The Great Kurath Re-Tubing
- the elephant
- Posts: 3777
- Joined: Thu Aug 13, 2020 8:39 am
- Location: Yazoo City, Mississippi (stop laughing!)
- Has thanked: 2187 times
- Been thanked: 1585 times
-
- Posts: 465
- Joined: Sun Nov 20, 2022 3:09 pm
- Has thanked: 18 times
- Been thanked: 117 times
Re: The Great Kurath Re-Tubing
Just watched your video and had a crazy thought. What about using a cable, like a bicycle brake cable as your "rod?" Put the spring and lever somewhere near the valve and run the cable any way that makes sense to wherever you want the finger lever. Im kinda nuts. But?
Sent from my SM-J327VPP using Tapatalk
Sent from my SM-J327VPP using Tapatalk
Meinl Weston 2145 CC
King Symphonic BBb circa 1936ish
Pre H.N.White, Cleveland Eb 1924ish (project)
Conn Sousaphone, fiberglass 1960s? (Project)
Olds Baritone 1960s?
Hoping to find a dirt cheap Flugabone
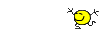
King Symphonic BBb circa 1936ish
Pre H.N.White, Cleveland Eb 1924ish (project)
Conn Sousaphone, fiberglass 1960s? (Project)
Olds Baritone 1960s?
Hoping to find a dirt cheap Flugabone
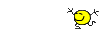
- the elephant
- Posts: 3777
- Joined: Thu Aug 13, 2020 8:39 am
- Location: Yazoo City, Mississippi (stop laughing!)
- Has thanked: 2187 times
- Been thanked: 1585 times
Re: The Great Kurath Re-Tubing
That has been suggested to me but is a little too out there for my personal tastes, and I used to work on mountain bikes and compete in NORBA back in the nineties, and I have never come across a cable system that did not have at least some slop due to cable flex. Even when heavily "tacked down" this happens. I generally have less than a half mm of slop in my levers; they are *very* direct.
The issue gets better with restraints on the cable, but what do I use for that: zip ties? I would have to make brass retainers that would be soft soldered in place and the flanges would have to be brazed to the restraint. The restraint would have to be removable or two parts screwed together or you cannot remove the cable from the horn when doing a chemical dip. The slop is from the bead crimper tool used at the ends of the wire: there is a built-in 1mm (at least) of slop because of how the tool works. Also, over time there would most certainly be some cable stretch; even a millimeter will make the cable too sloppy to use, and I don't want to have to cut and crimp a new cable every few years.
My stuff ends up working as it came from the factory that way, and it usually looks about that good, too, once fully cleaned up. The issue is simply the distance between the lever and the stop arm, as well as the offset to the side of the lever, the angle of the lever, and the tangled mess the rod has to travel through to make it from one object to the other. And finally, what I have been struggling with for so long: It has to be bent in a shape that can be routed through the rat's nest of tubes and braces to allow for installation or removal.
I *finally* have all my i-dotting and t-crossing done.
Thanks though. It was not a weird suggestion, as others have suggested and I have also considered it. I'm just a solid-metal-to-solid-metal-connection kind of guy, I guess, heh, heh…
I am currently scheming for a replacement for the support block that will be great if I can make it work, but it will not be happening at all until this summer. I need this tuba to be working right now! ACK!
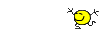
The issue gets better with restraints on the cable, but what do I use for that: zip ties? I would have to make brass retainers that would be soft soldered in place and the flanges would have to be brazed to the restraint. The restraint would have to be removable or two parts screwed together or you cannot remove the cable from the horn when doing a chemical dip. The slop is from the bead crimper tool used at the ends of the wire: there is a built-in 1mm (at least) of slop because of how the tool works. Also, over time there would most certainly be some cable stretch; even a millimeter will make the cable too sloppy to use, and I don't want to have to cut and crimp a new cable every few years.
My stuff ends up working as it came from the factory that way, and it usually looks about that good, too, once fully cleaned up. The issue is simply the distance between the lever and the stop arm, as well as the offset to the side of the lever, the angle of the lever, and the tangled mess the rod has to travel through to make it from one object to the other. And finally, what I have been struggling with for so long: It has to be bent in a shape that can be routed through the rat's nest of tubes and braces to allow for installation or removal.
I *finally* have all my i-dotting and t-crossing done.
Thanks though. It was not a weird suggestion, as others have suggested and I have also considered it. I'm just a solid-metal-to-solid-metal-connection kind of guy, I guess, heh, heh…
I am currently scheming for a replacement for the support block that will be great if I can make it work, but it will not be happening at all until this summer. I need this tuba to be working right now! ACK!
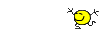

- bloke
- Mid South Music
- Posts: 20748
- Joined: Thu Aug 13, 2020 8:55 am
- Location: western Tennessee - near Memphis
- Has thanked: 4288 times
- Been thanked: 4554 times
Re: The Great Kurath Re-Tubing
Yep. Devices that would take up cable slack (due to stretching over time) would probably need to be something like an additional roller wheel with an adjustable (or spring tensioned) height soldered on to something, and an additional roller wheel is just going to add more friction and slow down the action or define that the action requires a much stronger spring to overcome the additional friction.
With a front action piston tuba, it's really challenging to locate the rotors past the pistons and work out lever systems that are viable, particularly with two. Wade has got a challenge there, but he's up to it.
I don't know if this would have made it any easier, and there might be other obstructions - such as body bows or first valve circuit or whatever, but I might have looked at the cheesy Yamaha stick-them-in-the-mouthpipe solution... but I still don't know for sure how I would have run two levers into a mouthpipe location from the left hand.
...and - as long as tubas are (as the shortest ones are still as long as bedrooms in some houses), I've always considered dependent rotors to be cop-outs, and of limited use.
With a front action piston tuba, it's really challenging to locate the rotors past the pistons and work out lever systems that are viable, particularly with two. Wade has got a challenge there, but he's up to it.
I don't know if this would have made it any easier, and there might be other obstructions - such as body bows or first valve circuit or whatever, but I might have looked at the cheesy Yamaha stick-them-in-the-mouthpipe solution... but I still don't know for sure how I would have run two levers into a mouthpipe location from the left hand.
...and - as long as tubas are (as the shortest ones are still as long as bedrooms in some houses), I've always considered dependent rotors to be cop-outs, and of limited use.
- These users thanked the author bloke for the post:
- the elephant (Mon Jan 23, 2023 11:07 am)
- the elephant
- Posts: 3777
- Joined: Thu Aug 13, 2020 8:39 am
- Location: Yazoo City, Mississippi (stop laughing!)
- Has thanked: 2187 times
- Been thanked: 1585 times
Re: The Great Kurath Re-Tubing
I realized that this thread, by title, was completed last year! Since then I have added pages to it about the addition of the 6th valve.
That really needs its own thread.
All I have left of *this* project is to shorten the 2nd slide by about half of an inch, and then all the hated and ignored cleanup work to all the solder joints, and then experiment with that Rennaissance Paste Wax stuff or even lacquering the valveless bugle.
So I am wrapping up the thread regarding the very successful adjustments to the valve section bores to help even out the careless taper.
[I still believe that all this weirdness was designed around his own not-yet-built piston set, and that the purchased Nirschl piston set was probably sort of "pasted in" as a "good enough" substitute. (I keep seeing all sorts of compromises made that make me suspect this is one of the better prototypes sent out for Dan P. to evaluate before serial production began.) I worked out the taper *gaps* as best I could and used some beautiful Miraphone nickel silver tubing sets for that purpose. I believe the tuba looks a lot better, too. It certainly plays better now. Making alterations to the taper was risky, and the intonation *was* affected, but I think 95% of the changes were improvements, and 5% were new issues or issues that got worse.]
The response in the low register is improved substantively, but I am still unhappy with low Bb. I suspect the tightness in that one note to be due to the shape of the 5th slide loop. (It is important to note that he changed this design in his later Willson 3200FA5 at least three times, based on photos. So he was trying to figure out the same issue, because there was NOTHING wrong with the 5th loop wrap, physically, and all of these horns share that same rotten low Bb. I think his final version of that slide loop might have nailed it. However, I suspect that being attached to his weird ROTAX valve prevented this from being completely fixed. I will try to recreate that version of the 5th slide at a later date, using my excellent Miraphone rotary valve.)
So that is it. This thread probably won't see much updating any longer.
Please look for my new thread dedicated to the 5th and 6th valves.
Thanks so much for reading this endless tome.
Wade
That really needs its own thread.
All I have left of *this* project is to shorten the 2nd slide by about half of an inch, and then all the hated and ignored cleanup work to all the solder joints, and then experiment with that Rennaissance Paste Wax stuff or even lacquering the valveless bugle.
So I am wrapping up the thread regarding the very successful adjustments to the valve section bores to help even out the careless taper.
[I still believe that all this weirdness was designed around his own not-yet-built piston set, and that the purchased Nirschl piston set was probably sort of "pasted in" as a "good enough" substitute. (I keep seeing all sorts of compromises made that make me suspect this is one of the better prototypes sent out for Dan P. to evaluate before serial production began.) I worked out the taper *gaps* as best I could and used some beautiful Miraphone nickel silver tubing sets for that purpose. I believe the tuba looks a lot better, too. It certainly plays better now. Making alterations to the taper was risky, and the intonation *was* affected, but I think 95% of the changes were improvements, and 5% were new issues or issues that got worse.]
The response in the low register is improved substantively, but I am still unhappy with low Bb. I suspect the tightness in that one note to be due to the shape of the 5th slide loop. (It is important to note that he changed this design in his later Willson 3200FA5 at least three times, based on photos. So he was trying to figure out the same issue, because there was NOTHING wrong with the 5th loop wrap, physically, and all of these horns share that same rotten low Bb. I think his final version of that slide loop might have nailed it. However, I suspect that being attached to his weird ROTAX valve prevented this from being completely fixed. I will try to recreate that version of the 5th slide at a later date, using my excellent Miraphone rotary valve.)
So that is it. This thread probably won't see much updating any longer.
Please look for my new thread dedicated to the 5th and 6th valves.
Thanks so much for reading this endless tome.

Wade

- the elephant
- Posts: 3777
- Joined: Thu Aug 13, 2020 8:39 am
- Location: Yazoo City, Mississippi (stop laughing!)
- Has thanked: 2187 times
- Been thanked: 1585 times
Re: The Great Kurath Re-Tubing
As I stated above: I won't resurrect this old thread unless I have something further to share.
Today I fixed a LOT of niggling pitch issues all over the horn by shortening the 2nd slide. I had chopped the second slide and added a much more robust pull ring that was larger, longer, and had a more solid flange to the slide crook. However, I was too busy to remove the outer tubes (and the brace to the 3rd slide) to shorten and reinstall them.
Today I did that, and I also worked on the alignment of the upper 3rd slide, which looked a little crooked despite having an excellent, smooth pull. It was a tiny bit off, but it looked wonky because the two tubes had brace flanges at opposite ends that stuck out on opposing faces of the tubes, so they genuinely looked very far out of alignment. After measuring several times and studying some photos I decided to get out the granite surface plate, and the adjustable parallels, and line up the slide itself a little better. (It *was* off, being nicely parallel but out of the plane by about a quarter of a millimeter. Once I was happier with the slide I then was able to heat the short tube's joint with the piston casing as well as the adjustable brace until I got that satisfying *tink* that happens when the pressure is released from a slightly bound-up joint.
It is amazing to me every time I correct a too-long slide that it affects so much of the horn's scale. I have been happily playing stuff for the last two hours with no lipping or <ahem> wincing. What a fun tuba!
Finally, The new 2nd slide pull ring I made earlier ended up with the long rod slightly crooked. Once I corrected the subtle slide alignment issue, unskewed the slightly askew rod, and then shortened the slide by 10mm the visual difference is subtle but real. And I really need to get a long break from work to take this horn apart and fully clean up all the exposed and ugly work. (1st week of June?)
Further, there was a definite leak somewhere near the 2nd valve. It seemed to leak on the open horn but was worse with the 2nd or 1st down. I suspect a cracked knuckle between the two pistons. Anyway, the heating with the torch seems to have blocked up whatever it was. I cannot explain what I did, which was nothing intentional, to fix this, but it is a big difference. One of the outer tubes was leaking at the valve case, I think, and that was the major issue, but something else changed in the tone and the whole horn plays with a better focus. I can't explain it, but I screwed up in reverse, I guess. Whatever — I'll happily take it.
Before…

After…

Slide and brace off…

Cutting the outer tubes…

Slide cut…

This looks better…

Today I fixed a LOT of niggling pitch issues all over the horn by shortening the 2nd slide. I had chopped the second slide and added a much more robust pull ring that was larger, longer, and had a more solid flange to the slide crook. However, I was too busy to remove the outer tubes (and the brace to the 3rd slide) to shorten and reinstall them.
Today I did that, and I also worked on the alignment of the upper 3rd slide, which looked a little crooked despite having an excellent, smooth pull. It was a tiny bit off, but it looked wonky because the two tubes had brace flanges at opposite ends that stuck out on opposing faces of the tubes, so they genuinely looked very far out of alignment. After measuring several times and studying some photos I decided to get out the granite surface plate, and the adjustable parallels, and line up the slide itself a little better. (It *was* off, being nicely parallel but out of the plane by about a quarter of a millimeter. Once I was happier with the slide I then was able to heat the short tube's joint with the piston casing as well as the adjustable brace until I got that satisfying *tink* that happens when the pressure is released from a slightly bound-up joint.
It is amazing to me every time I correct a too-long slide that it affects so much of the horn's scale. I have been happily playing stuff for the last two hours with no lipping or <ahem> wincing. What a fun tuba!
Finally, The new 2nd slide pull ring I made earlier ended up with the long rod slightly crooked. Once I corrected the subtle slide alignment issue, unskewed the slightly askew rod, and then shortened the slide by 10mm the visual difference is subtle but real. And I really need to get a long break from work to take this horn apart and fully clean up all the exposed and ugly work. (1st week of June?)
Further, there was a definite leak somewhere near the 2nd valve. It seemed to leak on the open horn but was worse with the 2nd or 1st down. I suspect a cracked knuckle between the two pistons. Anyway, the heating with the torch seems to have blocked up whatever it was. I cannot explain what I did, which was nothing intentional, to fix this, but it is a big difference. One of the outer tubes was leaking at the valve case, I think, and that was the major issue, but something else changed in the tone and the whole horn plays with a better focus. I can't explain it, but I screwed up in reverse, I guess. Whatever — I'll happily take it.
Before…

After…

Slide and brace off…

Cutting the outer tubes…

Slide cut…

This looks better…

