economic shutdown behavioral experiment) - this being the third year and deciding to continue on with this strategy, and it is allowing me to keep more money in the bank rather than in parts stock, and - much more importantly- it's green.
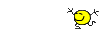